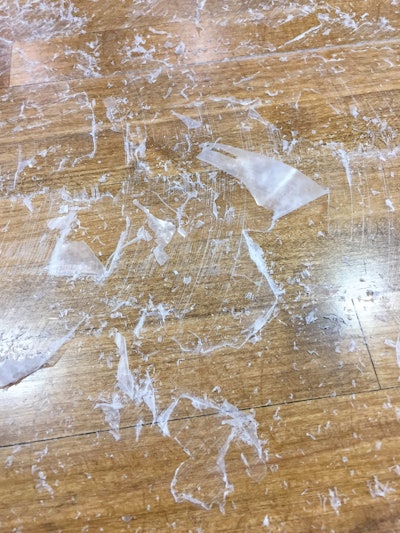
Most catastrophic finish failures are straightforward: a shortcut gone wrong; an “I’ve always done it this way” system failing; ignoring dry and cure times; not providing fresh/thorough abrasion, etc. The more difficult, and perhaps more important question is: “What am I doing that causes the finish not to perform up to expectations?” In no particular order, here are some of the main errors:
Not keeping it clean: Dust and debris are your finish’s worst enemy. When these particles show up in your final coat and you walk into a room of sticky notes, review your dust containment system and your final cleanup before the coating.
Flooding seams and end-joints (and even under the floor): Especially when stain is involved, getting too much in these areas does nothing but cause problems! The surface might be dry, but solvents bleeding out of the swimming pools you created between the seams, end-joints, and perhaps even under the floor will cause white lines (and eventually adhesion failure) as they build up under the sealer and finish. In some situations, it might be better to buff on/off, hand apply, or dip-and-roll a product versus a flooding process.
Mixing systems: While everyone loves to offer a “custom” system (i.e., solvent stain, solvent sealer, waterborne finish), most of us don’t have a lab to test and understand our system’s compatibility. You can affect the long-term performance of the top-layer coats (too soft, scratch easily, cloudy, etc.) without knowing it due to the different solvents/carriers trying to come up through the finish coats. Even layering one type of waterborne finish over a cheaper one to save money can affect more expensive top layers. And, did the customer know you substituted? Give them what they paid for and stick to the manufacturer’s full system and the recommended application rates; as well as the dry, cure, and abrasion instructions.
RELATED: Wood Floor Sanding 101, Part 1
Not understanding environmental conditions: Not fully understanding how the job site temperature, relative humidity, and airflow might affect your application, dry and cure times for each product will either cause you to take unintended shortcuts (e.g., not letting something dry long enough because it’s more humid than usual) and/or cause short-term and long-term issues with your coloration and coatings systems—ranging from peeling to blotchiness to easily marred coatings.
Not educating about floor care: So, you’ve done all this beautiful work and then let your customer go to the big box store to choose from a myriad of floor care products, most of which will leave an oily or greasy residue on the floor, if not downright changing the sheen levels (and perhaps contaminating the surface, negating future recoat opportunities). Give your customers the right products and educate them on vacuuming, cleaning, deep cleaning, recoating schedules, etc.
This waterborne finish didn’t fail, but with nearly floor-to-ceiling windows in the home, the contractor’s cross-board application shows up in the finish (even with a super-low sheen). Always coat the floor “with the flow of the boards” when possible.
This finish didn’t fail (it’s actually still 100% adhered through the scratch), but the floor owners' expectations in regard to their floors, their large dog, and his untrimmed claws were not talked through sufficiently beforehand. You can actually see how the scratch gets deeper in the spring wood, then jumps up on the summer wood—but still with the finish intact underneath.
This finish didn’t fail. It had a rotten bag of purple potatoes sitting on it for three months that soaked through and stained the floor. Finishes are very resistant to moisture and liquids, but they are not impermeable (vapor needs a route up through from the bottom). Plus, liquid can always run down the boards' side and end seams.