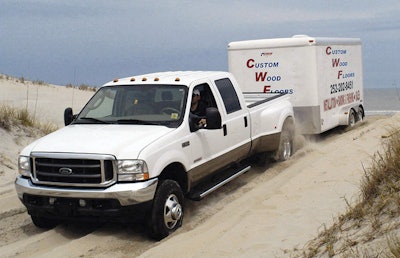
Almost any wood flooring contractor will tell you that he doesn't have an easy job. And, it's true. Installing, sanding and finishing hardwood floors is an intensely physical job that involves carrying burdensome loads, lifting heavy machinery and dealing with aches and pains at the end of the day.
The contractors in this article understand all too well the physical rigors of being a wood flooring contractor. Not only do they install, sand and finish hardwood floors just like any other contractor, but sometimes they have to lug themselves and their equipment to the job by boat, ferry, snowmobile or even seaplane. The benefits of their extra hassles? Being able to experience sights off the beaten path. Working in areas many consider vacation wonderlands. Seeing creatures from orcas to grizzly bears as part of their commute. Read on to see how these contractors manage to do their jobs in extreme conditions.
Beaching It
Contractor Josh Frink of Custom Wood Floors, located in North Carolina's Outer Banks in Kill Devil Hills, N.C., calls the surrounding area "just a beautiful paradise." He and his wife first saw the region while on vacation in 1996, and they started looking for property immediately. While the area may be paradise, it provides some interesting challenges for a wood flooring contractor.
More than 100 miles long and up to a mile wide, the Outer Banks are a tourism hot spot, with many rental homes for beach vacationers. The local construction business is booming, which translates into lots of wood flooring jobs. A fair amount of Frink's business is in a beach community called Corova, which is located as many as 20 miles past all paved roads. Getting to the multi-million-dollar homes involves driving up over the sand dunes, down the beach, and then back up over the sand dunes to the job sites.
"You've got to have a 4-by-4; that's not even a question," Frink says. Before heading onto the beach, the vehicle's tires have to be deflated to about 15 to 20 pounds per tire, making them more balloon-like, he says. If not, the truck simply sinks into the sand. Slowing down or stopping are also hazards that can cause a truck to sink, especially when it's loaded down with wood flooring bundles and equipment.
Having four-wheel drive isn't the only thing to worry about when driving on the beach. Frink must time his commute to job sites to coincide with low tide, which changes by a half hour every day. "You print out the tide charts and pretty much schedule your life around the tides," Frink says.
Driving his work truck and trailer down the beach can be a nerve-wracking experience, he admits. "It's pretty hairy, because you have $70,000 or $80,000 of equipment, and if you make a mistake, it's all in the ocean. I've come close a few times," Frink says. Even for drivers used to the conditions, getting stuck is inevitable. Frink estimates that he gets mired in the sand about once a week, and he pulls somebody else out of the beach at least once a day. "There are lots of tourists up here who have no idea what they're doing; they try to get up there in little Honda Accords and just bury themselves," he says. Experienced drivers, he says, don't go into the area without shovels, tow ropes and water.
Once at the job site, heavy lifting is required. Due to the flood plain, all houses in the area must be built at least 11 feet off the ground, so all equipment and materials must be carried up at least that high, and oftentimes more. "You have the great room and kitchen on the top floor, and of course that's where everybody wants their wood floor; you have to lug your wood and all your equipment all the way up," he says. Not contaminating the job site with sand is tricky, Frink says, explaining that he keeps a vacuum at the door to clean off all people and equipment entering the home.
Although the jobs are merely feet from the ocean, Frink says the relatively stable moisture levels translate into few moisture problems, although a few jobs that were literally on piers over the water made him a little nervous. By using "serious vapor barriers," he hasn't had any problems with those floors, he says.
The area's notorious nor'easters do sometimes wreak moisture havoc, however. Besides making access to the beach impossible, they can pelt rain at 80 miles an hour for as long as a week. Even with high-quality construction and windows, there are frequent leaks that allow water to make its way onto the wood floors. "Just about every new installation I do, I have to come back and fix two or three spots, and on several jobs I've had to pull up the whole floor," Frink says. The weather can get so violent, he says, that sometimes houses simply slide into the ocean.
