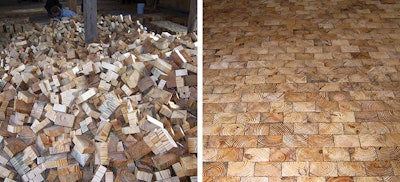
End-grain flooring is popular today, but this flooring also has an interesting and remarkable history. End-grain blocks were first used for street paving; several historical streets in the United States remain that are paved with end-grain wood blocks. You can Google "wood paver alley" for some interesting history!
Valued for their durability, sound and energy absorption qualities, as well as ease of removing and replacing, end-grain blocks became the industrial wood flooring of choice in the early 1900s for heavy industrial applications in plants such as US Steel, General Electric, Caterpillar, Alcoa, GM, Ford, and so many others. Today, the floors in those industrial facilities are still being serviced with replacement blocks, adhesives and coatings.
In today's market, end grain is also being installed everywhere from private homes to commercial locations such as theaters and museums. Dozens of species are available, and modern end grain is available in individual blocks, on engineered planks, end grain in strips, on cork backed panels, and with mesh backing.
There are no published grading rules for end-grain blocks, and many times the more character in a block, i.e. knots, checks, "blue-ing," etc., the more interesting and desirable they may be. In fact, making end-grain blocks from the worst grade of lumber may be the best use of the raw material. If required, however, blocks can be provided check-free, pith-free, sap-free and knot-free.
Typical end-grain thickness is ¾ inch, but some species perform well as thin as ½ inch, and we've made blocks from ⅜ to 4 inch in thickness. As a general rule, there's a correlation between face size and thickness. The larger the face size, the thicker the block should be. At one of the GE facilities we service, they use two layers of 4-inch depth blocks—the impact wear pulverizes the end grain but saves the metal objects being dropped, and when the top layer is crushed, it is removed and a new top layer applied.
End-grain blocks should be mixed up and acclimated before installation; these pine blocks are at a Connecticut school.
When industrial blocks arrive on a job site they should be removed from their packaging and acclimated before installation. Commercial blocks should also be removed from their packaging once they are on site, and they should be mixed and scattered to avoid clustering of the same blocks cut from the same log. The blocks must be acclimated in loose piles to normal long-term conditions. The installer should be advised of the humidity conditions planned for occupancy and then make every effort to acclimate them to the average level of humidity. As with any wood flooring job, the installer should record the moisture content of the wood upon arrival and before installation. Note that when using a pin meter on end grain, the pins should be inserted into the sides of the block, not into the end grain.
When gluing end grain, it is extremely important to use urethane adhesives for installation, as water-based adhesives can have an adverse effect on block performance.
There are several format options. Some species are available on engineered planks, many are on cork panels, several have mesh backing, some are in strips, and, of course, individual blocks. Blocks can be made from both new or reclaimed logs or cants. Blocks can be installed snug against each other or spaced apart for a more grouted joint appearance. Small voids between blocks can be filled with a paste, usually made from the sanding dust mixed with the chosen finish. For larger voids, many times we suggest using granulated cork, perhaps topped off with paste filler to hide the granules.
RELATED: End-Grain Floors Take Root at the Bill & Melinda Gates Foundation
Some end grain formats are available prefinished. For the products requiring sanding and finishing in place, the sanding and finishing products and procedures should follow a routine procedure, although it may be necessary to start with a lower sanding grit than you normally would with conventional hardwood. We always recommend oil finishes for end grain, which better help stabilize the blocks. Of course, urethane finishes can also be applied, but keep in mind that too much urethane on the surface can cause panelization and shrinkage gaps, just as it can with conventional hardwood.
Again, there are no general industry guidelines for end-grain installations, so be sure to follow the instructions/specifications provided by your end grain block manufacturer every step of the way. And remember, the art is in the installation!
How much does end block cost?A frequently asked question is: "How much is a wood block floor?" That's like asking an automobile dealer, "How much is a car?" We supply close to 50 species, and orders range from 100 square feet in a home to 100,000 square feet for an architect. The lowest-cost product is generally a pine block; on the other end of the spectrum there are products such as ½-inch-depth 3-by-3-inch end grain cherry that can be ordered sap-free and FSC-certified.—N.K |