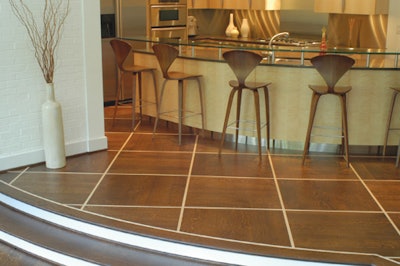
NWFA members voted online before the show and at the Expo at the NWFA Convention in Baltimore in April to pick this year's winners for Wood Floor of the Year, and the winners were announced at the show.
Congratulations to 2006's NWFA Wood Floor of the Year Winners
MODERN MAKEOVER
Best Kitchen/Dining Room | Nicholson Flooring Co. Inc. (Greensboro, N.C.)
Nicholson Flooring Company has come a long way since it was founded in 1948. Eugene Nicholson started the company as a sanding business charging 8 cents per square foot. It wasn't until 1995, when sons Tommy and Larry Nicholson took over their dad's business, that the company ventured into installations. Now, more than 10 years later, this family-owned business has earned its first Wood Floor of the Year Award. So, it's only fitting that the winning floor, which is in Tommy Nicholson's home, remains in the family.
The kitchen and its winning floor is part of an ongoing major remodeling project in Nicholson's home. Nicholson worked with his wife, who did most of the decorating, to come up with a contemporary-styled kitchen mixing a variety of materials. The couple first chose figured English sycamore custom cabinets, and they wanted to design a floor that would complement the light tone of the wood. Nicholson eventually chose maple strips surrounding dark-stained quartersawn white oak panels. The idea for the layout came from Nicholson's wood supplier, who suggested that Nicholson use longer lengths to create a finger-parquet pattern. "I took that one more step and put a border around it," Nicholson says. Using AutoCAD software, Nicholson created the layout, which consisted of 30-inch squares made from six pieces of 5inch-wide, 30-inch-long white oak planks surrounded by maple all laid on a 45. The square panels were preassembled at the shop, then nailed and glued at the job site.
Another key element of the kitchen's design revolves around the curved island. Nicholson built the curved wall, then created templates for the countertop designers. When the countertop was completed, a 16-inch-wide cantilevered glass shelf following the same contour was created and installed on top of the counter. Nicholson then used the same radius from the countertop to create a rounded step leading into the adjoining sunroom. In order to create a seamless transition between rooms, he designed a new step. "The step I inherited between the two rooms was short," Nicholson says. "It was too much not to have a step, but almost too little to have a step, so we made it a full 12 inches wide." The landing tread was made in three sections out of the same 5-inchwide quartersawn white oak. The top tread, which is accented by a maple feature strip, was created using the same radius. Adding both style and functionality to the step, Nicholson cut round grooves on the bottom of both treads and installed rope lights under the treads. Because the lights are part of the tread, they add subtle illumination to the odd-sized step.
After the floor was installed, he turned the project over to his brother, Larry Nicholson, for the finishing touches. The light and dark contrast of the wood required the oak to be taped off while the maple was sealed, and then the maple needed to be protected so that the white oak could be stained.
Tommy Nicholson was thrilled with both his new floor and his first Wood Floor of the Year Award, which shows how far Nicholson Flooring Company has come from its modest beginnings.—C.L.
Suppliers listed in boldface are advertisers in this issue.
Distributor: Horizon Forest Products | Finish: Dura Seal | Nailer: Stanley-Bostitch | Adhesive: W.F. Taylor Co. Inc. | Abrasive: Klingspor | Sander: Galaxy Floor Sanding Machines Ltd. | Buffer, Edger: Clarke American Sanders
ARTISTIC REFLECTION
Best Living Room/Family Room | The Sherwood Flooring (Toronto, Ontario)
Most Wood Floor of the Year winners consider their floors to be works of art, but this floor, created by The Sherwood Flooring owner Predrag "Pedja" Vukmanovik, takes that concept to a new level. The floors in this high-end house in Mississauga, Ontario, literally had to be works of art since the owner dictated that the patterns on the floor be reflected in full-scale paintings on the ceiling. "Every single room in this house—it has about 6,000 square feet of hardwood flooring in it—every room was a challenge. Every room was for a gallery," Vukmanovik says. This custom job required intricate detail, and Vukmanovik was given the proper timeframe with which to complete it. "The owner of that house … told me: 'Pedja, I want my floor to be outstanding. I want my floor to be visible. Take all the time you need to finish this job. There can be no rush,'" Vukmanovik recalls.
