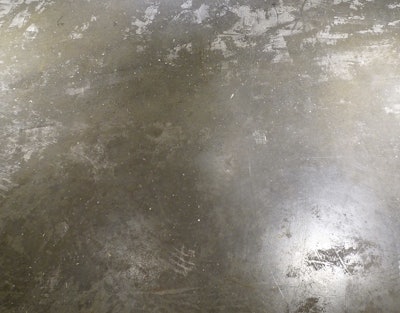
Editor’s note: Wood flooring expert Roy Reichow passed away on Sept. 13, 2021. The following column was written shortly before he passed as part of his constant effort to educate the wood flooring community.
The Homeowner’s Issue
In late December, the homeowner purchased the home with a 3-inch natural red oak engineered hardwood floor installed in the living room. After replacing the floor with a glued-down 7-inch-wide engineered plank, the wood floor became loose and began to make noise. The retailer said it appeared to be a manufacturer-related issue and needed to be inspected.
Roy: The Inspector’s Observations
My inspection took place on the day the wood floor in question was being replaced with new material. Plank extraction was observed in two areas, and I noticed the concrete was slick-troweled (smooth). The flooring adhesive manufacturer requires a concrete surface preparation (CSP) grade of 2 or greater. The inspection revealed the concrete was not prepared to the adhesive manufacturer’s requirements before installation of the wide plank floor, so the error was installation-related.
Blake: The Attorney’s Analysis
As noted above, the inspection revealed the error was related to the installation, so there does not appear to be a question about who is responsible. If the installer failed to properly prepare the concrete, then the installer is responsible to fix the problem. However, this case presents a unique twist because apparently the floor was already being replaced at the time the inspection occurred. The law in most states allows the responsible party an opportunity to inspect the work and fix any problems. It is a common rule that if the owner fixes the issue before the responsible party has a chance to inspect and fix it, then the responsible party is only liable for what he would have spent to correct the problem. In this case, it would have likely cost the original installer less to replace the floor than the retail amount the owner paid someone else. For example, if the owner paid $10,000 to have someone else replace the floor, but it would have only cost the original installer $7,500 to do the work using his own employees and with no markup, then the installer would only be on the hook for $7,500. The takeaway is that while it might be clear who is responsible for a problem, if an owner acts too hastily and fixes the problem before allowing all parties to inspect the issues and offer a cure, the owner might be leaving money on the table.