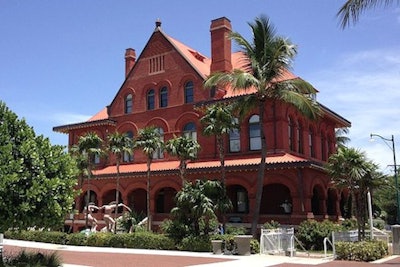
It is important to fine-tune your daily habits to prepare for potential problems by making decisions and judgments more simple and learning what to focus on and what to ignore. This is part of the 8 Ps: "Proper Prior Planning and Preparation Prevents Piss-Poor Performance." And by developing some new good habits, you can be prepared for trouble if and when there are problems. The other great news about these new good habits is that they will substantially lower the probability that you will ever have any problems.
Wood floor inspections that occur after there is a problem tend to focus on who to blame, then throw them under the bus. Wood flooring industry installation guidelines and the manufacturers' instructions establish what will be important to an inspector. As you navigate from preparing and submitting the initial proposal and the contract to managing the job site and installing the wood floor, in real time you only have one chance to do things "right" and document what happened. General contractors and building owners will develop much more respect for the individuals who understand and incorporate wood flooring industry guidelines into the fabric of their wood floor business.
You must document ALL of the issues that will be scrutinized by an inspector. The method of documentation should be irrefutable, permanently recorded, and easily retrieved. Maybe you should even send copies of this documentation to the GC and building owner. After all, "Good fortune favors the well-prepared." You can perform these habits and document these potential issues on the old Taco Bell receipts that are stuffed in the passenger's cup holder or employ a more organized, modern method of managing this stream of valuable data.
On May 1-4, 2014, in Key West, Fla., I am teaching a class on this topic AND conducting a wood floor service event at the Key West Museum of Art and History. Mornings are for the class, then after lunch we will be sanding and finishing the Goodwin Heart Pine Co. flooring that was installed in the main gallery over 10 years ago.
This is a work opportunity, not a training event, that is being sponsored by Goodwin and Bona. This is our work site:
We will be using Bona sanding machines, abrasives and finishes. Sitting and listening to someone drone on about technical information for an eight-plus hour day can be is excruciating, and three or four hours is much more bearable. We will be offering a discount to the participants who are qualified and want to help sand and finish the KWMAH floors on a first-come, first-served basis.
The morning class will focus on NWFA Guidelines, proposals, contracts, what and how to document, how to maintain and share information, waivers, warranties, and how to manage disputes. It is a complex series of interrelated topics. You will leave with a new perspective on the inspection process and managing disputes. It will also be an opportunity to network with your peers in one of the iconic locations in the U.S., The Conch Republic a.k.a. Key West.