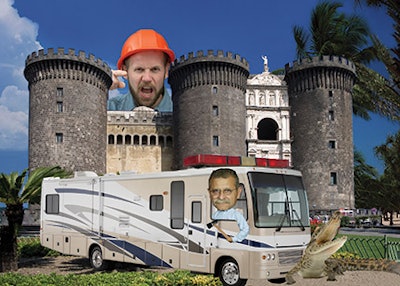
We are going to talk about difficult job-site conditions in this article, so I'm going to tell you a true story: a nightmare, just before Christmas. If there is anything left that didn't happen on this job, we will discuss it later.
This "once upon a time" began in the early summer of 2005 with an old-money family from New England. A winter "cottage," reminiscent of their ancestral home in Ireland, was to be built on a finger of land in Naples, Fla., that is surrounded by the inlets, lakes and waterways attached to the tranquil Gulf of Mexico. In my mind, I pictured adorable thatched-roof dwellings surrounded by primal woods.
I drove to the job site to look over the flooring before the installation began and to meet with the principals involved. While driving through the winding streets of this exclusive neighborhood of mansions, I couldn't help but wonder how a cottage would fit in here. All doubts were swept away as I approached an 8,000-square-foot castle swarming with tradesmen of all descriptions. This was no little Irish cottage.
Next, I noticed, with my wood floor man's perspective, that the hole where someday the huge front door would be was currently sheets of plywood. The balconies had more plywood, with holes cut to allow for gigantic flex ductwork from multiple temporary air conditioners to enter the building. The huge package-unit A/C units were perched on scaffolding around the building and looked like blocks of vibrating steel on an oil derrick. Another hair turned gray atop my shell-shocked head.
I finally entered this "cottage" through a maze of scaffolding, air hoses and electrical cords were snaking in every direction, resembling the roots of banyan and cypress trees in the mangrove swamp that reclaimed this land from the sea. The scene was eerily lit by bare bulbs strung out on temporary wiring like some crazy person's attempt at décor. The chorus of at least four languages being shouted over dueling radios made me feel right at home—I've done commercial work before!
Red Flags Flying High
As per my usual request, I wanted to rack out some of the flooring to make sure it was milled well, check the moisture content (MC) of the flooring and the subfloor, and, more importantly, make sure it was the right flooring for the job and met the customers' expectations. The flooring was 4,000 square feet of prefinished 5-by 3/4 -inch ebony, with two 6-foot-round Celtic medallions at either end of a grand hallway leading to the other main areas. The entry and hall were accented by ribbons of santos mahogany downstairs. The upstairs was prefinished santos mahogany bordered with ebony that was to match the custom stairs, which wove their way up to a bridge spanning the grand hall entrance.
Here is where the excrement begins to engage with the air movement device. Let me make a red flag list:
- There were missing windows and doors, as noted earlier, with no attempt at weatherproofing the openings.
- The doors that were hung were invariably left open.
- There were huge A/C units pumping frigid air into a very humid space with no way to control the interior environment.
- The building was on the water, built essentially on a small peninsula.
- The ebony flooring was mismilled, causing large gaps, plus there was trash in the finish and excessive overwood/underwood.
- It took years to get that much ebony together, and we found out that there was no more readily available on this planet.
- The subfloor was "flattened" with a self-leveling lightweight concrete product (3/4 - to 1-inch thick) over which we were supposed to fasten a 3/4 -inch plywood subfloor.
- The stair company couldn't locate enough ebony to make the stairs, so they made them out of santos mahogany and told the designer that "the floor guys can sand and finish everything to match."
- There were marble setters, tile guys, painters, plumbers, electricians and finish carpenters on the site, as well as a stone cutter from Mexico who was carving gargoyles and cherubs into the main fireplace, which was made of giant slabs of sandstone. There were cabinetmakers and a crew installing an ornate metal ceiling. Outside, landscapers had just started planting palms and trees to replace the ones torn out to make space for the house, and the landscapers were yelling at the crew setting the driveway pavers, while another crew worked on building a stone fence and entry gate; each crew chief was giving the other crew chief the international sign for "you are getting in my way." Did I mention the masons, pool guys and roofers? Cops were writing tickets if anyone parked, well, pretty much anywhere.
- The job superintendent was obsessive-compulsive, but the homeowners and the designer were just picky.
- The wood floor person who sold the job was a "friend" who knew that my son and I could "make things right."
- The job was to start in one week. My mustache was by now completely white. OK, only kidding (the mustache was almost all white already).
Trust Your Instincts
There are a couple of ways of looking at a situation like this one: If life gives you lemons, make lemon meringue pie! Or: Sometimes the job you don't do turns out to be the best job you never did! You've got to go with your gut. As it turns out, these homeowners were nice people and eager for my advice, and the designer understood the magnitude of the problem and vowed to help. (The job superintendent just needed mental health care.) Here is what we did to deal with the multitude of challenges and get the job done:
Bad product: First, we brought up the problems with the wood flooring to the parties involved, not the other way around, which gave us instant credibility. Knowing we couldn't get more prefinished ebony, we agreed to sand and finish the entire floor after the installation. This would eliminate the overwood and finish problems, allow us to use slivers to fill the biggest gaps, and also ensure that the stairs would match the floor as to both the height and sheen level. I explained that with the feature strip and medallions, a jobsite finish would be more in keeping with the other high-end work being done in the house. And on a job like this, what's an extra $6 per square foot in the overall scheme of things? We made samples of santos mahogany stained to match the ebony. Upon approval of the sample, we had it signed in two areas and cut it in half, keeping one until the job was over (and the checks cleared).
