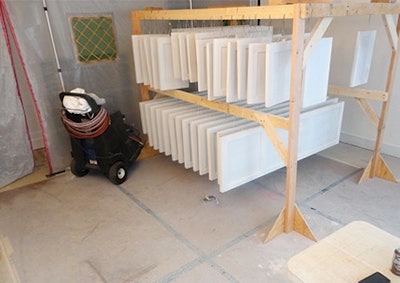
One of the biggest drawbacks to wood floor refinishing is our place in the sequence of building trade workers on a work site: dead last. We come behind everyone else when there is little time, patience or money to go around. At the core of the problem are turf wars, since the areas we need to work on are the same areas others need to tread on. In an effort to create harmony on the job site and reduce friction, contractors and homeowners will delay work on the floors until the very end. That concept may be good in theory, but, in reality, it often deprives us of the time needed to do our work and creates even greater chaos for us when we are finally allowed on-site.
Newer floor protection products have allowed us to completely change where we come in the long line of subcontractors.
Some time back, a contractor friend of mine and I asked some "what if" questions and came up with options that have changed the way we do business, and we have never looked back. On my historic restoration projects, our wood floor work now precedes the stripping of walls and ceilings and window restoration. We've been doing this for years now, and to say it works well is an understatement. You may want to consider doing the same.
The reason we can do this is that over the last 10 years, we have seen a quantum leap in temporary protective products that can minimize the No. 1 reason for putting us at the end of the line: premature damage to a freshly finished floor. For decades, the building trades had to rely on red rosin or builders paper to protect surfaces, and they did a marginal job at best.
Next-generation floor protection
The new generation of products provides a variety of materials that are typically made from recycled materials and address our needs. I think it would be most helpful to tell you about the specific products I know of and have used, although there certainly may be more (I'd like to hear about any you know of—feel free to leave a comment below).
Instead of the 9-mil-thick red rosin paper, we now have a 45–50-mil-thick paper that rolls out and actually lies flat so seams can be taped. (Two of the most popular in that category I am aware of are Ram Board and Flexboard by Protective Products.) They provide additional protection from spillage and also claim to allow vapors to pass through them if vapor is present in the substrate.
The floors in the master bedroom of a $2 million remodeling project after being sanded, stained and finished.
Once the floors were wrapped and protected, the master bedroom became a spray booth for cabinetry and trim items.
There are also softer products that are more pliable—but not at the expense of protection. A favorite of mine is Albert Floorotex; its bright blue surface is a thin polyester attached to a white nonwoven material made from recycled plastic. It is lightweight, and the bottom has an adhesive that keeps it in place when put down, which is particularly advantageous for stair treads. The product allows for moisture vapor to pass through, although the polyester keeps spills out. Somewhat similar is Dura Runner Plus with its felt-like surface on top of a waterproof backing; the backing helps prevent slippage but doesn't have adhesion.
If I really want to up the protection ante, I will put down Masonite or hardboard over these products. It may sound extreme, but I've never regretted going overboard in this category.
A few precautions to keep in mind
As with all products, make sure you read the technical specs. Finishes should be well into the curing process (it's best to check with the manufacturer about how soon they can be covered). (Note from the editor: See page 32 to read about what happens when a floor is covered too soon.) Also, avoid areas of intense sunlight to avoid color differences in the floor from UV damage.
Also, as you would expect, these items do add to a project's cost, but all of these products can be removed and reused in other areas or on other projects, which really helps defray their cost. Simply put, the cost and the labor needed to install them should never be an argument to not use them.
Of course, none of this amounts to much if we don't have concrete evidence of these types of products actually performing their tasks. I've had many opportunities to use them, and I'll give you visual proof of their effectiveness.
Example: a $2 million restoration
This was a $2.3 million remodeling project. The contractor was an old friend of mine, and we knew in advance we could not put the floor work at the end. All of our wood floor finish work took place as soon as the drywall and plaster were completed. The floors were sanded and stained, and three coats of finish applied. The finish was allowed to cure for four days and then totally covered. It was understood that when the covering was removed, we would do a fourth application of finish.
The covering on the floor allowed for other work to continue. The master bedroom was turned into a spray booth for custom finishing cabinetry. The family room became a storage area for cabinets before they were installed, paint supplies and other equipment. A bedroom was used to prefinish the new stair treads being installed from the basement all the way to the second floor. All of this was on top of freshly finished wood floors.
When the project was completed, the contractor was firmly convinced he could never have achieved such high-quality results if the floor work had been put at the end of the project. He needed additional time, and he got it. He's never gone back to the old scheduling sequence since that project.
The floors in Henry and Clara Ford's billiard room fully restored and ready to be wrapped.
Once protected, the billiard room provided a workshop for stripping doors and storage space for building materials.
Example: Henry and Clara Ford's Fair Lane
This is my current restoration project in Dearborn, Mich., of Henry and Clara Ford's house known as Fair Lane. After we were selected for the restoration of the wood floors, we had the pre-construction meeting with all the other trades, and the question came up about sequencing. I patiently waited my turn and then told them I felt like the wood floor restoration work should precede all other trades. I expected pushback and got it, but I went prepared. I took my iPad and started showing the photos of restored floors on other projects and how they were protected, along with accompanying testimonials. It took a bit to sink in, but the decision was made to put us first in the line.
We completed restoration of the music room in August 2016, and the floors were immediately covered. Following our work, the walls in the music room were chemically stripped of paint to reveal the solid walnut paneling. The windows in the room were removed and replaced, and a lot of electrical work was completed.
After we completed our restoration work in the billiard room in March, those floors were covered. The photos I took in October (shown above) show the room is now used to store building materials and to strip the painted French doors. All of this over fully restored wood floors! The principals with the Historic Ford Estates overseeing the work are elated.
Discovering flexibility in planning and execution
They discovered what I already knew: Temporary protection products give flexibility in planning and executing a project. They open doors you never thought existed and provide options that can exceed everybody's expectations. On every project where we've flipped the sequence, everyone involved has said they would never go back to the older, outdated method of putting our trade last. For me, it's been a game-changer.
Temporary protection products are a growing field, so be on the lookout for new products beyond those I am aware of and mentioned in this article. You might find that, like me, you never go to the end of the line again.
Other WFB articles by Michael Purser:
The Low-Hanging Fruit: Old Floor Refinishing
The Floor Listener: Wood Floors Have Stories to Tell
Take Caution When Doing Restoration Work
The Missing Link: Are You Skipping a Step in Your Recoats?
What the Wood Flooring Industry Can Learn From the Tower of Babel