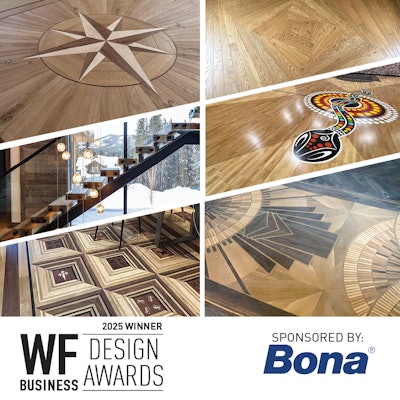
From breathtaking residential stairs that blend rustic charm with modern design to an inspiring showroom that tells a family's story through its intricate custom inlays, each winner of the 2025 WFB Design Awards exhibits dedication and passion for wood flooring craftsmanship. These award-winning projects showcase the achievements of wood flooring professionals and their unique visions that transform flooring into works of art.
We're honored to highlight their efforts with awards for Best Residential, Best Commercial, Best Stairs, Best Gym, Readers' Choice and Next Gen (for companies owned by someone 35 or younger). The winners were selected by an independent panel of wood flooring experts and, for Readers' Choice, via an online survey. This year's sponsor, Bona US, will provide each of the winners with prizes, and one winner will receive a $500 gift card.
Thank you to everyone who submitted to the 2025 Design Awards and to those who strive to elevate the industry with their commitment to the craft. We want to see your future projects, as well. You can enter the 2026 Design Awards here. The contest is open to all wood flooring professionals across the U.S. and around the world. To see this year's winners, scroll down.
Readers' Choice
Courtesy of 50 Grit Flooring
50 Grit Flooring | Cincinnati, Ohio
Josh Hansman was inspired to draw this design giving the illusion of movement to a wood floor … and then the idea sat, undisturbed, for a decade. "I've been holding onto it because you have to have a special room," Hansman says. "You can't just put that in somebody's house unless they live in a carnival house or something like that."
When it was time to install a wood floor in the 50 Grit Flooring conference room at the company's design center, Hansman realized he had the perfect space for his vision. He even had the material, which was 10-inchwide prefinished red oak plank left over from a previous job.
With that, Hansman began puzzling out how to actually create what he says is a "Fibonacci-inspired" floor. The Fibonacci sequence is used to create golden spirals, which are found throughout nature.
"I knew I had to start from the middle and work out. That's all I knew. So you just start cutting, and then you figure it out," Hansman says. "I'm kinda drawn to puzzles, but puzzles in real life, like, when you have a difficult floor and you run into something that is really tough. And then I like trying to figure out a solution and … breaking it down to the steps."
Courtesy of 50 Grit Flooring
For this puzzle, Hansman measured the exact dimensions of the conference room, then began building and dry-laying the floor in his warehouse. First he ripped the 10-inch-wide planks into two pieces that each measured 2 inches at one end and 8 at the other. Then, starting with a middle square, he built the floor piece by piece. One end of the board had the original square cut, and the other was an angled cut at the right length he would mark and cut as he went. "As unique as it is, it's still pretty simple," Hansman says.
Once it was dry-fit, it had to taken apart and labeled with a number for the row and letters for the sides. Then each piece was routered so it would accept a spline.
"Probably the hardest part of the project was having to move it into the conference room. The very center piece is a square, but it couldn't be laid square in the room. It had to be rotated," Hansman explains. Because the floor was being full-trowel-glued to the slab, there would be no room for adjustment once it was installed, so, "we're trusting that the measurements are right and that we will end up hitting the corners." The last rows fell perfectly with a ¼-inch gap at the walls. Hansman is happy with the final result—to some degree. He wonders if he could have "made it spin more" by using wider boards for a more drastic taper, but then he considers that might be too much. "With my creative side, I wanna overdo everything and go big and make everything super crazy," he says. "But at the same time, you can't. You have to keep everything kinda subtle."
Most satisfying for him is creating something unique. "It's one of a kind, right? I've never seen another floor like that. So, I can claim this one as my floor."—K.M.W.
SUPPLIERS (advertisers appear in bold): Adhesive: Bona | Moisture Meter: Delmhorst | Router: Makita | Saw: Festool | Wood Flooring: Carlisle Wide Plank
See how the cuts were made for this floor:
See a time-lapse video of assembling this floor:

Best Residential
Courtesy of Ourada Designs
Ourada Designs | Seven Mile Falls, Wash.
