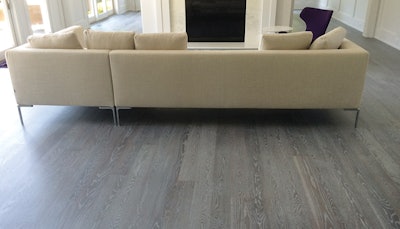
Not long ago, color for wood flooring meant a can of oil-based stain, possibly water-popped, orâfor those really pushing the envelopeâsome aniline dye. Today, oil-based stain and aniline dyes are still stalwarts of adding color to a wood floor, but the options have exploded. WFB talked with three wood flooring contractors across the country to find out what colors are hot in their markets, what products they use to create them, and tips they have for fellow contractors trying to offer something beyond color straight out of the stain can.
Dmitry Lyubomirsky, Allstate Flooring, New York City
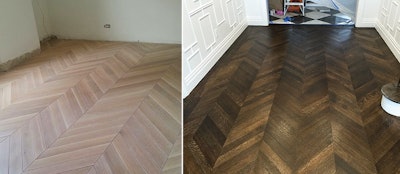
No matter what color customers have in mind, chances are good they will find it at Allstateâthe company has 1,800 samples between its prefinished and custom finishing options. And yet, the company strives to offer custom options for many customers. "It's interesting to see the end result; we try to come up with something that will have a wow factor. Every job is different and we try to give them something unique," Lyubomirsky says.
In fact, some customers demand it. "I had a customer who walked in and saw a sample in my showroom. She said, 'Who in my neighborhood has this color? How much would it cost for me to be the only person who has it?" Lyubomirsky says.
Although the colors may end up being unique, the blank slate the company starts with is typically white oakâmore than 95 percent of the company's jobs are white oak. "It looks more elegant, whether stained or natural. And it allows you to play with the tannic acids in it," he says, referring to the possibility of using reactive products that change the chemistry and therefore the species' color.
Dmitry on color
"The most important thing is sanding and prepping the floor. If the floor isn't sanded and prepped properly, it won't give you the result you're looking for."
"We are all careful to avoid a resand. It's embarrassing, and it costs money and time."
"We all know the basics, but it's fun playing with the colors and coming up with things that are unique."
"There are 20 ways to sample the same color."
"We're always looking for a way to do something that gets the same result but takes less work, both for applying it and for the long term."
What the company does with that white oak can depend on the area where the customer lives. For example, he says in the Hamptons, the customers all want shades of gray. In today's wood flooring market, there are endless possibilities to get those shades. One straightforward approach Allstate uses is to simply mix black oil-based stain with white stain (they use DuraSeal Ebony or True Black mixed with Country White) in different ratios. The option to water-pop the floor or not adds another layer of complexity that will affect the color of the stain.
Another option the company uses to create a light whitewash floor is to apply either one or two coats (depending on the color desired) of a waterborne sealer tinted by the manufacturer with a white color (they use Bona's NordicSeal) followed by a commercial-grade catalyzed waterborne topcoat (they use Bona Traffic HD)âan approach Lyubomirsky says is particularly appealing because it is a huge time saver. Yet another option for the whitewash look is to use a white penetrating oil (they like Rubio's Super White hardwax oil).
A variation on straightforward gray colors is the fumed or "ceruse" look, in which the heartwood is one color and the grain is a different color. "Depending on the grain of the wood, it creates a very unique appearance and makes it rich and elegant," Lyubomirsky says. Again, today there are options to achieve a similar look. One method is to apply the reactive product, whether it's a brand-name product specifically formulated for this process or another product, such as an iron acetate, that darkens the floor, then apply light-colored finish. Or, now there are oil-finish systems with a base coat, such as an ebony color, and a second coat, such as a white shade, designed to give the layered look, making the job easier.
When playing with these finish systems, Lyubomirsky cautions that they require caution and practice. "With resands, you have to be very careful about any contamination in the wood; you will only see it when it's too late, so we only use it on new wood with new installs," he says. "You really need to practice applying it evenly and not allow it to puddle or get too thin. Uniformity is the key. With experience, you will get better at it."
Dave and Jeremy Lorsung, WC Hardwood Floors Inc., Corona, Calif.
