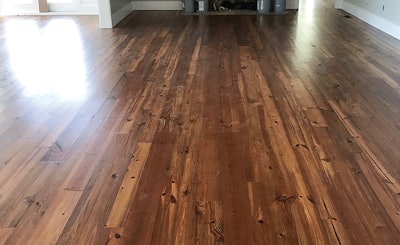
In the wood flooring industry, it can be easy to get wrapped up in the same thing—straight-laid strip or plank flooring—on every job. You get in that predictable rhythm, and it gets boring. One type of flooring that never gets boring for me, though, is reclaimed flooring. Every one of these floors has its own character; you're giving people a truly one-of-a-kind floor. Those jobs are the most satisfying to me and what I enjoy the most in my life as a wood floor pro.
This is one of our best-selling floors: reclaimed barnwood in mixed species. These floors are not culled; they have all of the species that typically came from the property where the barn was built. This floor was sanded on site to the customer's specs and coated with a satin two-component water-based finish.
Today in my contracting and retail business here in Ridgeland, S.C., along the coast, about 40 percent of our jobs are reclaimed projects. It's rare that I get someone coming in the door asking for a floor that's repurposed or sustainable, but when we explain the story of what a reclaimed floor is, and the fact that no new trees are having to be harvested to make the flooring, being reclaimed starts to mean a lot to potential clients and really becomes a selling point.
Additionally, in our market, reclaimed floors fit in well with the traditional look of old-style southern homes that many people are trying to recreate with their new homes. Many houses here are second or third homes for their affluent owners, and these floors have so much character and beauty that they end up being a real conversation piece—the owners can wow their friends at parties and talk about what they have.
Because reclaimed flooring is different and does have its own character, it can't always be treated like a typical wood floor. Following are some things I've learned over the years of working with a lot of reclaimed flooring.
Buy from a reliable supplier
We typically deal in reclaimed barnwood sold as a mixed species or as a red oak/white oak mix that is original-surface. We also do a ton of reclaimed heart pine that is sold in original-surface or clean-milled. When it comes to purchasing and finding a reputable and consistent supplier for reclaimed flooring, that can be a challenge. It has taken me years—and finding out the hard way in some cases—how and what to look for when buying.
I have always bought my materials by the truckload, but at one point I was more hands-on with the process and was buying rough kiln-dried stock and having it processed into flooring by a local mill. One time I bought a truckload of "reclaimed" material from a guy out of state, and it turned out it was new material that had been sitting out in the weather—they were trying to pass it off as reclaimed. Another time I bought a truckload of material and it was infested with bugs, which can be a widespread problem for reclaimed raw material. Yet another time I bought a truckload of material from someone who had been reliable, but he never came through, and I was left out of the money and scrambling to place the order with another supplier because I already had taken deposits on some of the jobs.
Depending on the supplier, waste can be a huge factor when dealing with reclaimed wood. I've dealt with suppliers who had upwards of a 20 percent waste factor—they're running it through a molder as it came off the side of a barn without defecting it. It could have too much overwood or underwood, or it could have a big chunk missing out of it. The supplier is counting that as square footage you're buying. Once you're on site, that definitely adds up, and that's money down the drain.
Buy end-matched product
Currently we buy all of our reclaimed pine and barnwood end-matched, so our waste factor is no more than 10 percent and is usually less. A lot of the good suppliers are selling their reclaimed products end-matched, but in my dealings I've found probably 75 percent of the people selling reclaimed flooring are not end-matching it, which tells you you're going to end up with a lot of waste. If they're end-matching, you're getting a product that's been sorted through and defected, so there is less waste.
Look for quality milling
Of course you want quality milling on any job, but with reclaimed, you're often dealing with an original-surface product that isn't going to be sanded flat. It is important to have consistent milling so you avoid any major overwood or underwood issues that would create lippage and trip hazards. Some of the stuff I've come across can have a 1/4 inch of overwood. That's a real trip hazard and not a practical floor. With the good suppliers I have now, I haven't gotten material that has more than an 1/8 inch of overwood.
Reclaimed floors such as this mixed species floor (left) and red/white oak mix (right) suit the traditional southern aesthetic of the architecture in our area.