"I just want to make beautiful things, and they don't have to be live-edge," says Tom Ourada at Ourada Designs. "I felt like I pigeonholed myself by doing the live-edge thing; the reason why I've done that is that's the material I have at hand," he says. Although his winning entry this year is a marked departure from his signature live-edge style, the large art deco inlay that is the centerpiece of this year's winning floor shares one important factor in common with his previous work: It was all painstakingly cut, piece by piece, in his shop.
Ourada was brought onto the job to install a herringbone floor, but when he saw the art deco style of the home, it set his artist's mind in motion. He researched art deco design online and began to sketch—a process that happens organically for him. "Any time I get motivated, I'll just go sketching some stuff out, it could be in my van, in my basement, in my bed … all different places," he says.
His final vision uses art deco to allude to the nearby Seattle skyline. Two subtle offset starbursts in the background suggest the fireworks he would watch growing up in Seattle as a child.With his sketch approved by the client, he began creating the inlay in his shop. "I took pretty accurate measurements of the space there, but until you get it on the floor, you just don't know exactly how it's going to fit, so I made it all a little bit bigger than should be," he says. The final design has five half spheres, each a different dimension. In his shop, he began each one by bending the outer ring, then filling in each row with the rectangles and wedges. He adjusted the wedges very slightly if he saw his pattern was beginning to be off. Piece by piece, row by row, he built each radius until it created a half sphere … "So that was fun!" Ourada says—sincerely. "What I love doing is figuring out new stuff: How am I going to make this work?"
Each half sphere transitions from maple rectangles on the outer row to darker colors, with a combination of alder and maple, then acacia and walnut. The wedges are white oak.
On site, he laid out the half spheres and cut them into place, adjusting for factors like the door not being exactly centered to the stairs, then filled in the rest of the inlay. Then he could complete his walnut herringbone floor, making sure the herringbone started exactly equally on each side of the inlay: "You can see the triangles on the right and the left are exactly the same," he notes.
Facing a time crunch, Ourada brought in friend and fellow wood floor pro Keith Long to help complete the herringbone installation and sanding. Then the floor was coated with a penetrating oil. In total, the 800-square-foot took a total of two weeks in the shop and three weeks on site.
Ourada was excited to work on a project outside of his "norm" that fulfills his need to create art. "Josh Hansman asked me, 'Why are the points of the stars not in the same spot—why are they off?'," he says. "It was interesting that somebody noticed that it isn't symmetrical. To me, that's what art is about: Getting people seeing things and noticing things."—K.M.W.
See this video tour of the completed floor:

Gallery by Suelos de Madera | Valladolid, Spain
SUPPLIERS (advertisers appear in bold): Abrasives: 3M | Adhesive: Wakol | Buffer: American Sanders Epoch | Edger: American Sanders Super 7 | Filler: DuraSeal | Finish: Daly's Wood Finishing Products FloorFin | Moisture Barrier: Wakol PU280 | Moisture Meter: Lignomat | Nailer: Bostitch | Sander (big machine): Hummel | Sander (palm): Festool | Saws: Festool, Makita
Best Commercial
Courtesy of Gallery by Suelos de Madera
Emilio Manzano, owner of Valladolid, Spain-based Gallery by Suelos deMadera, says when customers come into his showroom they are filled with "amazement and admiration" upon seeing the showroom's custom floor. "They are interested in knowing how it has been built, what meaning the figures have and what is in each piece of parquet," Manzano says. The showroom floor is a parquet of emblems dedicated to Manzano's family and their history. It includes tiles with the initials of Manzano, his wife and their children; silhouettes of the family's mastiff, French bulldog and cat; symbols of the Camino de Santiago and the autonomous community of Castile y LeĂłn where their family lives; and leaves of the trees from the species used in the floor.
In 2020, the Gallery by Suelos de Madera showroom flooded, requiring the floors be completely replaced. Manzano turned the unfortunate situation into an opportunity to create something unique for the floor. Earlier that year, Manzano had worked on a similar parquet floor at the Domotex trade fair for Workcamp Parquet. "We built this pattern and I liked it so much that I decided to reproduce it as soon as possible," he says. With his showroom suddenly needing a new floor, he had the chance to recreate it.
Courtesy of Gallery by Suelos de Madera
The floor was created using fully recycled materials using scraps from his previous flooring projects. The species included maple, walnut, merbau, wenge, badi, cherry and Douglas fir. So many species were used because Manzano wanted to "show the public our professional capacity, skills and the beauty of wooden floors," he says. Every piece was hand-cut from blades made of metal from old band saws and, once installed, the floor was hand-scraped by Manzano and his son Sergio. Together, his family built the floor over 12 months, using all their free time and days off.
