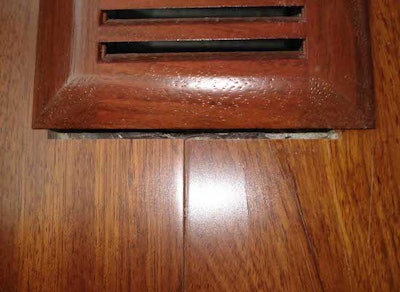
Many times during the installation, the installer or crew may be in a hurry to get the job completed and to get to the next one so they can get a jump on tomorrow. We have all been there and done that at one point or another during our careers. However, we must keep in mind the little things that may end up having us pull our tools and go back to the job site to take care of a callback.
Plank replacement is pretty straightforward for a wood flooring pro, but in most cases, the heat vents are in a window area, so fading can be an issue. The second concern is whether there is any leftover material. During inspections, I have seen situations many times where the installer had removed every stick of extra flooring material, so new material had to be ordered. If the flooring is discontinued, one relatively minor mistake like this can result in total flooring replacement. Or there is replacement material available, but it comes in a different color, gloss, width, etc., making plank replacement difficult for the installer.
The question is: How much did it cost the installer by not taking the time on the little things? Getting pulled off a job to complete the service call is bad enough, but when the replacement goes into extra costs, it can cost six to eight jobs’ worth of labor costs … just because of the little things. Are you paying attention and slowing down enough to notice those details? Not doing so threatens consistent profits in your installations.