Vukmanovik's team was brought onto the custom project by an old friend, Dominic Sarracini, president of Toronto-based Heartwood Architectural Wood Products. The two companies had collaborated on earlier jobs, so when the homeowner asked Sarracini to design the wood floors in his house, Sarracini in turn asked Vukmanovik to install them. "He wanted somebody that really knows how to do these things, because they require a lot of patience," Vukmanovik says. "Before we even laid down the first piece of wood, it took me the full day with two guys just to measure where it was going to go."
For this living room, Sarracini opted for a field of 3-inch-wide ash planks over radiant heat. The perimeter of the floor was assembled off-site into 32 segments of 5/16 -inch-thick flooring to accommodate the intricate inlays. Vukmanovik installed these segments around the ash field. Each section contained hickory, maple, walnut, padauk, zebrawood, nogal and Brazilian cherry. A 2 1/2 -inch wenge border edges the perimeter of the floor, which is surrounded by marble. The only ready-assembled part of the floor was the star medallion in the center—the thousands of other pieces were assembled by hand by Vukmanovik's team.
Vukmanovik had to exercise the utmost caution when installing the myriad pieces. "It's very, very easy to make a mistake, and once that adhesive grabs hold, it's a potential nightmare," Vukmanovik says. Once the pieces were in, he waited two weeks before sanding. The owner had cited concerns about yellowing and, since there was a large amount of ash, Vukmanovik decided to use a water-based finish.
It took Vukmanovik's team more than two months to install the 6,000 square feet of hardwood flooring in the house, but in the end he felt it was another triumph to add to his long list of high-end custom projects. "The owner was very happy, and I was very happy," Vukmanovik says.—M.I.D.
Suppliers listed in boldface are advertisers in this issue.
Designer: Dominic Sarracini | Flooring: Heartwood Architectural Wood Products | Abrasive: 3M | Finish: Basic Coatings LLC | Nailer: Stanley-Bostitch | Adhesive: Bostik Inc. | Sander: Galaxy Floor Sanding Machines Ltd. | Buffer, Edger: Clarke American Sanders | Saws: Dewalt
VICTORIOUS VICTORIAN
Best Entry/Foyer | The Sherwood Flooring (Toronto, Ontario)
Many wood flooring contractors use historical influences as inspiration to create impressive wood floors. So when Dominic Sarracini, president and designer from Toronto-based manufacturer Heartwood Architectural Wood Products, was commissioned to design a custom floor for a high-end project in Mississauga, Ontario, he selected an elaborate lace pattern originating from an English woman's lacework sewn more than 300 years ago. The only person he knew who could properly install this complex pattern was Predrag "Pedja" Vukmanovik, owner of The Sherwood Flooring. Having worked in places such as Serbia, the United Kingdom and Montenegro during its 10 years in business, The Sherwood Flooring was well-equipped for the job. Sarracini designated the complicated Victorian lace design for the house's foyer, which was only one small section of the 6,000 square feet of flooring that Sherwood would eventually install.
Sarracini's intricate lace parquet pattern plays the color and texture of quartersawn white oak against that of Brazilian cherry. Vukmanovik assembled the parquet into 2-by-3-foot tiles that were brought together on-site and glued to the subfloor. "This was very tricky, because each tile is supposed to connect to the next in a pattern, but with two layers of tape, it's difficult to see," Vukmanovik says. The team took its time laying down each tile and settling it into the adhesive. "You just can't cut corners on these types of jobs," Vukmanovik adds. "Each tile had to be connected all nice and tight with not a single hair gap." To contrast the ornate lace pattern in the body of the floor, Vukmanovik bent white oak strips to run as a border around the 300-square-foot entry.