The recreated showroom has a completely different look from the old one, Manzano says. The old showroom floor was made of small Douglas fir pieces and the floor wrapped up onto the wall, giving the room an "industrial look." But this showroom represents a labor of love: love for the craftsmanship of wood flooring and love for his family business.—S.V.
Courtesy of Gallery by Suelos de Madera
SUPPLIERS (advertisers appear in bold): Adhesive: Pallmann P6 | Buffer: Bona FlexiSand 1.9 | Dust containment: Festool CT 48 E AC | Finish: Pallmann Magic Oil 2K Original | Moisture barrier: Pallmann P104 | Moisture meter: Gann Hydromette RTU 600 | Multi-disc sander: Pallmann Spider
Best Stairs
Courtesy of Furniture Grade Floors
Furniture Grade Floors | Silverthorne, Colo.
Silverthorne, Colo.-based FurnitureGrade Floors LLC's business strategy is to always execute the "finest level of craftsmanship" with "high-quality, detailoriented work." That's a promise owner Everette Simmons believes he successfully accomplished with these winning stairs.
Furniture Grade Floor wasn't originally chosen to build the stairs in this Frisco, Colo., home. The company was initially hired to install the floors of this new build, but when Simmons went to take measurements, he saw the potential to create something "showstopping." The homeowners intended to install a floating staircase made of Douglas fir, but Simmons thought a more rustic look, matching the reclaimed oak floors of the home, would be a better fit. "I sort of sold them on saying, 'Just trust us with this process, and we will give you the nicest staircase that you've ever seen,'" Simmons says. His pitch was a waterfall grainmatched floating staircase constructed with the same materials as the floors, creating one cohesive look.
The floors and stairs consisted of 50% white oak with a worn appearance and 50% reclaimed mix of red and white oak. Every piece used was hand-selected to match the length, texture and color Simmons desired for the floor. The two selections were different colors, so the installers had to alternate between the two to get an overall blended look. Simmons wanted the waterfall fold to continue down the tread and wrap back around to the top since every side of the stair would be visible, but getting the waterfall fold on the treads on was "extremely difficult," as the reclaimed wood tended to crack and fall apart when cut. To ensure they had long enough pieces, Simmons says a lot of glue and tape was used to keep the pieces together and the miters tight.
Courtesy of Furniture Grade Floors
Once the treads were built, each was hand-sanded and finished to create a custom rustic look. For the finish, they first applied a custom stain and two coats of waterborne finish. Next they troweled on black knot filler, then wiped it off with water and hand-sanded it again before adding another layer of finish. "That made the stairs look really rustic and rough, but when you touch it, it's baby-smooth," Simmons says. The steps were then mounted to the glass and steel railings by drilling bolts into the sides of each tread. Track lighting was installed underneath each step to create a ½-inch shadow reveal to the walls.
Simmons says he knew they had created something special as they were completing the stairs and every other tradesman working on the house stopped to look and was blown away by the craftsmanship. He says, "We do floors and they get walked on and overlooked, so to have people appreciate the insane amount of work that goes into it is really special."—S.V.
Courtesy of Furniture Grade Floors
SUPPLIERS (advertisers appear in bold): Abrasive: Norton | Adhesive, Moisture barrier, Underlayment: Wakol | Borders: Birch Creek Millwork | Buffer, Big machine: Lägler | Edger: American Sanders | Filler: Berger-Seidle | Moisture meter: Delmhorst | Nailer: Bostitch | Router: Bosch | Sander (palm): Festool | Saws: Festool
Best Gym
Courtesy of Creative Flooring Solutions
Creative Flooring Solutions | Grovedale, Australia
Although Creative Flooring Solutions is known for its high-end residential work, this isn't the type of residential wood floor they are known for. The company is increasingly focused on sports flooring, however, and this project combines both of those markets, as the portable court is in the basement of a large home overlooking the Indian Ocean in Western Australia.
"The need for basketball courts is huge in Australia, with everyone recognizing we are many hundreds of courts short of what is required," says Chris Stringer, owner at Creative. He says they are doing "a heap of portable courts" due to the ability to rent an old factory or warehouse and install portable courts to create a basketball facility, and in residential applications, customers can take the floor with them if they move.
