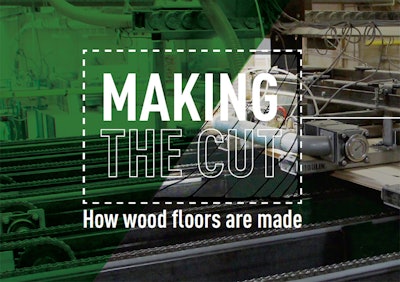
It's a scorching July afternoon in Westby, Wisconsin, a Norwegian hamlet of fewer than 2,200 people nestled in the rolling hills of the Coulee Region of west-central Wisconsin. Untouched by the glacier, the terrain is rugged with steep timber-lined ridges, intermixed with the green of rolling farm fields. It's noticeably peaceful—until one steps out on the manufacturing deck of Lacrosse Hardwood Flooring.
Within this 45,000 square-foot manufacturing space, over seven semi loads of lumber are processed into 55,000 square feet of flooring every day. What may
sound like mechanical chaos to the uninitiated is the sound of order and productivity to Lacrosse Division Manager Paul Ostlund. "If it's quiet, something bad has happened," he says. That "something bad" could be a problem with any of the over 2 million moving parts within the mill that keep hardwood flooring pouring out of this high-tech manufacturing facility.
The seemingly straightforward endeavor of manufacturing solid hardwood flooring relies on the constant vigilance of machine operators, the tenacity of a highly skilled maintenance department and the watchful eye of production managers who direct product flow and line speed like an NFL offensive coordinator on game day … except this game is played nine hours a day, five days a week to keep up with demand.
In an environment where the tiniest vibration can bring the wheels of production to a grinding halt, it quickly becomes clear that producing hardwood flooring is not for the inattentive or the faint of heart.
Lacrosse Hardwood Flooring took Wood Floor Business on an in-depth tour of its Westby, Wisconsin manufacturing center to show how wood flooring is made.
To reduce end splits, every board has blue end-wax applied to slow down the wicking process.
Lumber at the gate: receiving 90,000 board feet per day
Lacrosse receives seven semi loads of lumber per day from its company-owned dry kilns and sawmills throughout Wisconsin.
All of Lacrosse's lumber comes from the Great Lakes region and includes white oak, red oak, walnut and hickory. Upon arrival, each load is scaled and inspected for grade, moisture content and manufacturing quality by three National Hardwood Lumber Association inspectors.
Kiln drying quality is a critical part of the company's quality assurance program, as lumber that is too high or too low in moisture content impacts yield, grade and the quality of the finished product, Ostlund says. Lumber loses its moisture 10 times faster through the ends than edges or faces of the boards, so controlling moisture starts the day the lumber is received at the dry kilns. To reduce end splits, every board has blue end-wax applied to slow down the wicking process as the lumber sits in the air yards before kiln drying.
(1) The gang-rip saw computer and infeed.
(2) A board exits the gang-rip saw.
Sizing and shaping the boards: ripping and side-matching
In the flooring mill, packs of random-width lumber are unstacked on mechanical tilt hoists that separate the boards into an organized, never-ending sheet of lumber destined for twin computer-optimized gang-rip saws that maximize yield and value while ripping the boards to consistent widths (photo 1) for further processing at the side matchers.
The constant "zing" of over 40 boards per minute passing through multiple rip blades sounds like an orchestra continuously tuning its instruments. Lasers from the saw feeders illuminate the best solution for each board, providing the saw operators a visual verification of what the computer has determined. These operators must then make an instant decision to accept or correct the computer's analysis based on many factors that impact the final product.
After the boards emerge from the rip saw (photo 2), the piling staff sorts the material for the nine widths of flooring produced at the mill. The ripped material then sits for 48 hours while any stress that may be in the ripped lumber is relieved before machining through the side matchers.
Some manufacturers run their rip lines and side-matchers together, which eliminates extra handling, but the company feels doing them separately offers the greatest quality across its large variety of products, Ostlund says.
(3) An automatic tilt-hoist down-stacks boards onto the side-match conveyor.
At the side-matchers, ripped lumber is down-stacked through automatic tilt-hoists (photo 3) and unscramblers to feed a constant ribbon of lumber through the two side-matchers that process lumber—creating the side-match and also planing it—at 600 lineal feet per minute (photos 4-5). Each of the 140 cutter knives on two side-matchers are balanced within 2⁄10 of a gram of each other, or 1⁄5 the weight of a dollar bill.
(4) Inside the side-matching machine.
(5) Boards exit the side-matching machine.
Defecting and optimizing at 600 feet per minute.
Immediately after side-matching, a robotic vacuum lifter picks up sheets of side-matched strips (photo 6) and transports them to the infeed of the EBI Inspector Scanner, which optimizes grade and yield while looking for imperfections within the wood that do not belong in any of the company's finished grades of flooring (photo 7). The EBI scanner was part of a $2 million upgrade to the mill earlier this year.
(6) A robotic vacuum lifts sheets of side-matched boards.
(7) The EBI Inspector scanner.
The scanner uses multiple measurement lasers and high-speed cameras to instantly detect every aspect of every inch of flooring that passes through it. It monitors all critical measurements of the flooring profile within 3/1000 of an inch and evaluates thousands of measurements per second. As the boards fly through the scanner, the computer applies small luminescent marks detected by Lacrosse's optimizing defect saws. As the flooring strips travel through the saws, cameras detect the lumen marks and send a signal to the computers that tell the saw blades when and where to cut, eliminating defects and creating consistency in the grades.