In order to grab the attention of visitors as they walk into the first room of the house, Vukmanovik wanted the Brazilian cherry to appear as red as possible. So he first applied a polyurethane oil-based finish to the floor, followed a month later by a water-based finish. The end result was a custom floor the neighbors aren't likely to have. "It's one of those floors that you don't see every day. Everybody who has ever seen the floor thinks it's carpet or an area rug," Vukmanovik says. "It's the type of floor that some like and some don't, because it's kind of busy, but here it's just a little part of the entry."
As a first-time Wood Floor of the Year Award winner, Vukmanovik couldn't be more pleased. "We're doing all these high-end custom homes in the area, and nobody's seen them except for me, so I thought I'd send a few pictures to the NWFA and see if anything happens, which it did," Vukmanovik says.—M.I.D.
Suppliers listed in boldface are advertisers in this issue.
Designer: Dominic Sarracini | Flooring: Heartwood Architectural Wood Products | Finish: Basic Coatings LLC, Fabulon | Adhesive: Bostik Inc. | Abrasive: 3M | Sander: Galaxy Floor Sanding Machines Ltd. | Buffer, Edger: Clarke American Sanders | Saws: DeWalt
CREATIVE CURVES
Best Bedroom | Diamond Flooring (Elizabethtown, Ky.)
The clients who own this floor are exactly the kind of clients most wood flooring contractors would love to have. He's a retired doctor who appreciates fine things and has a great eye for detail, and she's a noted watercolor artist. While they both contribute ideas for the designs of their wood floors, they also appreciate the artistry of the wood flooring contractor. "They're involved, but not to the point where they're telling you exactly what they want. That makes a big difference for a wood flooring contractor," says Jamie Lupresto, president of Diamond Flooring, who garnered his first Wood Floor of the Year Award for the resulting bedroom floor.
Lupresto had worked with the clients previously, when he and his crew replaced about 36 stair treads and risers in their home and added medallions to the landings. About a year later, the clients called and said they wanted to remove the carpeting from their bedroom and would like ideas for a wood floor design.
Lupresto set about envisoning a floor that would coordinate with the color of the bed and end tables, as well as work with the placement of the furniture and Persian rug that the homeowners wanted at the foot of the bed.
The resulting floor has a Brazilian cherry field. Because of the furniture and Persian rug, a border surrounding the bed was out of the question. Instead, Lupresto drew a design that would subtly accent the bed and end tables using yellowheart and wenge. With minor changes from the client, the scrolling pattern was approved.
Lupresto turned to Custom Hardwod Supply for help creating some of the pieces and templates for the scrollwork, which were essentially large, custom-designed inlays.
Lupresto and his employees Jessie Turner and Jordan Weaver then had two weeks in which to remove the carpeting and complete the entire floor, right down to putting the furniture back in place. The clients typically spend two weeks on vacation, often traveling to Europe. "They leave at 8 a.m., you get there at 9 a.m., and you know that they're coming back in two weeks and have a housekeeper ready to clean it up ... They never even see a saw," Lupresto says.
The schedule is "kind of stressful," Lupresto says, but he's not complaining. In fact, there's plenty of the spacious home left to work on, and Lupresto already has a few ideas in the works for the kitchen and the piano room. When he ran into the clients recently, he simply told them, "Let me know when you're going on vacation again."—K.M.W.
Suppliers listed in boldface are advertisers in this issue.
Distributors: Custom Hardwood Supply Inc., Lanham Hardwood Flooring Co. Inc. | Abrasive: 3M | Adhesive: Bostik Inc. | Filler: Timbermate USA Inc. | Finish: BonaKemi USA | Flooring: DHL Nordisk | Nailers: Powernail Company, Senco | Sander, Edger, Buffer: Clarke American Sanders | Saws: Fein, DeWalt, Festool, Makita
SPANISH FLAIR
Best Library/Office | Johnson Yarema Hardwood Floors (Oakland, Mich.)
