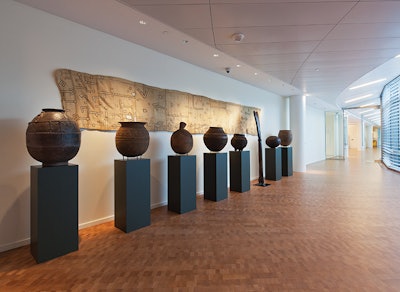
Photos: Sean Airhart/NBBJ
Software created by Microsoft transformed the way businesses operate on a day-to-day basis. From emails, to PowerPoint presentations, to spreadsheets, these tools helped companies, large and small, in myriad industries work faster, connect more easily and be more productive. But no matter how powerful these digital tools are, they cannot replace the benefits of an in-person collaboration: the morning shop meeting, the lunch break with colleagues, the chance hallway encounter.
Before 2011 this was something missing at the Bill & Melinda Gates Foundation, the world's largest philanthropic nonprofit started by the Microsoft co-founder and his wife. With staff spread throughout five leased buildings in Seattle, Melinda Gates started in 2006 to craft a vision for a new campus that could support all of the nonprofit's nearly 1,000 employees, who work to improve health, create opportunity, advance education and fight poverty around the world. The work culminated in the June 2011 opening of the foundation's 900,000-square-foot headquarters in the heart of the city.
Built at a cost of $500 million and occupying an entire city block, the campus comprises two office buildings (one anchoring the lot's northwest corner and another to the southeast), a reception area and a visitor's center. It boasts several features designed to lessen its carbon footprint, including a vegetation-covered, in-ground parking ramp; a million-gallon tank that stores rainwater for use in toilets, irrigation and reflecting pools; solar energy installations; and daylighting that keeps all workstations within 30 feet of sunlight. What's more, over 20 percent of the campus was built using recycled or regional materials extracted and manufactured within 500 miles of the job site-including some 42,000 square feet of beautiful end-grain alder wood flooring. With the assistance of architectural firm NBBJ and subcontractors of the Pacific Northwest, the Bill & Melinda Gates Foundation has planted permanent roots in Seattle and can now offer its employees a holistic workplace in which they can strive to improve lives around the world.
In the reception area, Seattle-based Northwest Millworks installed end-grain alder on walls and ceiling portions, while the GC also installed cherry-colored acoustic ceiling cladding made by Decoustics.
Uptown in Downtown
The Bill & Melinda Gates Foundation's 12-acre campus makes for yet another architectural destination in downtown Seattle's Uptown neighborhood. The campus sits kitty-corner from the world-famous Seattle Center, the arts and entertainment park that is home to the Space Needle and the Frank Gehry-designed Experience Music Project museum. On the foundation's block, the V-shaped office buildings are the two most prominent features. Their interiors are characterized by glass, steel and expansive daylighting, and there are many common spaces where workers can see their colleagues and work in groups large and small. Underfoot, end-grain alder flooring adds an organic element and reinforces the foundation's connection to the Pacific Northwest.
The 1-inch-thick, 31/4-inch-wide alder was manufactured by Lake Oswego, Ore.-based Oregon Lumber Company. The company, situated 180 miles south of Seattle, makes solid flooring, solid/engineered hybrid flooring and end-grain flooring for commercial applications such as the foundation's campus. Most of the company's end-grain flooring is reclaimed from pre-consumer waste, but this particular product came from FSC-certified lumber supplied by Cascade Lumber Inc. of Camano Island, Wash. "[NBBJ] wanted something unique; they wanted something durable; they wanted something that would add warmth in an environment where there is a lot of glass and other materials that are more sterile than wood," says Charles Couch, Oregon Lumber's president and owner. "They also wanted something that would lend itself to the Northwest." The wood flooring was installed in the office structures' common spaces and stair treads, while it also features prominently on walls and ceiling in the reception building. "They liked the look of the end-grain and then wanted to highlight it in a way other than just on the floors," Couch says.
Bellevue, Wash.-based commercial installation firm Western Flooring & Hardwood created nearly 500 custom stair treads used throughout the campus.
Fashion a Floor
For installation duties, NBBJ turned to Bellevue, Wash.-based Western Flooring & Hardwood and its president, Mark Sessions. This company specializes in installing large commercial and residential floors and is the unionized arm of Western Tile & Marble, a firm that won an NWFA Floor of the Year award in 2004 for work at Las Vegas' Palms casino, which Sessions also led. Western Flooring & Hardwood started work at the campus by installing a layer of ¾-inch plywood that was nailed and glued to the concrete raised-access subfloor. Sessions and his team installed the plywood to minimize the chances of panelization, or separation along the subfloor's seams, which he's seen elsewhere from raised-access subfloors.
