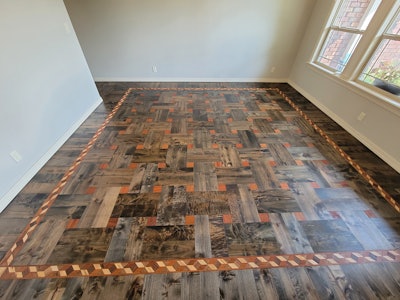
When it comes to custom flooring projects like this one, Jonathan Colpron’s biggest piece of advice is simple: “Slow and steady is good.”
“Don't get into a rush with any part of the project, just kind of let the project transform itself,” says Jonathan, who runs Colpron Custom Floors LLC with his wife, Jessica, in Emmett, Idaho.
The approach paid off in this unique dining room parquet, which features western maple, Brazilian cherry, walnut and hard maple. The Brazilian cherry was selected to match the home’s front door, and the homeowners, originally from Denmark, liked parquet floors, Jonathan says. The border was designed to match the recessed ceiling in the 170-square-foot room. The Colprons collaborated on the design with Dave Marzalek of DM Hardwood Designs. "We had help from Dave and learned how to do some really cool shapes,” Jonathan says.
They cut the western maple parquet using a home-built plywood sled, then cut the smaller border pieces using an Incra miter combo for extra precision. “Every piece of the border we actually hand-sanded to its final shape to make sure they fit,” Jonathan says.
For the corners of the border they ended up using hard maple end grain harvested from the Colprons’ own backyard. "It just kind of added a little spice to it,” Jonathan says. “We weren't really sure what we wanted to do for the corners and were trying to brainstorm, and it just turned out really great."
The cutting and milling of everything took around two and a half months, after which they began snapping lines on the OSB subfloor and gluing the parquet from the center out. They then cut in the border with a track saw and installed the walnut, Brazilian cherry and hard maple pieces with a FastenMaster hot-melt adhesive gun.
When all the pieces were in place, they sanded at a 45-degree angle, used filler, then sanded again with a planetary sander. They then taped off the Brazilian cherry squares and border and water-popped the western maple, returning the next day to apply a coat of black penetrating oil, which they later followed with a second coat. “We then gave it about five days to dry, peeled all the tape and then we basically went in there and did some detail work, touching up wherever bleedback was,” Jonathan says. They added a final coat of clear penetrating oil, ”which really made everything else pop,” Jonathan adds.
"The client was ecstatic,” Jonathan says. “They were very, very happy and they have recommended us to many, many people.”
The Colprons’ “slow and steady” approach to the project has continued to pay off down the road—literally. "We used it as the wrap on our van, too, which was pretty cool,” Jonathan says.
Suppliers:
Abrasives: Bona, Norton Abrasives | Adhesive: Loba-Wakol | Buffer, Edger: American Sanders | Filler: Loba EZ Fill Pro, Woodwise | Finish: Loba 2K Impact Oil Black and Transparent | Moisture barrier: Loba-Wakol PU280 | Moisture meter: Wagner Orion 950 | Big machine: American Sanders Legend | Palm sander: Festool Orbital ETS 150 | Saws: Makita chop saw, SawStop table saw, Metabo table saw, Festool track saw