Creating an artistic floor for a family of artists is a tough assignment, but John Yarema, owner of Johnson Yarema Hardwood Floors, and his crew completed this job with flying colors. Yarema earned his fifth Wood Floor of the Year Award with this floor, which is in the home of a Spanish physician and his artist wife. The homeowner's brother is also an artist, so the floor design had to fit with his many colorful abstract paintings that decorate the home.
Yarema worked closely with the homeowners to create a floor in the library that would match the bold interior design of the home. "The rest of the house is very eclectic, lots of art everywhere," Yarema says. "We wanted something that was a statement for that room as well." The inspiration for the design came from the Spanish tile floor in the adjacent room, as Yarema incorporated flowers from that tile design into the wood floor. Because the homeowner is an artist, Yarema valued her input on the palette of colors. Yarema went through the list of species she wanted to use on the floor, then he swapped out a few photosensitive species that were susceptible to color change. Twelve species, including purpleheart, padauk, sapele, bloodwood and canarywood, were chosen for the intricate parquet design.
Yarema finalized the design, then his crew began the arduous work of cutting and prepping for the installation. Even though the floor covered only a little more than 200 square feet, the intricate parquet design, which consists of more than 10,000 pieces, required several hundred hours of labor. "We probably spent about three weeks on cutting pieces," Yarema says. Some of the pieces were so small that they would get sucked up by the vacuum on the dust collection system, forcing the crew to cut many extra pieces. "We probably had to cut five times as many," Yarema explains.
Once the prep work was done, Yarema's crew had just a week to complete the installation. The homeowners were leaving town on vacation, and they wanted the room ready for a party when they returned. This meant many late nights and a few 16-hour workdays. Yarema's crew didn't mind the long hours, however. They were excited to work on a job that required such detailed craftsmanship. "Through these guys, you see the way you felt when you first started doing it," Yarema says. "It reinvigorates you."
The hard work paid off. Not only did Yarema win another Wood Floor of the Year Award, but the homeowners were ecstatic when they saw the floor. "They were so gracious," Yarema says. "It was a fun project to work on."—C.L.
Suppliers listed in boldface are advertisers in this issue.
Distributor: Erickson's Flooring & Supply | Flooring: John Yarema Engineered | Nailer: Stanley-Bostitch | Abrasive: Cumi Canada Inc. (Künzle & Tasin) | Finish: Glitsa American | Adhesive: Bostik Inc. | Edger: Clarke American Sanders | Buffer: BonaKemi USA | Sander: Hummel (Palo Duro) | Saw: DeWalt
STUDIO STYLE
Best Commercial/Showroom | Johnson Yarema Hardwood Floors (Oakland, Mich.)
Many elaborate hardwood floor designs have a traditional look. For this floor, John Yarema, owner of Johnson Yarema Hardwood Floors, wanted to show that hardwood flooring design can have a hip, modern twist. Originally designed for the recording studio of rock star Kid Rock, the design plays off an art deco French fabric. The designers were covering the studio walls in denim, and Yarema thought the art deco design would be perfect for the denim-clad walls. In the end, a simpler design was chosen because of the tight timeframe for the studio, but Yarema still wanted to use the design. So, he decided to install it in a 288-square-foot office in his showroom as part of a multiroom concept theme. "That was one of my favorites in the sense that I've been wanting to do it for well over a year and a half," Yarema says.
Yarema had created the initial design for the studio, but it needed to be customized for the showroom. "Everything we do, we custom-size it to the room so it works in the scale of the room," Yarema explains. That ensures there are full patterns running to each wall and that no design element is cut off. After the design was scaled in AutoCAD, Yarema chose a mix of wenge, quartersawn white oak, quartered maple and quartersawn walnut to add depth and create a three-dimensional effect. As with all of Yarema's designs, he chose the species by assigning a color value to each species. This process ensures that the combination of species on the floor will have the desired tone and contrast when next to each other. Once the design was complete, the pieces were cut and laid to the floor.
