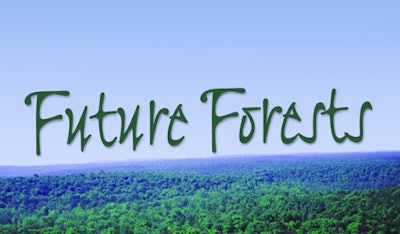
Mention a timber harvest, and most people envision a clear cut-nothing but stumps left in what appears to be total destruction. In the case of trees harvested to supply the domestic hardwood flooring industry, however, that's rarely the case. Today's hardwood forests that are managed for timber production are usually carefully monitored and harvested for sustainability. After the loggers move out, a casual onlooker may not even recognize that the forest was recently harvested.
To observe hardwood forest management firsthand, Hardwood Floors spent a day in a northern Wisconsin forest managed by Laona, Wis.-based Nicolet Hardwoods Corporation and its forester, Al Murray. Based in the heart of the Nicolet National Forest, the company owns and manages about 40,000acres, and is a supplier to sister company WD Flooring, also based in Laona. In this area of the state, about 75 percent of the people make their living off timber production, either directly or indirectly.
Nearly 99 percent of the company's harvest is the result of single-tree selection—the forester goes through the woods ahead of time and marks which trees should be cut (visible in this photo marked with orange paint):
In Wisconsin, the concept of sustainable forestry management and selective cutting dates back to the 1920s, when changes in the tax laws made sustainable harvesting a viable financial option. W.D. Connor, great-grandfather of current Nicolet Vice President Peter Connor, was one of the pioneers in developing the idea. In the first attempts at sustainable harvesting, about 70 percent of the canopy was removed from the forest. Through experimentation using permanent growth plots and different cutting strategies, current harvest schedules were determined.
Today, approximately 30 percent of the canopy is removed every 10 years. Retaining the right amount of shade encourages the remaining trees to grow toward the light and maximize their future value as logs. Removing trees that are dominant in the canopy creates light gaps in the over story, which allows sunlight to reach the forest floor and encourages the creation of a new "age class" of hardwood:
The 10-year harvest rotation maximizes growth while minimizing value loss and mortality. All species of trees are managed regardless of value or size. Lower-value hemlock and soft maple are retained for species diversity. Giant red and white pines, which provide "super canopy" nesting sites for bald eagles, are managed individually and are salvaged when they die.
Professional foresters also take into consideration stand density or basal area—the square footage of stumps on an acre of land. When ready for harvest, a typical acre in this carefully managed forest has about 130 basal square feet per acre, not including trees that are too small to harvest. To maximize growth, after harvest, the acre should have 70 to 80 square feet of basal area. It will take approximately 10 years for this acre to grow back to 130 square feet:
Cutting a tree should always result in more benefit than loss, both from a financial standpoint and for the health of the forest. A guiding factor when choosing trees for harvest is loss of value: Will the tree start to rot, die or otherwise devalue in the next 10 years? If so, it's a likely candidate to be marked for removal. The forester also considers what will replace the tree once it is cut. Are there other nearby trees that will take advantage of the new light and fill the gap? Different trees have different light requirements; yellow birch, for example, thrives in light shade, while hard maple is extremely shade tolerant. If there are several trees of the same size in close proximity, then one or more will probably be marked for cutting to reduce stand density and maximize growth for those left behind. In the photo at left, the tree at the far left is a likely candidate for cutting, as the large lump in its trunk makes its value limited, and there is a straight, healthy tree of comparable size beside it that, if left to grow, will likely continue to increase in value:
Foresters assess the quality of each tree from top to bottom. In this photo, this tree demonstrates why it's important to look up—although the value of this tree appears to be excellent at first, its upper reaches reveal a large crook with associated rot that diminishes its value. There is also a medium sized tree nearby that will replace it:
Loggers are the backbone of forest management, completing the work supervised by foresters. Most loggers lead solitary lives as independent contractors, working alone or in pairs in the forest. A single logger typically cuts about 4,000 board feet of timber per day (a board foot is a lumber measurement represented by 1 square foot of lumber that is 1 inch thick). Nicolet Hardwoods is a licensee of the Sustainable Forestry Initiative (SFI), and under SFI guidelines, loggers must have ongoing training, including first aid and CPR, best management practices for water quality, chainsaw safety and equipment safety. When loggers cut a tree, they try to minimize damage to the surrounding forest—the growing stock. Here, professional logger Francis Bey has carefully made his notch cut and is making his bore cut (a safety practice stressed by SFI) so the tree will fall precisely where he envisioned it:
Timber … the tree falls into a gap in the forest, just where Bey planned:
Bey now "bucks" the tree into usable lengths. He uses a measuring stick, marked with foot measurements, to calculate where he'll cut the tree for maximum log value:
Foresters examine stumps and log piles following cutting. An examination of this stump reveals that the tree was probably cut at the right time: If the tree were left for much longer, the heartwood would grow and radiate out, decreasing the value of the tree:
The maple stump also reveals some "curly" figuring. Curl and bird's-eye are disfigurations that are highly sought after by lumber customers, who pay a premium for them. Scientists are still unsure what causes these natural effects.
