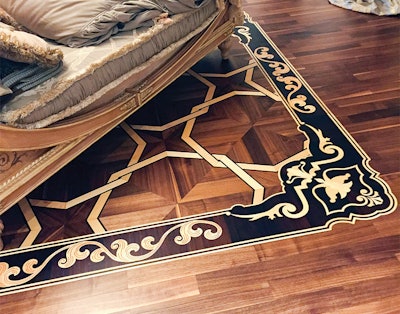
Here are the six winners of the first annual Wood Floor Business Design Award contest, and we're thrilled to share them with you. The contest began with the idea of inclusivity—let's create a contest open to anyone in the industry, regardless of affiliation, location, years of experience or skill specialty. While we included timeless categories like Best Residential, Best Commercial and Readers' Choice (chosen through an online survey), we also expanded into new categories to feature the craftspeople behind impressive gymnasium floors and stairways. And we created the Next Generation category—open to companies owned by someone under the age of 35—to give a platform for up-and-coming wood flooring artists to show their abilities. The winners were chosen by an independent panel of wood flooring experts, and prizes include a $500 Visa gift card, as well as a package of prizes from each of our sponsors: Bona and DuraSeal. Without further ado, we present the winners of our premier contest.
Best Residential
Czar Floors | Huntingdon Valley, Pa.
Ask Edward Tsvilik, vice president of Czar Floors Inc., to describe the design style for this home and he says it's "over-the-top-ornate, very fancy ... that's what a lot of affluent people are trying to replicate, because they think that's how the rich and famous do it."
Tsvilik would know—such projects are right in the wheelhouse for his company, which got this job through word-of-mouth after having done the wood floors for the clients' neighbors. The neighborhood is a "very affluent area," Tsvilik says. "They go to each other's houses and say, 'We'd like something better'—just to show off."
There is plenty to show off in this home, a sprawling 15,000-square-foot project in the New York City area. Tsvilik knew the clients were demanding from the beginning. They readily agreed to Tsvilik's proposed design for the floor, but "when I started giving the general spiel about the nature of wood and that you have to have certain expectations, and that the wood moves, he said, 'Do whatever you want, but I want to see no gaps in my floor.'" Adding to the complexity was the fact that the entire home had hydronic radiant heat.
Despite that, Tsvilik was unfazed. "We usually tell them that we will do what is humanly and physically possible—we can't break the laws of physics, but we will do what we can," he says. Having worked extensively with similar projects, he knew they would rely heavily on species known for stability, such as straight-grain maple, walnut and rift and quartered white oak. "We showed them a selection of wood that we knew would be stable, and they picked from that limited selection," he explains. "We could have introduced all sorts of colors with more variety, but with radiant heat, we had to keep our list shorter."
Additionally, the company built the flooring, from the parquet to the CNC-cut border, as engineered with a 5⁄16-inch wear layer on top of Baltic birch plywood. They also made it clear from the initial stages of the project what was necessary from the other contractors and the client in order to maintain a floor with no gaps. "We will spell it out for them what we expect from their HVAC contractor, what we expect from their radiant heat contractors, what we expect from them how they maintain their environment in their rooms," Tsvilik says. "We always give them hygrometers to measure the relative humidity, and we want to make sure they have an in-house humidifier in the wintertime and make sure it is serviced every year. We try to cover our behind to have all the bases covered." These expectations are all included in the contract, as well. Additionally, Czar installed in-floor sensors that take continual temperature and relative humidity readings.
All the precautions and meticulous planning paid off for the project, which took two years to complete. The clients, even with their extraordinary expectations, "love it," Tsvilik says, adding that he's hoping the word-of-mouth in the neighborhood continues for more ornate projects.—K.M.W.
Suppliers: Advertisers in this issue appear in bold.
Abrasive: 3M | Adhesive: Bostik | Buffer, Filler, Finish: Bona US | Borders/Inlays, Wood Floors: Czar Floors | Sander: Lägler (Palo Duro)| Router, Saws: Festool
The Best Residential Category is sponsored by Bona US.