Due to the extra complications of handling jobs in the area, Frink typically charges at least 10 percent more for these jobs. While the commute is risky and the labor can be intense, the work isn't without its rewards. The area is beautiful, and Frink sees everything from wild horses to beached whales to shipwrecks on his way to work. Frink and his workers keep their surfboards in the back of the truck so they can catch some waves during a break, or sometimes sun themselves on the scenic top decks of the beach homes while they wait for finish to dry. The sun and surf seem to be the right combination for an aching back.
There's nothing unusual about transporting sanding equipment by boat at Rishe's Custom Hardwood Flooring in New York's 1,000 Islands region.
1,000 Islands … or More
Roughly 600 miles north, Stuart Rishe of Rishe's Custom Hardwood Flooring in Ogdensburg, N.Y., also deals with water in his day-to-day work life, but this water is a little different. His work area includes the 1,000 Islands area of the St. Lawrence River, a scenic area that actually includes 1,864 islands. "Some islands have only one home on them and some have hundreds, but there are all kinds of contractors here whose livelihood is just working on the islands," Rishe says, adding that it's a "very wealthy area." The clientele has been a good fit for the company, as Rishe has continually upgraded his skills to include borders, medallions and other high-end work.
The area includes both permanent homes and vacation homes, and while some major islands have bridges connecting them, others are accessible only by boat. "Usually at the end of March, the icebreaker goes up and opens up the channel. Once the ice clears out, we can go in and out in boats pretty much the first week of April and right through the end of November," Rishe says. The weather runs the gamut in this area. "It gets very cold. In March and April, the wind is just bitter coming out of Canada," he says, adding that the weather also can be beautiful.
Arranging for boat transportation can vary depending on the job. Rishe works with a network of general contractors, most of which have four or five boats that help transport their subs to the islands. When going to a job by boat, Rishe typically drives a half hour north, then loads his equipment at the dock. Most islands are then only a few minutes away. Rishe has one high-end client who simply offers the use of his own boats for the crew's needs during the project.
When a job requires a major installation, materials must be transported by barge, which often is handled by the job's general contractor. On islands without power, a generator also is a necessity, and again, that's usually the responsibility of the general contractor if the job has one-Rishe typically writes the requirement into his estimates. A generator of at least 15,000 watts is required to be able to run sanding machines. "Obviously, you have to be careful running off a generator that you don't burn up your sanders," Rishe says. He uses less powerful generators to run smaller equipment when necessary.
Rishe is careful when dealing with the job-site environmental conditions. Moisture can be an issue, especially because radiant heat is prevalent, and wood floors on the second story in boat houses are not uncommon. When he anticipates moisture issues, Rishe doesn't stop at using moisture barriers. He frequently spreads out the flooring on sawhorses and sprays the bottoms of the boards with polyurethane before installation, a technique he says helps slow moisture migration and prevent cupping.
Rishe also is careful to educate the customer about which products are appropriate for areas with the potential for drastic moisture swings. He recommends quartersawn material or engineered products in those areas, and he's particular about which species here commends. "We steer people away from things like beech that are pretty unstable," he says. "We give them a few options to pick from." In a region that's more water than land, that's sage advice.
Wild Canada
On the opposite side of the continent is another area rife with islands. Situated in Duncan, British Columbia, on Vancouver Island, Mastercraft Flooring Ltd. does business in "one of the most beautiful places in Canada," according to company President Nick Kulhawy. Its business consists not only of work on the main island, but also the innumerable islands in the famous region. Some of the islands have ferry service, making it easy for a hardwood flooring crew to get the work trucks to the job site. In other cases, a boat or a seaplane are the only options for getting where they need to be. "You put all your materials on a boat, and away you go," Kulhawy says. "It's adventurous. One of the nice things about it is, it's work, but it's almost like a holiday, if you enjoy nature and the wilderness." Orcas, gray whales and dolphins are frequent company during boat rides on the way to work.
The region's temperate climate means that crews can take boats to the job sites year-round, although it does get chilly and damp in winter. Kulhawy uses his own boats, or charters a barge or a water taxi when necessary. Occasionally, his crews need to travel by seaplane on the Harbor Air airline. "They're the feet of the north up here; wherever you want to go, you just charter it, and they just drop you in," Kulhawy says. "We have a lot of airstrip around here: water everywhere."
Not surprisingly, loading and unloading equipment and materials can be a chore. Kulhawy says he's lost small tools and plenty of cell phones-"you see its inking down there and you just have to wave goodbye to it"-during the loading and unloading process, but thankfully never a sanding machine. Once back on land, crews might have to maneuver bundles of wood up a steep staircase hanging off a cliff or trudge through the woods. "If the packing goes quite a distance, we'll load wood up on two-wheeled dollies," Kulhawy says.
