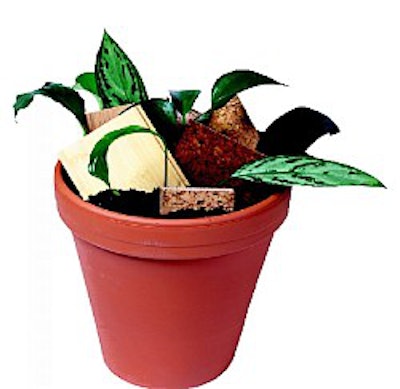
Your phone rings. It's a potential customer who just got back from a trip visiting her long-lost friend 1,200 miles away.
Her friend just had a cork floor installed in her great room. It had a unique pattern and was stained white. And, the friend informed her, no trees were cut down to make the floor. Now she's convinced she wants to rip out her carpeting and put the same exact floor over the slab in her house. "You can do that, right?" she asks.
The next day you get an e-mail from someone across town. It's a potential client building his dream home, and he's focusing on environmental products throughout. He found some information on bamboo on the Internet. He needs 5,600 square feet. "Is it true that it grows again in four years? Can I get the color I want in a 3-inch width?" he asks.
Do you have the answers to those questions? In this age of increasingly educated and environmentally aware customers, wood flooring contractors need to know about more products than ever before. If they don't, they risk losing the business to the contractor down the street who does. Two of the species gaining increased attention are an old favorite, cork, and a relative newcomer, bamboo. Neither one are technically wood in the traditional sense—cork is tree bark, and bamboo is a grass. Both have impeccable environmental stories to tell and versatile applications as "wood" flooring.
Calling for cork
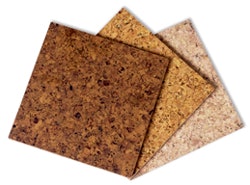
Cork is actually the bark from a type of oak tree found mostly in Portugal and Spain. When the trees reach about 20 years old, the bark may begin to be harvested. About two-thirds of the bark is carefully stripped off the tree, leaving an important inner bark layer that protects the tree. The process may be repeated every nine years. When the trees reach 150 years old, they need to be replaced.
Once the bark is removed, the cork is ground up, reconstituted with a binder and formed into blocks. As part of the binding process, the blocks are then heated; the length of time they are heated determines the final color of the tiles. The resulting color is consistent throughout the depth of the product.
As the product's popularity increases, so do the options for cork flooring and the number of manufacturers. Be sure to choose a reliable producer that can be trusted to stand behind the product. The traditional cork floor has a wax finish and comes in square-edge tiles. That floor is still popular, especially with those choosing cork for its environmental advantages, but today modern urethane-type finishes and floating floors also are available.
The size and shape of the ground-up cork pieces may vary, offering a wide variety of different looks, and the range of colors available allows for installers to be creative in designing different patterns. Tiles are solid cork—not engineered layers—and range in thickness from about 3/16 to 5/16 inch with varying widths. Unfinished cork tiles are available, as well. Installers who favor the product tout not only its unusual style, but also its warmth, sound-deadening capabilities, and even non-skid characteristics.
Cork floats
The cardinal rule of installing cork tiles is to check for moisture—in the subfloor, in the adhesive and in the air. Cork expands and contracts rapidly, so installers who are used to bending the rules of job-site moisture and acclimation are in for a surprise with a cork floor. If it's installed in wet conditions, you won't have to wait a few weeks or months to get the angry call about cupping—you'll see it for yourself the next morning when you return to the job site. That's why installers must be diligent about checking the subfloor for moisture. Job-site humidity also should be checked. If the floor is going down in a region with large seasonal swings in humidity levels, manufacturers recommend installing the floor in the least humid conditions the floor will experience. For example, a cork floor being installed on a humid Chicago summer day needs a job site with the air conditioning turned up to simulate the low humidity levels of winter.