Best Commercial
Yantarnaya Pryad-Parquet | Khimki, Russia
Let's hope the professors who meet in this room to hear Ph.D. candidates defend their theses aren't wood flooring people—they might be too distracted to pay attention.
Yantarnaya Pryad-Parquet installed this dazzling 278-square-foot parquet floor inside a dissertation room at the Peoples' Friendship University of Russia (RUDN) in Moscow. The wood floor tile pattern on the outskirt of the room features ash, merbau and maple, while the inlays in the center of the commanding oval table are ash, merbau, maple, oak, walnut and wenge.
The flooring patterns were inspired by the room itself. Yantarnaya wanted the pattern and the inlays to emphasize the importance and solemnity inherent in the room's function. Ph.D. candidates have been devoting themselves to their field of study for most of their adult lives, and the formal Rococo-style designs respectfully celebrate the work it took to come this far, says Anastasia Galkina, export manager.
It took Yantarnaya 30 days to manufacture the parquet. The octagons are close to 17 inches wide. In the middle of the table, the smaller inlays measure roughly 67 square feet and the large center inlay an impressive 109 square feet.
The team spent 25 days gluing down the parquet and sanding and finishing it on-site. They worked by day but also by night to minimize the disturbance to nearby classrooms.
"The customer was very happy with the quality and beauty of the parquet," Galkina says. It appears the floor passed its defense. Consider it a postdoc.—A.A.
Suppliers: Advertisers in this issue appear in bold.
Abrasive: 3M | Adhesive, Filler, Finish: Chimiver Panseri S.p.A | Edger: Mafell
The Best Commercial Category is sponsored by DuraSeal.
Best Stairs
Artistic Floors by Design Inc. | Parker, Colo.
"In the squares and in the streets we are placing our work … Art should attend us everywhere that life flows and acts." This quote from Russian artist Vladimir Tatlin resonated with Artistic Floors by Design Inc.'s Joe Rocco. Far from a regular floor guy, Rocco believes that art should, indeed, "attend us everywhere," including on the floors on which we walk, and his mind is often consumed with how to create that art.
"I will find myself looking outside in the backyard, and something will catch my eye. I'll think, 'That's an interesting shape or texture … how would you bring that into the mundane of 2¼ strip oak?' It's just something that kind of comes out of me in weird ways," he says. In this case, it came out of him in the form of these elaborate backlit stairs for his own home.
The job that triggered the inspiration for this floor was one six or seven years ago that had puck lighting in the floor, and Rocco had to cut around those lights. "That got me to thinking about, 'How does lighting affect flooring?'" he says. Then recently he noticed backlit translucent tile in design magazines and began developing his idea for these stairs.
The floral pattern coordinates with the large carved teak artwork in his home, including a piece that hangs directly over the landing. The pattern was blown up at a local printer and the design transferred onto the sapele base for the landing. The piece consists of four elevations: The highest is the pattern that withstands foot traffic, the second elevation is the background, the third elevation is the pattern with portions too fine to withstand foot traffic, and the lowest elevation is a total cutaway of wood to allow the LED illumination from below. Rocco began by cutting through the sapele to create the voids that would later be illuminated and represent the shimmering of early morning dew on this tropical floral pattern. He then hand-routered around the design's perimeter using various diameter router bits. Rocco and his employee, Kevin Eder, completed removing the excess material from the background elevation using a combination of hand routing and a homemade router sled. Finally, the smallest areas, with fine detail that would have broken off with foot traffic, were hand-carved into the background elevation.
With the routering, carving and sanding completed, the raised and hand-carved portions were dyed black using a small artist's brush and Q-tips for the smallest areas. They were then coated with Miracle Oil natural. The rest of the floor was sealed with Lenmar Rapid Seal, a dual-purpose poly sealer, to bring out the natural appearance of the sapele and then top-coated with Arboritec's 2K Genuine, a commercial matte waterborne finish.
