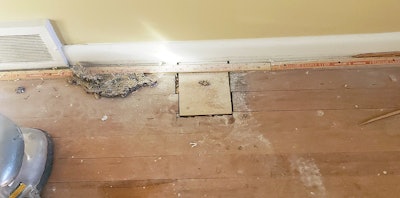
I still do some installations, but the majority of my business here in Michigan is sanding existing wood floors. Here are some things I always do long before I bring in my sanding equipment.
1) Discover what’s underneath
A lot of our work is sanding floors that have been under carpeting. On estimates, I use my Leatherman to pull up carpeting in corners to see the wood and determine if it’s red or white oak (here, it’s always one or the other). Then I tuck the carpeting back in and let them know there are no guarantees that the entire wood floor looks like what we just saw. If I have access, I also go below the floor to check the subfloor and joists.
2) Is there enough to sand?
I try to find an air register where I can see the wear layer on the existing floor; there has to be a solid 1/8 inch-plus to be able to sand. On an old floor, seeing shiners doesn’t necessarily mean there isn’t enough wear layer—oftentimes those didn’t set all the way.
3) Figure out the finish
Most existing finishes don’t concern me—but aluminum oxide on a prefinished floor is a completely different beast, and UV-cured urethane can also be difficult. Those finishes will require extra time and money. We use a Diamabrush on the buffer to break the top of the finish off, then start sanding with the big machine. You can also use newer abrasives that are specifically designed for those floors, but they are expensive, so you need to bid that into the job. When in doubt, I bid for the worst-case scenario.
4) Where’s the power?
During the estimate, I determine exactly where I’ll be able to get power safely and check to see if there are any tricky issues with access and getting equipment to the site.
5) Discuss shoe molding
We like to remove and replace shoe moldings, but that’s something the client has to budget for—if not, we’ll sand up to them.
6) Leave the contract open
There could be stains, damaged flooring or missing flooring under carpeting. I’m on a job now where toothing in repairs added $3,800 to the job. Are the clients willing to pay for repairs? Will they let you use a stain color that will disguise stains that don’t sand out? If clients don’t have the budget, some contractors take the position of, “That’s what they’re paying for, I’ll give them what they want,” but how many people walk into that house down the road and see the floor you did? I always bid extra time into my jobs so I can make it right.