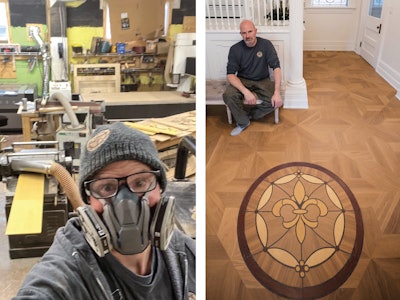
I grew up doing some woodworking with my dad and brothers, and we were always renovating old houses for rental properties, too. I don’t remember how I felt about it, but there was always an appreciation for wood around us growing up. Looking back on it now, I know it was the best thing we could have been doing—and I had no idea where it would eventually take my life and my career.
When I headed to university, my roommates worked for a guy refinishing bowling alleys all summer. I joined them traveling across Ontario for four months—and realized sanding, repairing and finishing was so gratifying.
I went to the library and signed out the best book I could find on the subject, written by Don Bollinger in 1990. I learned about NOFMA, so I went to their school and was amazed by the massive collection of wood floor instructors and students and the panels and equipment—it was pretty magical. The highlight was meeting Don Bollinger himself—I couldn’t believe it!
My bank was giving $15,000 loans to small businesses, and it was just enough to buy a new set of dustless Bona sanding equipment. I started hustling, and eventually my two brothers joined and we opened a showroom. We went to more classes and ran crews until 2008, when we decided to shut down the showroom and part ways amicably.
I decided to focus strictly on site-finished wood floors and push myself toward higher end work. I found the Decorative Flooring school in 2009 with Jim Garth. I was captivated by what he was doing with his laser-cut process and his vacuum table presses. The laser-cut thing was way over my head, but his jigs and sleds really caught my attention—we used them to create square star medallions and borders. I came back full of new ideas and ambitions.
I attended more classes, and in 2017 I finally met Lenny Hall. Lenny had a big impact on me with his meticulous calculations, teaching me about using calipers and bringing me into his “reading to 1,000th of an inch club.” His techniques for setting up a fence on a table saw using calipers and using screws as stop-blocks for fine adjustments on miter saws was truly a game-changer. Lenny also became someone I could reach out to—he truly is a gift to our industry.
In 2016 I had saved enough money to buy a building for a showroom/shop. I bought more equipment to do high-precision woodworking. Over the years I had been inspired by the award-winning floors from craftsmen like Gene Klotz, Birger Juell, John Yarema and Chuck Crispin, and I started entering my floors in the industry contests. They were herringbone or basketweaves with borders, etc., so nothing too crazy, but I was excited to even have an entry.
Then I had a chance to do some intricate walnut patterned flooring in a new build; it included two matching 8-foot-wide medallions with 12-inch book-matched walnut inlays. This gave me my first award—a WFB Design Award. The following year I did a crazy restoration of a century-old parquetry floor lost in a fire, and there was a big profile of it in this magazine. A couple years later we fabricated a pattern in marble and prefinished wood for a big designer in Ontario, and it won another WFB Design Award. The same year I created a 16-foot-wide live-edge walnut medallion for my showroom and won my first NWFA Wood Floor of the Year.
Then one day I was reading WFB and saw a Dan Antes article with his massive intricate medallions. I reached out to him, and before you know it we were on the phone discussing his CNC decorative work and my ambitions for decorative wood flooring. So now I’ve met yet another generous craftsman in our industry.
Honestly, for most of my career the laser and CNC-cut floors were not of any real interest to me (in fact, I complained about hand-cut and CNC-cut floors being allowed in the same categories of competitions). But Dan’s work looked so intricate yet still so artistic that it really drew me into wanting to learn more.
Soon after, I learned about the Shaper Origin handheld CNC router, and it was a way to get my feet wet in CAD/CAM. I started figuring out how to use this magical device. They made it easy to upload existing files and create simple shapes; it’s when you want to create something original that you have to learn some design programming. The programming came fairly easy to me, but I found the tool a bit too much work: I created an intricate 140-piece compass rose medallion that took over 30 hours to cut!
This is when I started to search for a gantry CNC bed—a gantry is a milling machine where the cutting head moves along a horizontal “bridge” above the work piece. I found a lightly used imported 4-by-8-foot machine with a strong 7-hp spindle. The machine sat for close to a year before I figured out its CAM program, but eventually I got the beast running. I went back to cut my 140-piece medallion on this machine—in an 8-hour day with no hands!
I’m still learning—and I find the best work comes from collaborating with designers and homeowners. This design came from a stained-glass window in the home.
Today, our operation with my crew of four is all site-finished work, and every four to five jobs we get to have fun with patterns or inlays. I have the best crew I’ve ever had, and I like to play in the shop, making our own designs for jobs and fabricating patterns and inlays for other contractors here in Canada. I’ve also been cutting trees down and playing with end-grain and live-edge flooring and furniture.
I feel like I finally have all the tools and skills necessary to be the craftsman I’ve always wanted to be. I’ve learned from the best in the world, and I will continue to learn and grow … but what’s left to know? What separates me from the top guys today? It’s creativity and the customers, of course. I have been studying art, creativity and design, and I do find the best designs come from collaborating with other artists, whether they are designers or homeowners. When someone gives me ideas and I can use my experience and knowledge, we always come up with something unique, that is what’s really exciting and keeps me engaged.
At 54, I feel I have a lot still left to give this world. As I continue running my small business, I also welcome the opportunities of fabricating floors and collaborating with other artists and craftsmen and women across Canada—and maybe further—to create amazing things in wood for as long as I can. Some might think it sounds like I’ve had a great career, but most days I feel like I’m just getting started.