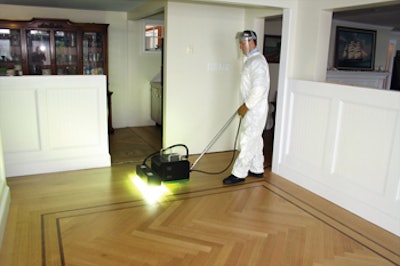
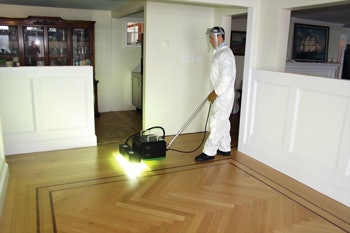
Traditionally, customers who wanted job-site finished wood flooring always had to compromise in a couple key areas. They've had to wait to get back on the floor while the finish dried enough to move the furniture and rugs back on the floor, and they've also had to sacrifice some durability. That isn't necessarily the case anymore, though: UV finishes that can be cured on the job site are now available, and using them has created a real competitive advantage for my wood flooring contracting business.
How it Works
What is essential for UV-curable finishes is UVa and UVb light-the same light spectrum that cures most factory-finished flooring. These portable systems (coupled with water-based UV finish) essentially allow us to bring the prefinished finish technology to the job site.
The equipment is quite simple: It consists of a power supply and UV lights. Once the finish is dry to the touch, you roll the machine over the floor to instantly cure the finish.
There are about five manufacturers of the lights and two distinctly different types of lights. One is a "hot restrike" setup, which is achieved through the use of continuous wave xenon lights; it does not require warm-up and cool-down cycles before and after turning the light on and off. The other is a high-pressure mercury light, which does require warm-up and cool-down cycles (about 30-45 seconds). Both systems are proven to work and are available in 110- and 220-volt configurations, with lamp heads from 12 to 26 inches, in both automatically and manually driven configurations. Handheld lamps are also used to "cut in" the hard-to-reach areas and come in handy when getting started or when site-curing steps. When using any of the UV machines, it is extremely important to protect your eyes and your skin from exposure to the light.
Job-Site UV Finish
The finish, just like the equipment, is also quite simple. You apply it just as you would any other water-based finish, and just as with all non-UV water-based finishes, you must think in terms of "dried" and "cured."
The biggest misconceptions about UV finishes are that they do not dry on their own and that they are not compatible with many stains, sealers, water-based finishes and prefinished products. Neither is true. They do dry on their own without UV light, enabling the flooring contractor to walk on the floor, if needed, to plug in the UV lights if there is no power access beyond the wood floor. And, like all other commercial water-based finishes, there is a chemical process during the curing stage that, in effect, plasticizes the coating with a catalyst or hardener serving as the second component. In non-UV coatings, we use organic compounds such as isocyanate and aziridine to, in part, speed the curing process and add to the coating's durability. With UV finishes, the catalysts are photo initiators and oligomers that break down the low-density molecules upon exposure to the UV light, causing polymerization. The result is an impermeable, chemically resistant, extremely durable film comparable to the finish on prefinished flooring.
Safety Considerations
With UV finishes, there is little to no risk of VOC exposure, but, due to UV light exposure, contractors do have to be careful when curing the finish. The UV lights made for curing floor finish emit a light spectrum that is incredibly intense; it is an acute form of low radiation and will cause reactionary decay in skin cells. Exposure to the light is not healthy for skin, so you should err on the side of safety and use common sense during curing. What is most important is to protect yourself and any workers around you involved in the curing process. Always protect your eyes with UV protective eyewear or face shielding, cover your skin, and apply SPF 50+ sunscreen, preferably with zinc oxide, in places where there is partial skin exposure. It is not recommended to simply wear sunscreen instead of wearing long pants, sleeves gloves and shoes. Be smart when using these machines, not complacent.
On a Real Job
The benefits of this technology are tremendous for several reasons. To illustrate this in the most practical way, it will be best for me to describe the results of a sand-and-finish job we did back in January at a local restaurant. We arrived at the restaurant at 2 a.m. to get all of the barflies out of the bar, then proceeded to move the chairs and tables off the 700-square-foot space, which had reclaimed factory floors that we originally installed and finished about four years ago.
The two-component finish had worn quite extensively, so the floors needed to be refinished. After sweeping the floor, we set up the big machine and edger to cut with 80-grit. Our intent was to skip-sand the finished reclaimed flooring, as removing the patina would be a disservice to any reclaimed floor purchased with the "dirty" top face. After three hours of sanding, the floor was ready to be cleaned and sealed. We used a high-solids, fast-drying, adhesion-promoted acrylic sanding sealer on the first coat, then waited for two hours.
During this down time, we propped open the doors and plugged in fans to exhaust the water from the sealer. After the two hours, we swiftly abraded the floor with a multi-head sander with inter-coat abrasion pads, vacuumed the floor and coated with an emulsified water-base with catalyst to speed the drying time. We had the second coat on by about 8:30 a.m. and had it dry by 10:30 a.m. We then simply abraded the edges with a 5-inch palm sander, paying special attention to the high-traffic areas, and vacuumed, tacked, and started recoating with a UV-curable topcoat by about 11 a.m. We then took lunch and waited another three hours and began to cure the floor. There were a few places that still hadn't dried completely in the cracks, as the floor was reclaimed and still had a lot of valleys where the finish could pool, so we simply wiped them out. By 3 p.m., the restaurant was open for business, just in time for happy hour.
Our experience with UV-curable coatings has been excellent for pad-and-recoats, stain jobs, commercial environments, high-end residential jobs, and any quick turn-around situations where furniture is moving in as soon as the floors are cured. These coatings are zero-VOC after the point of cure, cured 100 percent, and available for immediate use-a selling point that can't be beat.