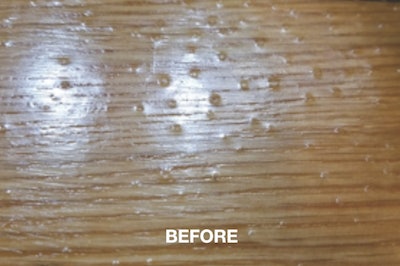
Top factors in success
Problems can arise when manufacturers’ recommendations are not followed. Job-site conditions are very important, as temperature, humidity and air flow are all important contributors to success. Hot spots on the floor from the sun or heating elements and excess air movement from refrigerators or HVAC systems can all cause problems. Clean, uncontaminated applicators and equipment are also vital to the proper application of your finish coats.
Does ‘thin to win’ work?
Often, when a contractor calls me with complaints about their coatings, I find the proper spread rate has not been achieved—sometimes on purpose! They tell me, “I was taught to lay thin coats. ‘Thin to win,’ my old boss used to say!” Because oil-based coatings have a longer open time than water-based coatings, folks would often get away with “thin to win.” However, if water-based coatings do not get the necessary “open” or “wet edge time” to allow the flow and levelling agents, as well as the defoamers to work, problems can occur.
Recommended spread rates and the math involved…
Let’s walk through some examples with spread rates.
At our company, most of our PoloPlaz finishes are designed to be applied at the spread rate of 500 square feet per gallon. However, for the sake of easy math, let us talk about Endure (our two-part water-based poly) that applies at a 400 square feet per gallon spread rate. Here are the relevant facts about Endure:
- One coat of Endure applied at 400 square feet per gallon is 4 mils thick when wet.
- Endure is 50% solids so that same coat has a dry film build of 2 mils (4 x 0.5 = 2).
- In normal conditions, this coat has approximately 10–15 minutes of wet edge/open time.
- Result: This film has enough time to flow and level out as intended.
Now if we apply a coat at say 600 square feet per gallon the math changes somewhat:
- One coat of Endure applied at 600 feet per gallon is 2.66 mils wet.
- Dry film build is therefore 1.33 mils (2.66 x 0.5 = 1.3 mils).
- In normal conditions, this coat has approximately 5–7 minutes of wet edge/open time.
- This film does not have enough time to flow and level out as intended. The defoamers and leveling agents did not get the opportunity to do their job—time ran out!
After all your hard physical work of sanding a wood floor, you deserve a completed floor that looks the way you want and generates referrals from customers who love your work. And, of course, you deserve to get paid and call it a job well-done. It is all possible when you follow the manufacturers’ recommended guidelines for application. You worked so hard to sand it well—finish it well, too, so your customers will be, well ... floored!