Adhesive is another area where contractors must play by the rules. When installing cork, the manufacturer's directions concerning adhesive type, trowel and spread rate should be followed to the letter. Even when using recommended adhesives, some contractors still do a test sample to see how the products react to each other. Waterbased adhesives are not recommended for use with cork. Moisture-cured urethanes are recommended, but shouldn't be used as a wet-lay application; rather, manufacturers recommend letting it tack slightly before installation. Dry-lay adhesives also are recommended. As usual, make sure the slab hasn't been treated with any sealers that will cause adhesion problems.
With all moisture and adhesive issues out of the way, you might think you're ready to start installing. But you need to perform one more crucial step: double-checking the subfloor for imperfections. As always, the subfloor should be flattened to industry specifications. This is especially important with cork. Much like sheet vinyl, cork tiles transfer any bumps or ridges on the subfloor to their own surface, so take the time to scrape away paint drips or other problem areas on the subfloor.
Gently abrasive
Even many experienced sanders choose to install prefinished cork, saying that the extra labor of sanding an unfinished cork floor isn't worth the hassle. That said, even those prefinished floors must be sanded and recoated at some point. It's a job that needs to be done carefully. The good thing is that because their color is consistent through the depth of the product, cork floors of a particular color or laid in a certain pattern keep their color, even when sanded.
The most important guideline for sanding cork is to use the finest grit possible to get the job done. For taking off old finish, most contractors start as fine as 100 or 120 grit. Resist the temptation to do it faster using a lower grit and fewer abrasives, as the risk of chewing through the cork is too great. Only the most experienced sanding professionals should attempt to use a big machine on a cork floor; three-disc sanders, oscillating sanders and buffers are the recommended machines. Edgers should be used only with a maroon or white backing pad. For wall lines and corners, small orbital sanders or simply hand-sanding work the best, as handscrapers tend to gouge the cork. Be careful when you're working with big, heavy tools on the floor. The most fastidious contractors lift and carry their equipment across the floor instead of rolling it, thereby sparing the unfinished cork the risk of compression dents.
Be sure to sweep and vacuum meticulously between sandings (use a good quality, soft-bristled vacuum brush). The actual chunks of cork themselves aren't porous, but there are lots of minute nooks and crannies between them, and they hold dust.
Finish it off
If you're refinishing a previously waxed cork floor, you have no choice but to recoat it with a wax finish. That guideline holds true for any wood floor, although contractors sometimes attempt and succeed at recoating a waxed hardwood floor with a urethane-type finish. Few of them would try it with a cork floor, however, as it is nearly impossible to remove all the old wax, making finish contamination inevitable.
Manufacturers recommend any quality hardwood floor finish for use over cork floors. If using a surface-type finish, such as waterbase, oil-modified, conversion varnish or moisture-cure, one method to improve the finish build is to sand the floor to a very fine grit, burnishing the floor and thereby sealing off as many open pores as possible. Contractors also may use more than one coat of sealer before going back on the floor with topcoat layers. When choosing a finish for cork, it is wise to think about the product's elasticity. Keep cork's compression factor in mind and choose a finish that will bend along with the floor instead of breaking. If using waterbased finish, be careful not to apply too much, as it may cause the edges of the tiles to lift, just as any other excess moisture would.
Cork floors may be stained just like any other wood floor as long as a recommended wood flooring stain is used. Giving an extra cushion to dry times is a good idea.
Branching into bamboo
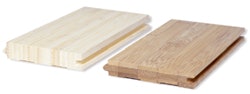
Much like cork, bamboo is regenerated rapidly relative to other wood flooring products. One specific specie—moso—is used for manufacturing bamboo flooring. Grown near the Shanghai region of China, it takes four to six years to reach maturity, at which point it has stalks about 40 feet tall and 6 inches in diameter. Because it's actually a grass, it doesn't need to be reseeded after harvesting, but simply sends up more shoots. In fact, bamboo has its own inherent environmental controls—it grows perfectly well as long as no more than 50 percent of its mature stalks are harvested, but cannot support its root structure if more are cut.