Make sure material has been kiln-dried
We have competitors in our market who are selling material right off the side of a barn to go into someone's home—not processed, not kiln-dried, and without any sort of bug treatment. This material has been outside in the elements for hundreds of years in some cases, and it could be infested with anything from ants to cockroaches to powderpost beetles. At the mill, sometimes they will rip the bottom side of reclaimed material clean and open up channels where you might see hundreds of bugs in one board. I don't play around with bugs! You don't want them in your customers' homes, so make sure all material has been properly kiln-dried, killing any infestations.
Installation isn't much different
Once we're on the job site, installing the actual flooring isn't different from installing any other floor. Because the flooring isn't necessarily going to be sanded flat, subfloor prep is extremely important. If we're installing engineered reclaimed flooring on a slab, we're patching and leveling, and if we're nailing down on a plywood subfloor, we use high-quality panels—the brand we use is AdvanTech—that are resistant to moisture. When necessary, we sand down any seams so we have as flat a subfloor as possible. In my experience, acclimation doesn't take as long for reclaimed products; I tend to see far less movement in them versus newly milled flooring.
I'm very particular on my barnwood installs when it comes to board placement and layouts. With these floors, I always find one or two boards when they're delivering the product that have this crazy character to them, and I make sure they go in a visible spot, not in a closet hidden away somewhere. It's more for me than the homeowner, but it's my little touch.
We never use a regular buffer on a reclaimed floor, as it grabs splinters and tears up the floor. For some jobs, a square orbital buffer is the only sander we use.
Don't overthink your sanding process
Sanding reclaimed material always becomes a hot topic when a lot of guys are first introduced to the product, and nine times out of 10 I think they're just overthinking it. On our jobs, the level of sanding is always based on the expectation of the customer. For some reclaimed floors, we do as little as buffing, and for others we sand them just like any other floor.
When people want to preserve all the character of the rough texture, including all the saw kerf, we just use a square orbital buffer (we use the American Sanders OBS). We never use a circular buffer on these floors, because it grabs splinters, creating holes you will have to patch with putty or replace entirely. For floors that are only buffed, we start with 36 on the OBS. People think that sounds like too much, but it isn't—it just takes the dirt off but leaves that patina. Then we'll go to a 60 and 80. There may be some areas where we have to scrape down overwood or palm-sand, but the sanding is very minimal. This type of floor has really done well for us. It does usually produce a much darker floor due to not removing much of the original patina that's on the wood.
A lot of our new-construction jobs in our market (coastal South Carolina) are slab on grade. We recently started offering all of our reclaimed flooring in engineered. On this job both the floor and the stairs are a mix of red oak and white oak, but the flooring is engineered and the treads are solid. This floor was glued and sanded to the customer's specs, then coated with a two-component water-based finish.
Another sanding process we use for reclaimed flooring I like to call "the best of both worlds." This is where we bring the flooring in untouched on the surface from the mill and we basically sand the floor to the customers' specs, which usually results in a much flatter, more practical floor. This gives the customer a more intimate experience and gives them the feeling they are truly getting a one-of-a-kind custom reclaimed floor. With this process, we will typically start out with 40-grit on the big machine. Again, a lot of times people think that's just going to take all of the character away, but it doesn't. These floors have dips and dives and imperfections, so the sander isn't hitting flat across that floor. We'll work from 40 to 80 and finish with 100 on the OBS. It looks great, and it's very simple. Most guys look at me dumbfounded when I tell them about it, because they can't believe it's that simple.
You can use whatever coating you want
We use all types of finish on our reclaimed floors, from hardwax oils to tung oil to oil-based polyurethane and water-based finishes. It's all a personal preference based on the look, budget and expectations of the client. My personal favorite to use on these floors is water-based, which gives them a natural look and an easily maintainable floor that won't inconvenience them over time. I get questioned a lot about how to buff these finishes between coats, and again, we use the square orbital sander. It does what I need it to without tearing up the floor in the process. One thing to keep in mind no matter what finish you use is that these floors will require more finish than a regular floor due to the irregularities and imperfections that make these floors so beautiful and unique.