With the plywood in place, Western Flooring & Hardwood next installed the alder pieces. About 15-20 of its workers would take on an area at one time, gluing and then side-nailing the alder pieces into place, Sessions says. About 7,000 square feet of alder was installed in the campus's reception area, while 10,000 was installed in the southeast office building; the remaining 25,000 square feet was installed in the northwest office building, which includes the lion's share of common space in a large atrium. Wherever the alder gave way to a different floor covering, Sessions' workers installed a ¼-inch-wide strip of cork to accommodate for expansion.
With the flooring installed, the crew next flattened the floors with three drum-sander passes using a 60-80-100 grit sequence; following this, they did three passes with a multi-disc sander. After the flooring was flattened, Sessions' crew applied a hardening-oil finish. One of the biggest challenges on this job was coordinating crews so they could finish their work while so many other contractors worked around them, Sessions says. "It had to be phased from installation, to sanding, to finishing," he says. "We mapped it all out in a calendar and sequenced it. For a while, we'd have one group of guys installing, another sanding and another group of guys doing the application of the oil."
"All my lead guys took a copy of the schedule, folded it up and put it in their pockets," Sessions says. "Then they just walked around and made sure everyone was hitting their milestones. It was detailed out not quite to the hour but the half-day. They knew the flooring was dry in one spot and that they needed to apply oil and give it the right amount of dry time."
Another challenge was applying that much hardening oil over such large areas; they practiced on a mock 250-square-foot alder floor. "We were confident that we had it down, but it was much more difficult when we had to take the steps we were doing on the 250-square-foot area and translate that to an 8,000-square-foot atrium that all had to be finished at the same time for uniform appearance." Sessions recalls that he and his crew learned very quickly that lap marks would be their worst enemy during the finishing process. "Eventually we got it down to where we had one guy rolling and two guys behind-one guy painting between the roller lines and the other guy blending the two together. Once that was done, we let it dry for 48 hours and then applied the second coat."
Between the first and second coats Sessions spot-applied a filler he describes as a "dough" comprising sanding dust mixed with oil finish. A third finish coat was applied using a buffer with a synthetic abrasive pad equivalent to a 400 grit, and then they applied a fourth coat-"to make it pop as we walked out the door," he says.
The staircases throughout the campus's office buildings-which have six stories-posed another challenge for Western Flooring & Hardwood. Each staircase has a unique, elegant curve to it, so Sessions and his crew were required to custom-make each tread, and then sand and finish them. In total there were 500 treads, so the task was time-consuming.
A 1/4-inch cork strip was installed where wood flooring met other floor coverings to accommodate expansion.
Sustainable Vision
After work on the Bill & Melinda Gates Foundation's new campus was completed, the accolades began piling up. With all its energy-saving features, it has the distinction of being the world's largest newly constructed nonprofit LEED Platinum-certified building in the world (NBBJ originally aimed for Silver certification). "Most satisfying is that this sustainability achievement was the result of an integrated and engaged design process, not a race to acquire points," says Cormac Deavy, a principal at Arup, a consulting firm that assisted with the project's design. "The design choices that the team selected have resulted in a high performance building." The campus also garnered praise from Interior Design, winning highest honors for large corporate offices in the magazine's Best of Year 2012 contest. (The campus has also won recognition from the American Institute of Steel Construction as well as Engineering News-Record.)
Reflected in the foundation's sleek, new corporate headquarters is its commitment to sustainability and its philosophy that "all lives have equal value." It makes perfect sense, then, that the foundation took that motto and applied it to future generations through building a sustainable campus. Most important is the fact the foundation's employees now have a centralized office-a place that will promote creative and collaborative work among staff, a place where the foundation can finally plant roots and grow well into the future.
Project Details
Architect: NBBJ (Seattle)General contractor: Sellen Construction (Seattle)Lumber supplier: Cascade Hardwood LLC (Chehalis, Wash.)Flooring manufacturer: Oregon Lumber (Lake Oswego, Ore.)Finish manufacturer: Woca Denmark (Lunderskov, Denmark)Flooring installer: Western Flooring & Hardwood (Bellevue, Wash.)