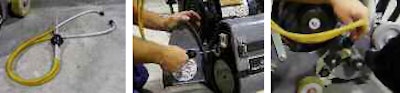
Wax On, Wax Off
I have a customer with a 50-year old oak floor that has always been waxed. She wants me to resand it and coat it with oil-based finish. Is that possible?
John Bast III, president of Tampa, Fla.-based Florida Hardwood Floor Supplies, answers:
Yes, it usually is. First, you have to do a thorough sanding with all the required grits, which is typically a three-cut process. You need to be thorough not only with the big machine, but also pay careful attention while you're edging. Any areas that have to be sanded by hand also must be done carefully.
Sanding heats the floor, which liquefies some of the wax that might be remaining between the boards or in the pores of the wood, driving it to the surface. That's why I recommend sanding the floor, letting it cool overnight and then coming back the next morning to screen and coat the floor. Grain-filling the floor between the medium and fine cut may also help.
If the wax isn't completely removed, several things can happen. You can get lines between the joints of the boards— along the sides and also at the end joints—from wax that was in that space. Wax remaining in the surface of the wood can cause alligatoring and peeling of the finish, also. Opengrained woods, such as pine and oak (typically the species used for the old waxed floors), are more likely to have problems than a tight-grained floor like Brazilian cherry.
As with any recoat job, it's a great idea to test an area before you do the whole floor and also to inform the client up front that problems from the original finish or other contaminants are a possibility. Wax is obviously a phenomenal contaminant, but if you're careful, you can usually resand a previously waxed floor successfully.
Expanding on Expansion
My new employee installed a solid 3/4 -inch prefinished floor yesterday and only left about 1/4 -inch expansion space at the wall. Will this be a problem?
Rusty Swindoll, assistant director of technical training at the NWFA, answers:
For solid wood floors, we recommend leaving expansion at the walls as wide as the flooring is thick—in this case, 3/4 inch. You'll want to check with the manufacturer of the flooring for that specific product's recommendation; not all manufacturers of solid products necessarily require that much expansion.
The reason for expansion space is to prevent the flooring from pushing walls out of place in the event that there are extreme moisture conditions on the job and the floor cups and buckles. Expansion space doesn't prevent cupping. If the flooring was acclimated to the job site and the temperature and humidity in the house never change, the floor probably won't have a problem—but if the floor floods, the wood floor can possibly move the walls and even shift the sill plates, causing structural damage to the house. If there is 3/4 -inch expansion, on the other hand, and there's a flood, by the time the floor moves 3/4 inch, the fasteners will have released and the pressure on the floor is released upward instead of pushing out the walls.
To be safe, one way to leave expansion space after the fact is to undercut the sheetrock to the level of the floor. To do this, you can use any number of tools—anything from a razor knife to an undercut saw like a jamb saw (beware of dust when using a jamb saw) to the small electric handsaws that are now available for flush-cutting applications. You can even use a reciprocating saw as long as you're careful not to cut into the joists; it can be especially useful because it cuts right through any drywall screws. A high-speed rotary tool would also do the job.
Playing it safe is always the best option. If you don't leave the expansion space required by the manufacturer and you end up with an expansion problem, you may not be covered by your warranty.
Comparing Change
What causes more change in the dimension of wood flooring, temperature or humidity?
John Christopherson, owner at Alaska Wholesale Hardwoods in Anchorage, Alaska, answers:
Humidity. At 50 percent humidity, the moisture content (MC) of hardwood will equalize at about 9.5 percent when the temperature is stabilized at 50 degrees Fahrenheit. If you change the temperature to 80 degrees, the hardwood will stabilize at around 9.1 percent MC. That is less than half a percent lower MC for an increase in temperature of 30 degrees. Switch that to a 30 percent humidity change and the wood will equalize at about 3 percent MC less than before. That would cause a 3-inch plainsawn red oak board to shrink about 1/32 inch.
Trick of the Trade: Listen Up
By Wayne Lee
Most chatter is caused by a bad drum, but if it isn't, it can be hard to figure out what the culprit is. This device can help you figure out if it's another suspect— bad bearings. The specialized stethoscope can be bought at any auto parts supply shop. Simply touch the end of the device to the relevant parts—if you hear a regular knocking noise while the machine is running, you know the bearing is bad.