While she thought it was "gorgeous," at first, Rocco's wife and business partner, Joni, was worried about actually using it. "My biggest fear was walking across it, because to me it is art, and I was freaked out about being too careful with it," she says. Despite those fears, the stairs have held up fine in a busy household of six (seven if you include Diesel, the bulldog).
The stairs join two previous Wood Floor of the Year winning floors and Joe's social media sensation bent floor/bar top as stunning features of their home, making life a little bit easier for Joni, who handles the company's sales. "It's a great sales point for me to have our own home look like a showroom," she says.—K.M.W.
Suppliers: Advertisers in this issue appear in bold.
Abrasive, Palm Sander: Festool | Finish: Arboritec, Lenmar | Router: Bosch, Festool
The Best Stairs Category is sponsored by DuraSeal.
Best Gym
Praters Athletic Flooring | Chattanooga, Tenn.
The more unusual the design idea for a basketball floor, the better Praters Athletic Flooring President John Prater likes it.
"People will call and say, 'We've got this crazy idea,' and we say, 'We love crazy ideas,'" he says. "For us, when you decide to take a hardwood court down to bare wood, you've got a blank canvas to use your imagination and try to get your message out."
Such was the case for this University of Louisiana at Lafayette floor. Praters had handled the graphics for the university's new portable floor about a decade ago, and now the university approached Praters with their idea for a new design—one covering the entire floor with a scene straight from the bayou, complete with cypress trees and draping Spanish moss.
"Even though it's very detailed, it was actually very simple," Prater says, explaining that there was only one color on the floor for the main design. The fact that such a floor could be considered "simple" speaks to Praters' extensive experience with such projects—the company did the graphics for about 60 portable courts last year alone (a task, Prater says, that is "not for the faint of heart").
"It was a matter of sanding the floor flat, then putting the designs into our cutting software for our vinyl templates, placing it, pulling it…" In other words, standard operating procedure for Praters. Two coats of pigmented waterborne sealer were used to achieve the color of the swamp, then two more coats of sealer were applied to the entire floor before it was abraded and the court lines and other graphics were applied. A typical floor takes about two weeks for the Praters crew to handle, but the detail of this design added about another week to the process.
Prater demurs when asked how much such graphics cost, but does offer that "there's probably $10,000 just in mask and cutting time just to prepare" this floor. Extensive custom graphics like this can easily double or triple the price of a typical floor, he says, but these days branding is going from the pros to the middle schools. "The Kentuckys and North Carolinas don't have to draw attention through the floor, because they are who they are, but when you get to [universities] that really want to set their athletics apart from others, branding is very important, and it's worth it," he says.
Now that companies like Praters have pushed the envelope to make such floors commonplace, what is next? "Where are things going to go now? I don't know, that's the big question," Prater says. One safe bet is that Praters will be at the forefront.—K.M.W.
Suppliers: Advertisers in this issue appear in bold.
Abrasive: Norton | Buffer, Finish: Bona US | Sander: Hummel (Palo Duro) | Wood Flooring: Connor Sports
The Best Gym Category is sponsored by Bona US.
Next Generation
Parquet Nobre | Rio de Janeiro, Brazil
Where the sea meets the sand. That's the concept Thiago Barros, the 31-year-old owner of Parquet Nobre in Rio de Janeiro, Brazil, was given by the interior designer who hired him to create a floor inside a contemporary pop-up jewelry store in early 2016.
"I thought, 'Houston, we have a problem,'" Barros says. But he's joking. "I love challenges, and I thought it was a huge opportunity to show the skills of our company's team."
He came up with an idea to "collide" two flooring materials. He chose reclaimed wood with rustic patinas of browns and blondes to represent the beach, while the sea would be concrete. Where the two materials meet, with the concrete filling the open, v-shaped side of the chevron, it gives the illusion that the concrete is overtaking the wood floor—the sea waves stretching toward the tideline.
"On the beach when a wave hits the sand, the sea pulls it back, leaving traces of water on it," Barros says. "So the bits of flooring in the concrete represent that moment of the sea invading the sand."