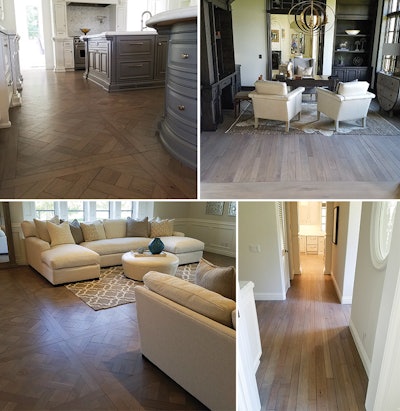
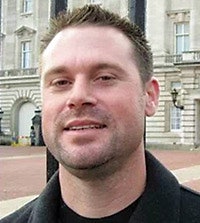
At WC Hardwood Floors, if there is a way to experiment with color on a wood floor, they've probably tried it. The company pushes the envelope for both its job-site floors and the colors they produce on their prefinishing line for floors that might be shipped anywhere in the world.
One of the biggest trends they see is a desire for the look of no finish on the floor. "Before we were doing 15 to 40 sheen, but now they want everything flat, flat, flat," says company CEO Dave Lorsung. "A lot of the finishes we're doing now are a matte with a 5 to 7 sheen."
When you're trying to achieve an exact color, those matte finishes actually make life easier, he notes. "With flat finishes, it doesn't change the appearance of the color like it does with a gloss finish," Lorsung says.
When working with custom colors, the company typically uses white oak due to the ability to manipulate the color with reactive products. They are careful to use only wood sourced from the same area of the country on a job. "If that wood is all from the same region, it's much more uniform. If it's different, then the tannins are all mixed up," Jeremy Lorsung, company vice president/sales, says. Since the tannins are the key to getting the right color reaction, too much variation in the amount of tannins leads to inconsistent color.
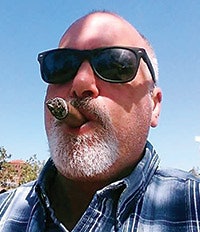
The company refers to their process of custom color manipulating the tannins as "chemical finishing." The products used vary widely. "The chemical might be as little as sodium hydroxide, or it might even be baking soda," Dave says.
Or the company might use sodium nitrate, or chlorine, or iron acetate. "They are all oxidizersâall different chemicals to make it look aged," he says. Most of them come in tubs of powder that are mixed with water in different ratios for different strengths.
For colors, the company has requests for browns, naturals, taupe and whitewashed floors, but gray is king, with probably 65â70 percent of their floors being some variation on gray.
They still get requests for black floors, but now those customers want a black that shows the grain of the wood.WC Hardwood Floors created 4,000 square feet of this chevron that was headed to a client in Japan. The rift-and-quartered white oak was fumed with ammonia, dyed, sealed with shellac, painted, sanded, coated with a water-based metallic stain and then coated with three coats of Bona's Traffic HD in satin.
The range of grays is vast, from gray-blue to gray-white to gray-black and even metallic gray. Most colors have a multi-step process, with some requiring as many as 10 steps. A typical process for a gray-blue floor, for example, might start by oxidizing the floor with a traditional steel wool and vinegar solution. "Then we might bleach it, and we might put a peroxide over that," Dave says. "If we want something to go a little brown, we might use the sodium hydroxide. If we want it whiter or just lighter, we might use hydrogen peroxide over it. We adjust the ratios of it to water for how dark or light you want to keep the oxidizer; it will turn it to a different degree of gray depending on the strength." The goal is that the product used will "hang up in the grain and look weathered," he says.
The company also uses aniline dyes, as well as a wide spectrum of oil finishes. "A lot of these oil companies make reactive stains; we play with them and apply different products to make different colors," Jeremy says.
No matter what their process, one goal is to try to keep the colors in the wood as opposed to the finish, he says.
A trend the company sees more of is customers not wanting the staining and finishing process done in the home; instead the company will prefinish the flooring, install it and apply only the final coat on-site. Doing so allows them to do things that might be too difficult to achieve on a job site, Jeremy says. For example, the company recently did a chevron floor with a metallic finish that was shipped to Japan. To match the sample they were given, they used a silver oil-based stain sourced from a local paint supplier (for more details, see the photo on this page).
When pushing the envelope of experimenting with different products, especially ones not made for the wood flooring industry, there's one overall tip that might be the most important of all: "Just ask the finish manufacturer," Dave says.
Dave & Jeremy on color
"When you don't write down the steps and ratios and weights and equations, you can't duplicate the same colors."
"When making custom colors, it's a lot of experimenting with different ratios."
"We fight it every day: 'I got this sample; can you match this?'"