Now Bey uses a contraption called a "forwarder" or"skidder" to move the logs from the woods to the logging road:
The compact machine moves through the forest with surprising ease, and most small trees and plants in its wake spring back up after it passes over them:
Such small and maneuverable machines are becoming hard to come by, as the trend in logging is toward larger equipment and higher production. Such large equipment works better in clearcut harvests and places such as pine plantations.
The logs are then stacked next to the logging road according to quality and use: sawlogs, which are logs 12 inches in diameter and up that have quality for lumber; sawbolts, which are sawlog quality but between 8 and 12 inches; and pulpwood, less than 8 inches in diameter or not of sawlog quality:
Saw logs and bolt wood will be transported by truck to the sawmill, where the logs will be sorted by species and quality. Veneer—logs with small hearts and one minor defect or no defects—are set aside to be transported to veneer mills to make fine-quality cabinet faces and tables. Saw logs and bolt wood are sent through the sawmill to make dimension lumber. Pulpwood is transported by truck directly to the paper mill.
With the volume of timber transported, road maintenance is crucial to the logging operation: Nicolet maintains about 200 miles of its own roads, with its own bulldozer, road grader and road-maintenance crew.
With the logs stacked, hindsight is 20/20. The log marked with the orange circle has diminished in value because it was cut after the heartwood spread and began to rot inside the tree. In contrast, the log with the yellow circle is a maximum-value log—large but with the heartwood still contained to a smaller area. The log circled in orange is probably worth around $150, while the other log would be valued at about $300. Large heartwood, interior defects such as ingrown bark, seams and bird peck pockets, as well as exterior defects such as knots, bumps, burls and bark swirls all reduce log value:
This area, cut within the last day, still shows signs of a healthy, productive forest. All age classes, from saplings to medium-sized trees to large trees, are present. After cutting, there is about 1,500 board feet of timber still standing. When the logger returns in 10 years—which will be the eighth time for this area—there will be about 3,000 board feet standing:
Natural Selection
The most careful forest management can’t do anything about Mother Nature: A tornado the previous week wreaked havoc on the forest. From aerial photos of the damage taken by the U.S. Forest Service and the Wisconsin Department of Natural Resources, along with his own observations, Nicolet Hardwoods forester Al Murray estimates that about 1 million board feet of timber was knocked down. Loggers are now concentrating on removing as much of the downed timber as possible before it starts to rot. Murray guesses it will take between 60 to 70 years of management for the forest to recover to the health and age classes it had before the storm:
Sustainable Teak Traditions
While stories often appear in the mainstream news of illegal logging and rampant deforestation in developing nations, there is one such country that has a longstanding tradition of sustainable forestry. Myanmar (formerly Burma), with the most extensive stands of teak in the world, has had a formal forest management plan in place since 1856, when the country was part of the British Indian colony. German forester Dietrich Brandis, now widely considered the father of tropical forestry, was hired to create a plan to manage the teak supply for the future.
Under Brandis’ plan, the forestland was divided into a series of grids. Only teak trees that were over a certain diameter in a grid could be harvested, and the harvest rotated among the grids so that by the time the rotation returned to the first grid, there was a new supply of age-appropriate trees ready for harvest.
Today, although the country is ruled by a military dictatorship, the stringent teak management plans are still in place. “They want to maximize the profitability of that marvelous natural resource, so they do it,” says Chuck Dean, president at Wilmington, N.C.-based Dean Hardwoods, who has visited the country many times and has been buying Burmese teak for more than 30 years.
Harvesting of the logs is done much the same as it was a century ago. Usually, the oldest trees are “girdled,” meaning that a ring is cut into the sapwood around the tree. Once the dead tree has lost the required amount of moisture—typically about three years later—it is cut and pulled out, usually by elephants, which have a minimal impact on the remaining forest. Most often the logs are then transported by floating them down streams and rivers.
In reaction to the Myanmar regime’s human rights violations, among them the repeated arrests of democratic activist and Nobel Peace Prize winner Aung San Suu Kyi, today the U.S. government bans the purchase of teak lumber from Myanmar. So, companies such as Dean’s must buy material from sawmills in Thailand, Malaysia, Hong Kong, Taiwan and other countries that import raw Burmese teak logs. “Unfortunately, it has no economic impact except an adverse one on us, because it makes it more difficult to get the timber,” Dean says.
Although he no longer can buy directly from Myanmar, Dean still has personal relationships with Myanmar officials. “We don’t have any formalized relations with them and don’t directly do business with them anymore, but we have some friends,” he says. “It’s been my naïve hope that through some of those friendships, those person-to-person relationships, gradually the dictatorship would melt into some form of democracy.” —K.M.W.