The design, engineering and cutting process took about three weeks to complete, but Yarema's crew installed the glue-down floor in just over four hours. While the installation may have been speedy, Yarema felt that quality wasn't compromised. "It's probably one of the finest installs I've ever seen," he says. "There's no fill in it, and you couldn't put a business card anywhere in the floor." With all of the small pieces coming to a point in the floor, there was no room for error.
After the installation was complete, Yarema decided to stain the walnut pieces in the floor to add a bit more contrast with the white oak. The floor was then finished with four coats of conversion varnish.
Although the floor didn't end up in Kid Rock's studio as originally intended, its current setting seems to have worked out better— Yarema already has two requests for the floor design as a result of it being displayed in his showroom.—C.L.
Suppliers listed in boldface are advertisers in this issue.
Distributor: Schafer Hardwood Flooring Co. | Flooring: John Yarema Engineered | Nailer: Stanley-Bostitch | Abrasive: Cumi Canada Inc. (Künzle & Tasin) | Finish: Glitsa American | Adhesive: Bostik Inc. | Edger: Clarke American Sanders | Buffer: BonaKemi USA | Sander: Hummel (Palo Duro) | Saw: DeWalt
VERSAILLES IN THE SKY
Best Restoration | Legendary Floors Terre (Haute, Ind.)
Opulent" is the best word to describe this palatial home, perched on the 68 t h floor of a prestigious address in downtown Chicago with a view of Lake Michigan. The designer was from France, and there were four French craftsmen on-site for four months gilding real gold throughout the home. It was so lavish that the building staff nicknamed the apartment "Versailles in the Sky." Not just any wood floors would do, so a detailed laser-cut wood floor was ordered from Italy, and Italian workers installed it. Unfortunately, when they flew back to Italy, they left the windows open to help the finish dry. That weekend, when the butler stopped in, he found 2 inches of water standing on the imported showpiece.
That's when Mark Scheller, who handled the restoration for Legendary Floors, was called in. He found that the floor, which had been installed as large panels, was no longer flat, and the seams between the panels, which hadn't met perfectly to start with, were now open. Pieces within the intricate pattern had cracked and needed to be replaced.
Scheller's first step was finding exactly the right wood to use as replacement parts for the floor, which included elements of white oak, walnut, European pear, mahogany, holly, wenge, padauk and bloodwood. "I spent at least two days going all over Chicago looking for just the right wood, the right grain pattern and the right density of growth rings," Scheller recalls.
Scheller discovered that the original installers had used only tiny trim nails to secure the panels to the subfloor. Where the seams had opened between the panels, Scheller injected a two-part urethane adhesive that remains flexible and elastic after curing. Where ever possible, he also screwed the panels down. Where the seam was unacceptable, he replaced the portions of the inlay work that met at the seam with new wood that matched the original pieces.
Around the four panels that make up the large center circle, the seam needed more drastic measures, so Scheller routed a circle around the perimeter, injected the urethane, rerouted the circle to get a flat surface on top of the urethane, and then carefully inserted two 1/8 -inch strips of wenge, creating what appears to be one band of wenge original to the floor.
Throughout the rest of the floor, Scheller salvaged what he could, and, where necessary, recreated damaged pieces. In other areas, he used slivers to disguise unsightly cracks. At doorways where butt joints of the floor met up unevenly against the floors in adjoining rooms, he inserted a new maple feature strip that blends in seamlessly with the original floor.
All told, Scheller worked on the repairs full time for five weeks. The floor was then resanded and refinished with wax finish. With its precise seams and attention to detail, the restored floor ended up looking even better than the original.—K.M.W.
Suppliers listed in boldface are advertisers in this issue.
Designer: Juan Pablo Molyneaux | Restoration: Scheller Hardwood Floors | Hand-Scraping & Finishing: Birger Juell Ltd. | Adhesive: Bostik Inc., Lord Corporation | Saws: Fein, Festool, Bosch | Router: Porter-Cable
PATIENCE OF A SAINT
Best Factory-Finished Floor | Scheller Hardwood Flooring (Lemoyne, Pa.)