In addition to natural controls on cutting, the communist Chinese government monitors the harvest so carefully that a container of flooring can be traced back to the patch of forest where it came from. The bamboo farmers mark every single stalk of bamboo with their name and the date. Farmers may harvest the bamboo only every two years, may take only stalks that are six years old, and must follow a government-dictated quota. Bamboo poles are dragged for miles out of the mountains, where the farmer is paid by weight. The bamboo's documents follow it through the entire manufacturing process and exportation.
Of the 40-foot hollow poles, bamboo flooring manufacturers use the first 12 to 14 feet, which have walls up to about 1 inch thick. Flat strips are milled from the core of the wall and boiled in a boric-acid solution (other ingredients are used, depending on the manufacturer) to extract the starch, which attracts powder-post beetles and termites. The strips are kiln-dried, sanded and laminated together. The lamination is either vertical grain or horizontal grain, in which case the flooring is laminated again for several plies. Typical end products measure around 3 inches wide, with thicknesses from 5/16 to 1/2 and even 3/4 inch. In addition, bamboo floating floors have recently entered the market.
Bamboo's natural color has a rich blonde appearance. Some bamboo strips go through a steam treatment before being kiln-dried. The process darkens the bamboo to a light brown color that is consistent throughout the depth of the product. Manufacturers refer to this process by a variety of proprietary names, such as "caramelized,""ambered" and "carbonated."
Like cork, bamboo is available in both unfinished and prefinished versions, although the latter is more popular. For the most part, it can be installed like any hardwood floor—follow the manufacturer's directions for specific products. Installers caution to take extra time with subfloor preparation, as the product's rigidity is even less forgiving than most wood floors over an uneven subfloor. Just as with cork floors, all subfloor imperfections, such as paint drips, should be scraped off before installation.
Sanding straws
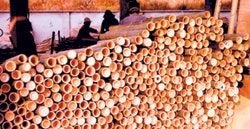
Sanders experienced with bamboo liken it to sanding a bunch of straws. When the tops are sanded off, a "U" shape is left. Because of the product's unique, fibery structure, bamboo should never be sanded across the grain, which would rip up the fibers. In fact, due to its smooth milling, most unfinished bamboo should not be sanded with anything rougher than a 60 or 80 grit for the first cut.
Sanders should be careful about keeping the job site meticulously clean and not wearing traffic patterns into the floor, as unfinished bamboo may hold dirt and reveal traffic patterns once the finish is on.
Opinions vary as to how smoothly the floor should be sanded. Some feel the floor should be sanded fine and burnished to close off bamboo's pores. Others feel this may interfere with good finish adhesion and also risks sanding the bamboo nodes too smoothly (much the same as the knots in knotty pine), causing finish appearance problems. With bamboo's natural, light color, you may encounter some of the same challenges as you would with a maple floor—swirl marks, other sanding marks and finish imperfections are more visible than they would be on a darker floor.
Bamboo manufacturers recommend any quality wood flooring finish and recommend staining, as well. As always, experiment with both the flooring and finish you intend to use before trying it on your customer's floor. Again, be cautious about bamboo suppliers—the market has been flooded in recent years with fly-by-night manufacturers, so choose one you can trust.
Your customers are also looking for someone they can trust— someone who gives them honest information about all their wood flooring options and who knows how to install, sand and finish them the right way. By adding cork and bamboo to your repertoire, you'll have two more options, even for the most ardent environmentalist customers.
Sources for this story included Coley Armstrong, Southern Oak Wood Flooring; Bob Bailey, Artisan Hardwood Floors; Daniel Boone, Goodwin Heart Pine; Ann Knight, Timbergrass; Steve Seabaugh, NWFA; Dan Smith, Smith & Fong; and Ann Wicander, WE Cork.