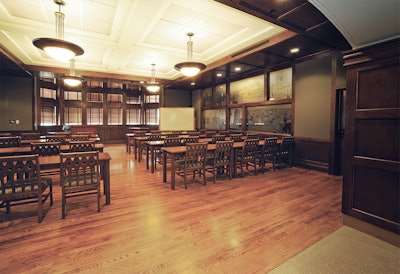
It's likely that grand ideas were always circulating in Brown Ayres' mind as he strode the University of Tennessee campus paths during his tenure as 12th president from 1904 until his death in 1919. When he took the helm of the school, it was already more than 100 years old. Originally located in what is today downtown Knoxville, the university moved to the 40-acre tract known as "The Hill" in 1828.
To help modernize his university, thus bringing it in line with its newly acquired national identity as a multidisciplinary research and education institution, Brown Ayres wanted to build a grand structure at the top of The Hill-the college's geographic focal point-that would replace three smaller structures already there. Though Brown Ayres would not live to see the culmination of his plans, his dream was realized in Ayres Hall, a neo-Gothic behemoth made from brick and mortar-and ¾-inch beech wood floors-that served as a physical projection of Tennessee's educational prowess.
In recent years, though, it was Ayres Hall that was deemed antiquated. In pockets throughout the entire building, the beech flooring bore decades of damage from spilled paint, plaster and water, in addition to wear from the foot traffic of thousands of students. An ancient HVAC system left the hall too hot and stifling for modern sensibilities. Classrooms were short on conveniently placed outlets, leaving teachers in a lurch when they needed to use AV equipment. The building was missing elevators, as well, and the fourth floor-"the tower"-had been closed since the 1970s by order of the fire marshal for being out of code. Ayres Hall was badly in need of a renovation.
This wood floor in a dean's office on Ayres Hall's third floor comprises 100-percent salvaged solid beech.Photo by Nick Meyers
As part of a comprehensive $23 million renovation project, Chattanooga, Tenn.-based Praters Inc. was tapped to renovate wood floors throughout the 100,000-square-foot building. Other interior renovations included lowering ceilings to accommodate utilities, enclosing stairways to conform with fire codes, expanding and upgrading bathrooms, upgrading lighting with energy-saving features, relocating door handles to conform with ADA requirements, and a plethora of other upgrades, both large and small. On the façade, the hall's original red tile roof was removed and reinstalled, four clocks originally left out of the building due to lack of funds were added, and the original window trim was refurbished, among other improvements.
Helping renovate an old educational building is nothing new for Praters. The company landed its first such job in 2000 through working with the Metropolitan Nashville Public Schools; officials were renovating a school that was built in the 1920s. "I found that the majority of classrooms had original wood flooring that was covered with carpet or vinyl over the years," John Prater, president of Praters Inc., says of that first project. "I put a proposal together insisting they refurbish the wood flooring in lieu of tearing out and replacing it with concrete or some other floor covering. Plus, we found that, overall, it was cheaper to renovate the existing hardwood. They liked that." Since then, Praters has completed more than a dozen similar jobs, and Prater says his company has made itself a good niche in Tennessee renovating old educational buildings.
Decades of damage were evident on Ayres Hall's old wood floors (top), including spilled paint and plaster. In addition to renovating the floors, Praters repaired damaged subfloors (middle and bottom) so they could accommodate new utilities.Photos by Nick Meyers
Much of the success of the project at the University of Tennessee can be traced back to the bid process, says Prater, who is himself a UT alum and has vivid memories of attending math classes in Ayres Hall as part of his business degree in the mid '80s. His team began by individually inspecting each of Ayres Hall's 86 rooms, detailing exactly what would need to be done in each one. From these notes they compiled a 10-page report and submitted it to architectural firms Weeks Ambrose and McDonald, and Ross/Fowler, which were overseeing the project together. On the day that bids were due, Prater noticed most other subcontractors competing for work in Ayres Hall submitted simple one-page summaries of the work. Prater is convinced it was this diligence up front that landed the job for his company. "Heading into making our bid, we had blueprints and specifications, but we really didn't have anything too detailed as far as the square footage of what needed to be repaired and what was salvageable," Prater says. "Instead of just blowing out numbers, we decided to take it room by room and make our own judgment and summary for what needed to happen in that particular room. We quantified each room and then submitted that info to the architects. In the end, they pretty much accepted everything that we recommended."