A good part of this installation was uncomplicated—2,200 square feet of 3/4 -inch-thick, 5-inch-wide, hand-scraped and factory-finished Brazilian cherry laid straight in a brand-new church. The tricky part came at the edge of the raised area supporting the altar, which involved 60 lineal feet of a radius bullnose. A radius bullnose alone wouldn't be too much of a challenge for an experienced installer, but this one had an added complication. "The nosings are all curved, but they are not an arc," says Mark Scheller, whose company collected its second Wood Floor of the Year Award for this project. "Whoever poured the concrete just winged it on the curve, and then they shimmed them out a little bit to get them closer." In addition to the steps being irregular, the unfinished Brazilian cherry nosings had been made with a rough template and a band saw, so they, too, were not precise. Scheller's challenge involved figuring out a way for these irregular steps to meet the field flawlessly.
To accomplish that, he started by making a template for each individual piece of nosing. He screwed a piece of plywood to the bottom of the nosing, and using a 1/2 -inch router bit, he cut halfway through the piece of plywood as he followed the profile on the back of the nosing, which would be the part meeting the field. He then took the nosing off the plywood and, using a bearing 1/2 inch bigger than the router bit, he cut through the rest of the plywood, ending up with a template that precisely fit the irregular nosing. Reference marks on the nosing marked the exact fit for realignment. Once a template was made for each piece of nosing, they were cut to length and fit to the existing floor, and the prefinished floor was routed away.
With the nosings fit lengthwise and to the profile of the floor, Scheller then went about fastening them without using any nails. "There's no way to clamp a nosing, so I used self-clamping biscuits," he explains. "They're plastic and they're barbed— they're hard to find and they aren't cheap—but they're really the only thing that would work in this application." Together with urethane adhesive, the nosings were firmly secured.
In all, the nosing work took about four to five weeks—more than would try the patience of many wood flooring contractors, but not Scheller, who thrives on precise, time-consuming projects. "It was a challenge; I like challenges," he says.—K.M.W.
Suppliers listed in boldface are advertisers in this issue.
Architect: W2A Design Group | Flooring: Brazilian Direct Ltd. | Nailer: Primatech | Adhesive: Sika | Saws: Festo, Fein | Router: Porter-Cable | Biscuit-Jointer: Lamello
SEAWORTHY SPIRAL
Best Limited Species | New Detroit Design Studio (Ray, Mich.)
The "chambered nautilus" is a crustacean inhabiting the western Pacific Ocean that, as it grows, continually builds larger chambers in its shell, eventually forming a spiral. Gabrielle Meaney of New Detroit Designs used that spiral pattern as inspiration for creating a spiral staircase in her studio. "Every time I walk up that staircase I am reminded of a nautilus pattern," Meaney says. The staircase also serves as a physical metaphor for her artistic life and her career in the hardwood flooring industry.
Playing on the spiral shell theme, Meaney had two goals. She wanted to construct a floor out of several pieces, yet have it look whole when viewed from above. Meaney also wanted to show how striking a floor can be when only three species are used, as opposed to the 42 or more species she incorporated into previous floors.
Meaney started her project by designing the nautilus pattern in AutoCAD with padauk, purpleheart and curly maple. "I think when you put the purple and orange [of padauk] together, and then they're both beside the very refined, iridescent curly maple, its extraordinary," Meaney says.
Working with a laser cutter and her designs, Meaney then assembled each piece of engineered flooring into treads that easily interlocked with the staircase frame. "So the stairs are inherently stable, and I didn't have to use gobs of glue," Meaney says, noting that she can disassemble the stairs if needed. She then bordered the higher treads with an old Venetian mortar recipe of ground-down river rock interspersed with droplets of glass to contrast the wood and create the illusion of a shimmering ocean floor. Stone and glass were among the first materials Meaney had used as a student starting her art career in Ireland, so she feels as though she has come full circle by combining these materials with her current pursuit of art in wood flooring. Meaney completed the installation with the nautilus holding a 24carat-gold leaf sign that says "Limited Species," which was significant to her, not only to demonstrate to clients the beauty of working with only three types of wood, but also because she says the nautilus family itself contains very few species.