With the complicated logistics of getting to such job sites, Kulhawy says that prefinished flooring is becoming increasingly popular, offering the dual benefits of a shorter time on the site as well as not requiring the transport of sanding machines by boat or air.
While the majority of Mastercraft's work is on the islands, Kulhawy says that some of the company's most interesting jobs were completed when the company also had a location in Calgary. Back then, the company handled jobs at schools in northern Manitoba. "It's very interesting getting into some of those areas," Kulhawy says. "A lot of those reserves are quite far north, and the only way to get in is either by water, winter ice road or by air." The region is covered with muskeg, a kind of bog, which makes it impossible to drive on until the ground freezes. Once winter hits, "winter roads" are created, which are used mainly by tractor trains. Ice bridges over small creeks and rivers are formed by stringing timbers across the water, then flooding the timbers with water to create a stronger bridge.
For jobs in such remote locations, bidding can be complicated. "You take the worst-case scenario and base it on that, and hope you can do it for the lesser amount," Kulhawy says. The most expensive scenario included having to fly crews and supplies in by plane, while the least expensive would be transporting everything to the job site on the winter roads. If flying were the only option, the crew would fly into the closest airport. Then, a boat, canoe, snowmobile or helicopter were sometimes necessary to get to the actual job site.
In such situations, ice breakup was a deciding factor for transportation. Kulhawy remembers one site where he was able to go to the job site and return by snowmobile. "But when the installers were finished, they had to come out by helicopter, because the ice was broken," he recalls. "Weather dictates it, and you have to go along with it; you can't change the weather," Kulhawy says.
Alaskan Adventures
Rolling with the punches in remote regions is something Bill Keith understands well. Now the owner/operator of Arctic Flooring in Anchorage, Alaska, Keith spent the first 10 years of his hardwood flooring career during the late '60s and early '70s working for a company that installed, sanded and finished wood floors in the remote interior of Alaska, mostly for "bush schools."
For those jobs, flooring was sent in ahead of time on a barge, he says. Crews would then be sent to the nearest major airport by commercial plane, usually with about 1,000 pounds of equipment crated for the trip. "You would get there, break the crates apart and break the machines apart so you could get them into a small plane, and that's where the fun started," Keith says. "You would fly into a village in a Cessna 185 and wonder why the pilot of the plane had hip boots on. You would get out on this muddy strip and wonder, 'How is my equipment going to survive this ordeal?'" Oftentimes, the equipment would need to be taken down to a beach, where it would then be loaded onto boats to travel upriver to the actual job site. In wintertime, the Cessnas would land on ice instead of mud, and instead of getting into a boat, everything was loaded onto a sled to be pulled behind a snowmobile, he says.
Crews tried to take only the necessities, and would frequently find themselves having to make do with what they had on site. "There were little, stupid things you would forget, like a dust bag for the machines, so sometimes you would have to improvise with pillowcases," he says. "They were small things you don't think about when you're in town, because they're always in the truck." If something essential was missing, the crew would have to find a phone in the village. "You would call and put your order in, and who knows when it would show up-whenever they could get somebody to fly it into you," he recalls.
With such conditions, the crews did the best they could to deal with moisture, which would go through extremes from summer to winter, when temperatures would fall well below zero. Having the heat running during the winter was a prerequisite, but that was about the extent of the job-site control. "You never knew how the material would be stored; that was always a big issue," Keith recalls. "We always hoped for an install in the spring, when it would be optimum conditions, but you just kind of had to go with the flow."
Crews for such jobs were small, because accommodations were scant. When a school was being built, camps of 8-by-8-foot trailers were created so the construction crews would have a place to sleep. Jobs could last from two weeks to a month, depending on the size. Once the job was done, the crew would be flown out, and the equipment would be sent out when there was an opportunity.
Although he never had any close calls with his safety during the thousands of miles of flying through the bush, the extreme conditions eventually drove Keith to start up his own company in the relative normalcy of Anchorage. Today, he occasionally has to spend a few nights or a week away from home for a remote job, but now they're sites he can drive to, albeit sometimes with four-wheel drive or his two-wheel drive van with chains on the tires.