The project was divided into three components. The majority of flooring in the three main levels and tower would be torn out and as much as possible would be salvaged for reinstallation; this meant a sizeable amount of new material would need to be installed, as well. Floors in just a few rooms on floors one through three would be left in place since, during the bid process, they were deemed structurally sufficient. Prater and his team calculated that they would have enough salvageable material from the tower to fill in the un-salvageable gaps on the main floors; this meant that floors one through three would be completely outfitted with original, salvaged material. As Prater puts it, "We sacrificed flooring on the fourth floor to produce 100 percent original flooring on the first through third floors." The project's second component, then, would be installing new solid unfinished beech flooring in the tower. The last component would be the basement, which would receive a new prefinished ash floor since a prefinished engineered beech product proved difficult to come by.
From the outset, the entire project was deemed a "historical renovation." This meant that, instead of taking extra measures to preserve the historical appearance of Ayres Hall, enhancing building performance for future use would be given priority. In the end, Praters was expected to outfit Ayres Hall with wood floors that would accommodate state-of-the-art HVAC, IT and electrical systems underneath. "We opted to provide them with a floor that would perform for another 100 years instead of preserving something that was not going to last," Prater says.
Knoxville-based Johnson & Galyon handled removing and salvaging the existing beech floors in Ayres Hall's three main levels and tower. "We took a lot more time and care in removing the salvageable material using just hammers and pry bars," says Johnson & Galyon's Project Manager Chad Brewster. To remove the original cut nails from the flooring, Brewster's crew employed two methods: They either tore the nail out with pliers or cut off the shank. After the flooring was torn out, Johnson & Galyon tore out subfloors in about half the rooms so that utility workers could install new wire conduits, junction boxes and HVAC vents underneath. In the other half of the rooms, utilities were installed in the walls, so Praters only needed to reinforce the subfloors. For the entire year that Prater and his team were on the project, more than 50 other trades were working around them. Throughout it all, Prater took hundreds of photos and detailed notes in order to document conditions in his work areas.
Originally, project architects figured only half of the wood flooring in Ayres Hall would be salvaged; however, in the end it turned out that about three-quarters of it could be saved. A complication was discovering that the original beech flooring actually comprised a variety of widths-while Prater and his team was sorting through the usable material, they realized some was 2¼ inches wide, while other material was 2 inches or even 1½ inches. After all the material was sorted and the subfloors prepared, Praters re-installed all the original material on the main floors and installed 7,000 square feet of beech in the tower; all of the floors were then sanded, stained and finished. Last, the company installed 12,000 square feet of prefinished engineered ash in the basement.
On Ayres Hall's fourth floor, Praters Inc. installed new unfinished solid beech material to match original flooring on floors one through three.Photo by Nick Meyers
Prater says he wasn't surprised that approximately three quarters of the decades-old original material was salvageable given its institutional upkeep, which involves decades of militant wax and polyurethane finish application. Plus, he says wear layers are usually still thick due to tight school budgets that don't allow for frequent re-sanding. As far as Prater could tell, none of the floors in Ayres Hall had been sanded and finished after they were originally installed.
The architects, construction crews and subcontractors involved in the Ayres Hall renovation were able to salvage many of the building's original components, including structural elements, roofing, wood doors and trim, and, of course, the nearly 100-year-old wood flooring. In total, about 692 tons of waste was diverted from landfills through salvaging, and today UT officials are in the process of having the building LEED-certified. Prater is proud to have been involved in this undertaking. "This project was tremendous since I had spent so much time in that building as a student," he says. "Watching it transform from the place that I remember to a new-millennium building with the same façade makes it the best renovation project I've ever seen, and we've been on a lot of them." Surely, Brown Ayres would be proud, too.
Project Details
Architects: Weeks Ambrose McDonald Inc. (Knoxville, Tenn.) and Ross/Fowler (Knoxville)
General contractor: Johnson & Galyon Construction (Knoxville)
Wood flooring contractor: Praters Inc. (Chattanooga, Tenn.)