"It used to be when a family built a home for the family the focus was on a large lawn for the kids to play football and other sports, but today we are seeing a large change with many families looking at having their own basketball court at home," Stringer says.
Courtesy of Creative Flooring Solutions
This client contacted CFS after seeing their courts used by professional teams. That began a two-year process that started with the client considering a replica of the Chicago Bulls court but then seeing another court online and saying he wanted something like that, with the stained "X" background, but with some personal touches. "From there the design evolved," Stringer says.
Gold shamrocks were added to represent the homeowner's family's Irish heritage. For the center, the homeowner decided on a Wagyl, which is a rainbow serpent in local aboriginal mythology that symbolizes creation and protection. "For the Noongar people, the Wagyl represents their deep connection to the land and their duty as custodians, emphasizing the need to respect and preserve the environment it created," Stringer explains.
The homeowner worked with a designer to create the exact representation of the Wagyl, then turned it over to the CFS team to render it precisely. "The homeowner was very particular about every detail on this court. We have hundreds of emails between each other over two years of designing the court and producing the drawings to producing scale models of the entire floor," Stringer says, explaining that there were many changes for the font, line colors, the brown stain that forms the X and more.
Two years later, with the design finalized, the CFS team was able to make the court come to life using a Danish-designed portable court system with hevea panels measuring 2180 mm (7 foot 113/16 inch) by 550 mm (1 foot 921/32 inches) by 44 mm thick (1¾ inch). The court is a Level 1 Fédération Internationale de Basketball-approved court—the highest level—with the addition of gold NBA three-point lines. "It represents the homeowner's commitment to making a great space for his children and their friends to hang out and shoot some hoops," Stringer says. It also represents the Creative team's commitment to tenacity, making sure this cherished court's installation was a definite slam-dunk.—K.M.W.
See a video tour of the floor during installation:
Courtesy of Creative Flooring Solutions
SUPPLIERS: Project manager: David Stringer | Installation: Creative Flooring Solutions, Planet Timbers | Moisture meter: Tramex | Router: Festool | Saws: Festool | Wood flooring: KTL Floor
Next Generation
Courtesy of MacDonough LLC
MacDonough LLC | Attica, Mich.
Austin MacDonough, owner of Attica, Mich.-based MacDonough LLC, knew exactly what design he wanted for this room when homeowners showed him the third story of an octagonal tower on their property in Metamora, Mich. He was brought onto this project with little instruction: just that the homeowners wanted something "special and weird." So, when he saw the top floor of the tower surrounded by windows, a compass seemed like the perfect fit. "We walked in the room and they said, 'What can you come up with?' And I said, 'I think this room needs a compass,'" MacDonough says.
The compass is located in the center of the 450-square-foot room, with 96 white oak pieshaped boards radiating from it. Circling the edge of the room and adjacent staircase is a border of white oak and American walnut.
Centering the compass and aligning the radiating planks to the walls presented a design challenge, as the walls weren't the same length and the windows weren't centered on each wall. In order to give the illusion that everything was the same size and centered, MacDonough cut the pie pieces into 16 shapes ranging from 8½ to 9¼ inches in width and made sure the planks aligned with the corners of each wall.
Courtesy of MacDonough LLC
Once all the pie-shaped planks were glued and nailed down, MacDonough free-hand cut and routed in the pieces of the compass. The compass includes white oak, American walnut and curly maple. Because he didn't want the compass to look like it had been "dropped into the floor," he designed it to have points sticking out of the main circle and the cardinal directions completely separate. The letters were cut on a band saw and routed in the floor. After every piece was installed, the floor was hand-scraped and coated with waterborne finish. Working with his two employees, the room took six weeks to complete.
Two years into owning his business, the 26-year-old is proud of his employees, Pete Kreiner and Austin Miller, who are able to create unique floors like this. MacDonough says taking care of his team by paying them well and having good communication is the reason the team is so successful and hardworking. When he started his business at 24 years old, MacDonough says everyone told him it wasn't the right time and he should wait until he's older, but MacDonough's advice other young pros is to branch out when you feel ready. "If you have drive and determination, you'll get somewhere," he says, and he's certainly proving that point.—S.V.
Courtesy of MacDonough LLC
SUPPLIERS (advertisers appear in bold): Abrasive: Red Devil Scraper | Adhesive: Bona | Buffer: American Sanders | Finish: Ciranova | Moisture barrier: Wakol PU280 | Nailer: Bostitch | Router: DeWalt | Sander (palm): Festool | Saws: Festool, DeWalt