Barros started the installation by creating a boundary between the space for the wood floor and the concrete, and the "sea" was filled with 2¾-inch-thick concrete. Once the concrete cured, the boundary was removed and Barros began installing the wood floor. First he laid 1½-inch-thick sleepers and then 3⁄8-inch-thick plywood. Finally he glued and nailed the chevron, which featured straight-edge 3-inch-wide lapacho and 1½-inch-wide pau marfim. The floor was left unsanded to preserve the rustic patina of the wood, which had been salvaged from old buildings in Rio. Barros then finished the floor with Bona Mega Natural.
At 322 square feet, the wood floor was a fraction of the total size of the room, but it made a huge impact. The reclaimed wood chevron created a cozy and alluring corner that provided an aesthetically pleasing contrast with the rest of the contemporary space. It's a perfect example of the new direction Barros, who took over the company from his father only two years ago, is trying to steer Parquet Nobre.
"Our innovation is going beyond the concept of just putting wood on the floor," he says. "It's bringing design to it. It's bringing thinking to it."
Barros says he's the youngest wood floor company owner that he knows of in his market. Considering the splash this sea-meets-sand floor made, it's obvious he can swim with the big fish.—A.A.
Suppliers: Advertisers in this issue appear in bold.
Abrasive, Adhesive, Finish, Sander (Big Machine), Sander (Palm): Bona Brazil
The Next Generation Category is sponsored by Bona US.
Readers' Choice
Metropolitan Hardwood Floors | Denver
It's a challenge that faces anyone designing a showroom: How to showcase as much as possible while creating an elegant space that doesn't overwhelm the visitor? Metropolitan came up with a novel solution at its studio location in Denver—and did it so well it was selected as the Readers' Choice winner.
The company was able to include more than 100 large samples, roughly 8½-square-feet each, into the 1,500-square-foot space without cluttering the showroom thanks to a large central storage cube. It's essentially a large box smack-dab in the center of the space, and very well could have been an eyesore were it not for the interior designer's simple but brilliant idea: wrap the three exterior walls of the hub in wood flooring, making one side herringbone that climbs up from the floor.
"[The cube] does dominate the space," says Chris Allman, a Metropolitan architect an design representative, "So if we didn't do something elegant on there, we felt it would have been very distracting."
The wall covering is the same product used on the floor in the rest of the showroom: an on-trend, 5-inch-wide engineered European oak treated with a natural chemical reaction stain (similar to using steel wool and vinegar, but the exact process is proprietary) from the company's Kentwood Originals Antiqued Oak line. The product was chosen to complement the industrial aesthetic of the showroom, which is located in a renovated bindery plant built in the early 1900s.
While the wood flooring laid across the studio floor was glued onto sound-reduction matting rolled on top of the slab, the flooring for the walls was blind-nailed and glued along the tongue. The flooring was straight-laid on two sides of the wall. On the third, Allman and two others installed the flooring in a herringbone pattern such that it seamlessly continues a field of herringbone that provides a seating area with a coffee table, couch and two chairs.
"We wanted to encourage people to sit down and be comfortable," Allman says. "This is a hospitality showroom, and we wanted a nice comfortable couch and chairs and a little bit of a home setting so people could start to visualize what the floor would look like in the home with the furniture."
The showroom has been a hit with the designers and architects for whom it was intended, and the herringbone floor has received high praise. The attention turned into demand—so much so that Metropolitan began production of a precut herringbone product in the same color to save its clients from having to do it themselves.
For Allman, who carefully hand-stained all the raw edges when they cut the herringbone, that comes a little late: "It would have been nice to make this product before so we wouldn't have had to cut anything," he jokes.—A.A.
Suppliers: Advertisers in this issue appear in bold.
Adhesive, Finish, Moisture barrier, Underlayment: Metropolitan | Router: Amana | Saws: Dewalt, Hitachi | Moisture meter: Delmhorst Instrument Co.
The Readers' Choice Category is sponsored by DuraSeal.