"Between the finishing steps, different sanding processes will also get different looksâdifferent degrees of colors, too."
"When working with aniline dye, the faster the better. You've gotta get the floor wet."
Steve Belrose, Belrose Hardwood, Hopkins, Minn.
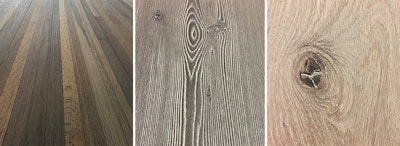
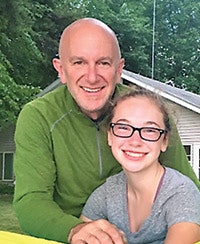
In his Twin Cities market and beyond, Steve Belrose (shown at left with his daughter, Claire) focuses on providing wood flooring outside the norm. "The way that architects and designers utilize our company is that we design a floor for that specific customer. Even if they already know they like 5-inch white oak, we don't just say, 'Hey, you like antique brown with a couple coats of poly?' We get into it with them," he says. "We're trying to bring it to the next level."
A little more than half of the company's floors use traditional hard finishes, such as waterbornes, conversion varnish and oil-modified poly, although at least 90 percent of those floors include some color process, oftentimes including difficult-to-stain species such as ipĂŠ and maple. The other floorsâclose to half of their jobsâuse some sort of oil-finish system, including all the color options that come along with those products.
In their local market, Belrose says the grays are still alive, but not the blue-grays. Instead, it's brown-grays and light grays "with a little more nuance," as he says. "It's easier for architects and designers to design around a color that goes with more things. If you can do a color that's more of a chameleon, that makes their job easier."
"The dark colors, the full big browns are still around, but the change in that trend isâat least in Minneapolisâthey don't want reds," he explains. "Then I would say the newest trend we're seeing is back to the lighter colors: natural wood colors, stain colors, even that light cerused white oak."
Belrose says he's surprised by the requests for light colors, particularly when the request is for light colors on species such as black walnut or white oak. "Or they want red oak with no red. If you already own red oak floors and red's the devil now, do you rip out all your floors? Or do you figure out how to neutralize it or push it one way or the other?" he says, adding that you might be able to accomplish that with a dye, for example.
Another important trend Belrose sees in his market is what he refers to as "complex colors," meaning layers of color, which could be some sort of reactive productâsuch as an iron acetate, lye, an acid-wash or a bleachâfollowed by a colored oil finish. He says when those colors first started appearing on the market, they were either a black background with a white oil or white oil followed by blackâworking with extremes. Today, he finds the colors tend to be much more subtle, tone-on-tone colors.
Depending on the reactive product, the floor might turn lighter (for bleach) or darker (with an iron acetate, for example). Although white oak is the standby for using reactives due to the tannins in the species, Belrose says they test reactives on all sorts of different species, from ash to maple, for different looks.
When bleaching a floor, the company uses a two-part bleach purchased from a local paint supplier. "Bleach is challengingâit doesn't feel good on your eyes and on your skin, and you have to wear protection," Belrose says. "Read the directions, because every manufacturer is a little different."
Belrose leans heavily on his manufacturers and says he views them as partners. When in doubt, he picks up the phone for answers to his specific question. "I want them to advise me based on their chemistry and R and D; they don't have to prove anything to me because they've already done the homework," he says.
Beyond that, Belrose advises anyone experimenting with different color processes to practice extensively before trying it on an actual floor, and remember that experimenting costs both time and money. "You need to practice on a floor you don't have to redo," he advises, citing the old axiom that practice makes perfect.
Once the right recipe is established and you're on the actual job site, "make sure you have enough of everything. It's really important to not run out of the components for your signature look. Don't go there with just enough," he says.
He also strongly advises watching other people practice the techniques first, whether in a live demo, on someone else's job site or in a YouTube video.
With all those caveats, Belrose strongly encourages other wood flooring pros to pursue their own custom ideas and experimentation with color. "The definition of luxury isn't necessarily about what something costs, it's getting exactly what you wanted. So you take a common thing and do something uncommon with it. That defines our market and our business.
Steve on color
"Practicing color on the actual floor you are doing leads to heartache and confusion and delay."
"Consistent volume equals consistent color. If you put more on, you'll get a different color."
"If you show it, you will sell it."
"An even sand/scratch pattern is pretty much the holy grail to getting a floor that looks great."
"I solve most of my finishing problems with a well-thought-out question for the finish manufacturer."