Despite the darkness and severe winters, construction in Anchorage goes on all winter long-"I'm constantly thanking my contractors for building year-round," Keith says. While only five or six hours of daylight during the winter can be trying mentally, in the summer there is daylight nearly 24 hours a day. "You definitely have more energy up here in the summertime," Keith says. "It's not unusual for us to be on the job at eight or nine at night, only because the sun is still shining."
Freight charges on oak flooring sent to Alaska typically run about 70 cents a square foot. Until about three years ago, when a hardwood distributor opened in Anchorage, Keith had to order from a distributor in Seattle, which meant that supplies would be shipped out twice a week for a week-long barge ride up the coast. "Usually what we would do is order a month ahead of time to get it in the shop to get it acclimated; I keep our shop real dry," Keith explains. "Coming from Seattle to Anchorage, there's a real transition period."
Now that there's a distributor in town, Keith doesn't have to plan as far out, but he still tries to address moisture problems. "It's an ongoing education with customers about keeping constant humidity levels, because when it does get 15 or 20 below, it's hard to keep 35 percent humidity in your house, even with the best windows," he says.
For Keith, such battles are all relative. He knows that struggling to get homeowners to maintain relative humidity is easy compared with struggling to get a sanding machine across a swampy runway onto a boat in the middle of nowhere in the Alaskan wilds.
Surf's up at Custom Wood Floors in North Carolina's scenic Outer Banks.
Island Hopping
Most people don't think of Michigan as being too exotic, but in Cedarville, Mich., located in the state's Upper Peninsula, Northern Floor Finishing does business in a way that's outside the norm. "Instead of getting in my care very day to check a job, I get in my boat-that's the fun part of it," says Chris Brumleve, president/owner. "There's a group of about 38 islands out here, and none are really bridged, so we generally have to take a boat in the summer and a snowmobile in the winter." The logistics of getting materials to the job site usually adds about 20 percent to the cost of the jobs, Brumleve says.
While work on those islands in the winter is limited, it does continue. In some cases, the older summer homes are not even winterized. "Those floors are a little cold to be refinishing," Brumleve explains. "Sometimes we'll install the flooring and finish it in the springtime when it warms up." The company has a trailer that can be pulled with a snowmobile, and it can carry about 100 square feet of flooring at a time.
Newer homes typically have electric heat, but the older homes without heat can be brisk on a northern Michigan winter morning. "Some now have electric heat or a fireplace or a wood stove, but it gets a little chilly in the morning," he says. Work outside his immediate area in places such as Mackinac Island and in Sault Ste. Marie helps fill in the winter schedule.
Sometimes, work on the islands is simply not an option. "You've got a period in the spring when the ice is thawing and the fall when the ice is forming, and you can't get to the islands either of those times," Brumleve explains. The freeze and thaw can each last as long as three or four weeks. During the spring thaw, wisely, "we try to leave town for a little bit," he says.
During the summer months, Northern Floor Finishing shares a small fleet of boats, including three 16-foot aluminum boats, a 20-foot pontoon and a 26-foot boat, with Brumleve's general contracting business. Employees must be boat-savvy. "They've all got to know how to drive a boat; that's basically a requirement of applying," Brumleve says. "It helps if you can swim, too," he laughs.
Equipment and materials are loaded on a ramp in town, and once on site, are manually carried to the job. "It can be somewhat time-consuming and backbreaking carrying that equipment around," he says.
Not surprisingly, Brumleve keeps moisture issues in mind. Some of the older island homes, which can be 80 years old or more and were built on piers without a foundation, actually have fewer moisture problems than some newer homes, which all have a foundation. The company uses moisture meters, but with drastic swings from high humidity to extreme low-humidity conditions in the summer, "it's kind of a crap shoot," Brumleve says. "You've got to try to balance out the seasons and the moisture you're dealing with at that time," he explains, adding that if they're installing in the winter, for example, they'll leave extra expansion in the floor.
The challenging job-site conditions area small trade-off for being able to work in such a beautiful area. Brumleve's grandparents owned a home in the islands that was built in the '20s, and working on the water "comes kind of natural to me," he says. Like the other contractors in this story who have their own unique environments, Brumleve wouldn't have it any other way.
Job-Site SurpriseA wood flooring job on an island in a resort area outside Anchorage proved to be more than Bill Keith of Arctic Flooring Co. bargained for-while he was doing the job, a forest fire burned the surrounding area (top) and jumped to the island where he was working. The resort where his work van was parked was a charred ruin (bottom), but the van escaped with only melted plastic parts. Keith managed to save the cabin where he was working by soaking the roof with water from sprinklers. |