Just as she had come full circle in her art career, it was important to Meaney to complete her wood flooring education by sanding and finishing the stairs herself instead of relying on the sand-and-finish companies she uses for other projects. Using palm sanders, Meaney smoothed each tread and coated them with a satin oil-based finish.
"I have a passion for wood, that's all I can say," Meaney says. She hopes this passion stands as an example to other designers of why flooring can't be ignored, and to constantly open minds to what flooring can be. "I think what's exciting is that not only is this a floor, it's a piece of art—and you can walk on it. You start at the bottom and you get to the top— and that's dynamic," Meaney says.—M.I.D.
Suppliers listed in boldface are advertisers in this issue.
Distributor: Rare Earth Hardwoods | Finish: Harvester Inc. | Adhesive: Bostik Inc. | Abrasive: 3M | Sander, Saws: DeWalt | Buffer: Ceno Group
SYLVAN RETREAT
Best Reclaimed | Birger Juell Ltd. (Chicago)
There aren't too many wood flooring jobs that would be considered unusual for Birger Juell Ltd. The ultra-high-end wood flooring company has done jobs for some of the world's wealthiest clients in the U.S. and abroad. But this Wood Floor of the Year winner was truly a one-of-a-kind project.
The genesis for the floor was an idea from the company's namesake, Birger Juell himself. While on a trip to Mexico, he had seen workers assembling a stone floor using everything from large stones to tiny pebbles, and he thought it would be interesting to duplicate the design in wood.
This project proved to be the perfect opportunity to realize that vision. The company had previously installed floors throughout the customer's opulent Chicago home, and now the client was renovating his turn-of-the-century log home in upscale Lake Geneva, Wis. When he saw a small sample of the floor created in wood, the customer immediately loved it, says Brian Quinn, salesman for Birger Juell Ltd.
Quinn ended up spending about two weeks on his hands and knees in the 6-by-10-foot bathroom working on the floor. He started with the large presanded and prefinished oak rounds. To fill in the spaces between the rounds, he walked through the wooded property, gathering twigs and branches. "There's oak, birch, maple and all sorts of stuff that I don't even know what it is, it just looked right," Quinn says. "I really wanted to bring in elements from his property to make it that much more intimate." Quinn cut the pieces on-site and let them air-dry for a week.
With his material ready and cut to the 3/4 -inch thickness of the floor, he carefully dipped each one into a pan of adhesive and placed each twig. When he thought the floor was ready, he filled it in with the soft grout—a combination of sawdust and oils—that the company typically uses to fill in its end-grain floors. When he and the project manager stepped back and looked at the final result, they both realized that the floor needed more of the smallest pieces, so Quinn meticulously removed all of the soft grout and installed more of the smallest material. Rough spots on the little pieces were hand-sanded, as using any kind of sanding machine would have knocked them out. Once complete, the floor was again filled in with the grout, and the floor was coated with the company's oil-and-wax finish system.
"It was a very rewarding job at the very end of it, but a very painstaking process," Quinn says. The time-consuming job was worth it, as the owner loved the floor, and Birger Juell was thrilled to win yet another Wood Floor of the Year Award.—K.M.W.
Suppliers listed in boldface are advertisers in this issue.
Flooring: Birger Juell Ltd. | Finish: Dura Seal | Adhesive: Bostik Inc.
Take a look at past Wood Floor of the Year winners:
Waikiki Winners: 2005 Floor of the Year Awards
Show Stoppers: 2004 NWFA Wood Floor of the Year Winners
In the Spotlight: 2003 Floor of the Year Winners
Best in Show: Floor of the Year Awards 2002
Sweet Victory: 2001 Floor of the Year Winners