Bad conditions: Instead of complaining about the job-site conditions, we offered solutions that could work if we all worked together. We got an area roped off with controlled A/C where we cross-stacked all of the wood. We checked the moisture content using both an invasive (pin) meter and a non-invasive (pinless) meter, adjusting for the specific gravity of the different species of wood, and documented it. We rechecked the slab and found it wasn't within 3/16 -inch in a 10foot radius, so we ground down the high spots and filled the low ones. After using a concrete moisture meter to make sure the slab was dry, we installed a vapor retarder and shot the subfloor down using pins long enough to ensure good integrity over the life of the building. We explained to the builder that we could not (and would not) begin to install until the MC of the flooring and the subfloor were within 2 percentage points of each other, as this was a wide plank floor. Further, we got the builder to insulate around the temporary A/C, and to keep the building closed (within reason). We wanted to get the interior environment down to around 45 percent relative humidity at 75 to 80 degrees Fahrenheit; typical for the south Florida climate.
Other trades: Once the subfloor was ready, we begged the other trades to try to keep the subfloor clean and dry, and then we got out of town. Everyone agreed with me that it would be best if we came back when there was less chaos and maybe even electricity in the building. I agreed to a restart date and suggested that for a "bit more" money we could work weekends and start later in the day so everyone would be out of our way. It was chump change for them and easier for us. Last, but not least, we got permission to park my motorhome on the lot, saving the 240-mile round trip across Alligator Alley every day. I would like to end this by saying, "We all lived happily ever after," but this is a true story.
Pulling it Off
The installation of the subfloor and the flooring itself went pretty much like most new construction jobs on a tight schedule. The subfloor installation had to be completed for the trim carpenters to install door jambs, casings and trim, as well as the stair company to begin their installations, so we worked around, beside, next to and over all of the other trades. We learned to cuss in Spanish, Portuguese, Creole and Romanian. With the help of some very talented (and some not-so-talented) people, the installation was finished close to schedule. There is a God.
RELATED: Avoid Common Callbacks with Imported Species
After much trial and error, we had found a way to stain the santos so it matched the ebony almost exactly, and both the main stairs and back stairs came out beautifully, if I do say so myself. Sanding the flooring was a little more of a challenge, since we were dealing with a very, very hard species with a beveled edge and aluminum oxide finish. First we shredded the finish using ceramic 80-grit belts on our big machine. We dropped back to flatten the floor, trying different grit belts until we found one that would work. We tried a 50 grit, but it didn't even scratch it. Then 36 grit, which gave us some scratching, but not much. We settled on a 24-grit and worked our way back up to 100, being careful not to dish out the santos feature strips. Sanding the medallions was tricky, as they were made of wenge and American cherry. All of that work was done starting with an 80-grit on the big machine and then hard-plating for what seemed like days to ensure everything was totally flat and scratch-free. We hard-plated the entire floor using a three-disc machine without skipping any grits: 60, 80, 100, then screening down to 120.
The floor was coated with an alcohol sealer to bring out the colors of the different species, then coated with a twopart commercial matte waterborne finish. All coats were applied with a roller due to the amount of lighting (both natural and canned), as well as all of the direction changes and decorative inlays. This work was done by coming in at 4:00 in the afternoon when the other trades left for the day and working at night, as well as weekends for the coating process.
Laborers covered the finished areas with kraft paper and 1/8 inch Masonite early the next day as we progressed. Leprechauns, elves or mean fairies would come in after we left and move the coverings so that people could ding the stair treads, get overspray on the floor or put masking tape on new finish, just to test our abilities at doing finish repairs. The final coat was applied after all of the other trades were out, and the only thing left to do was a small punch list before move-in time. I have to say even the obsessive-compulsive superintendent was very pleased with the finished product. "Happily ever after" time, right? Wrong!
But Wait, There's More
Remember the "once upon a time" part at the beginning? Well, this time happened to be August of 2005, and a nasty little storm named Katrina was passing west of our lovely peninsula. We got lucky, just some rain and wind as she moved north. But, there was more to come: In September, a not-so-nice lady named Rita came calling. She made one wonder why anyone would choose to live in the subtropics. Four major storms hit good ol' Florida that year, and the little Irish cottage was not spared. Doors that were guaranteed to withstand hurricane-force winds didn't. Windows that were built to hold back Hell's fury didn't. The newly planted royal palms and coconut palms now reside either in another neighborhood or in the Gulf of Mexico.
When the authorities allowed travel across the "Alley" again, we drove over at the homeowners' request to take a look at the damage. The 10 doors facing the water were blown in, and the great room, living room, den and master bedroom were flooded. The floors next to these entries were badly cupped and buckled in one area. The electrical outlets in the floor were still full of water, even though it was a couple of weeks after the storm. The best part: They wanted to know if they could still be in the house by Christmas. I asked if I could have a bit of whatever it was they were drinking. Being a man of faith, the homeowner said with a smile, "God never gives us more than we can handle."
Damage Control
Late in October, after coming up with a game plan, we went back to work. As you know, we couldn't get any more ebony. So, we had to carefully remove some of the undamaged ebony from one room to weave into the main living room. The den had a beautiful cherry fireplace, so we nailed American cherry in the place of the ebony. We had fans and dehumidifiers brought in and left them running 24/7.
RELATED: How We Handle Flooded Wood Floors
We had the appropriate "CYA" documents drawn up, as the homeowners did not want to remove as much flooring as we thought was necessary. We carefully and slowly explained what crowning was as opposed to cupping and that, in fact, it was caused by sanding a cupped floor too soon. We worked pretty much nonstop weaving, sanding and refinishing right up to days before Christmas, but we got the job done. There must have been someone looking over us, because the Irish clan had their cottage ready for the holidays. As I haven't heard from them, I assume that they are living happily ever after. Either that, or the superintendent has been committed.