As boards move out of the defect saws, they travel like soldiers in formation marching to the end-matcher for the final machining process. Each board passes through the first cutting station that precision-squares the end and applies the end-match groove (photo 8). The boards are then shifted automatically to the squaring trimmer that precision-squares the other end of the board and applies the tongue of the end-match.
(8) Boards travel on the end-matcher.
(9) The robotic nesting machine calculates bundles of flooring.
The final stretch: getting the grade
As finished flooring boards exit the end-matcher at 130 pieces per minute, mill inspectors give each piece a final grade based on length, color, character and clarity.
Boards are then fed into six robotic nesting machines that constantly monitor average length, piece count and minimum and maximum length to ensure every bundle is packaged the same (photo 9).
With more than 100 square feet of flooring per minute coming out of the production line, final packaging has to flow without interruption. Units are tagged for identification, strapped (photo 10), shrink-wrapped for protection and given the final inspection. For complete accountability, the shrink-wrapping team initials each unit placard as their seal of approval.
(10) Workers use the strapping machine for bundles of flooring.
After the whirlwind of the production lines fade into the background, flooring enters the finished products warehouse where stacks upon stacks of flooring (photo 11) are ready to ship, but the buzz of manufacturing is still not quite out of range. "We don't have any meditation or quiet rooms like at Google or Microsoft. Silence is our enemy." Ostlund chuckles.
(11) Stacks of flooring are placed in the finished products warehouse, ready to be shipped.
Quality control: Keeping things afloatBrittini Knight, the Lacrosse quality assurance coordinator, keeps track of hundreds of individual spot inspections and hundreds of thousands of computer-monitored inspections every day. Graphing and cataloging measurements to spot a trend is essential; Knight even monitors the relative humidity and gallons per day of water removed by the dozen dehumidifiers within the facility. At 6,000 square feet per hour, everything is happening really fast, creating a tremendous revenue stream, and a one-minute problem can contaminate thousands of dollars of flooring. To support an average of $240 per minute of product revenue, a highly experienced and trained maintenance team works overlapping shifts that provide 22 hours per day of support, and an online maintenance management software system keeps track of millions of moving parts, including more than $250,000 of on-hand spare parts and the preventive maintenance schedules for hundreds of machines. If a part like a gear or bearing has a 12-month wear life, the company replaces it at 11.5 months to ensure even the smallest parts don't shut the mill down. Change-overs are a killer, says Lacrosse Division Manager Paul Ostlund. When the production line has to change widths or species, the line has to be purged and machines reset to accommodate the next product. The large digital timer on the wall keeps track of the change-over time, which is down time with no revenue. The team works feverishly to execute 8- to 10-minute change-overs. When the clock gets to 15 minutes, production managers know Ostlund is getting real antsy and an "uncomfortable" conversation is imminent, he says. The company's on-site logistics department serves as "air traffic control" of product flow in and out of the mill. More than 600 semis per month must be coordinated to service the facility, delivering lumber, parts and supplies and shipping over a million square feet of flooring and over 2,000,000 pounds of sawdust each month. |
Employee retention: 'They're not easy jobs'Craigslist, Indeed, yard signs, radio ads, newspaper ads and fulltime recruiting. Lacrosse has used them all. Recruiting employees to work in a high-speed flooring mill is a job within itself, says Traci Fredrickson, Lacrosse's office manager, noting that the labor shortage is a problem manufacturers are experiencing around the country. "These are not easy jobs," Lacrosse Division Manager Paul Ostlund admits. "They are livable wage jobs with benefits, but our workers are not getting rich." Much like flooring installers, workers have to have a passion for this type of work. Ostlund says they've failed in the past by starting someone new in a fast-paced position too quickly. "We can't just throw them into the 'mosh pit' of manufacturing, we have to ease them into this environment a little bit at a time," says Jeff Traeder, the company's rough mill production manager. "Before we interview a candidate, we take them on a tour so they can get an idea of what this is going to be like." The company makes an effort to focus on the morale of the entire staff with its "Circle of Continuity" problem-solving group that focuses on SAMS: Safety, Accuracy, Morale, Speed, which aims to keep the entire team focused on the company goals. The company also offers a $150 per-pay-period perfect attendance bonus. "It's a method that has had some success and it's a strong motivator," Ostlund says. Four years ago, the company also started offering "Westby Bucks," a sort of "Monopoly money" given out for perfect attendance, years of service, exceptional effort and other positive contributions to the team. Employees can redeem these bucks for any number of items such as company logo clothing, tools, sporting goods, even iPads and extra paid vacation days. While the longer term incentives have helped with staffing, the first few weeks of employment at the mill are a critical period, Ostlund says. "If we can keep them for a month, the chances are much higher that we've got them," he says. "When we lose them, we typically lose them in the first few weeks, so we are always working on retention." Nothing can prepare a new employee for the constant thundering noise of productivity, though. Lacrosse Production Manager Brett Olson compares the sounds of the mill's churning with the way a teenager's heavy metal music sounds to a parent. But it's "music to our ears," he notes, because "no one gets paid till the flooring gets made." |
Watch the video version of WFB's tour of Lacrosse Hardwood Flooring's Wesby, Wis., manufacturing facility here: