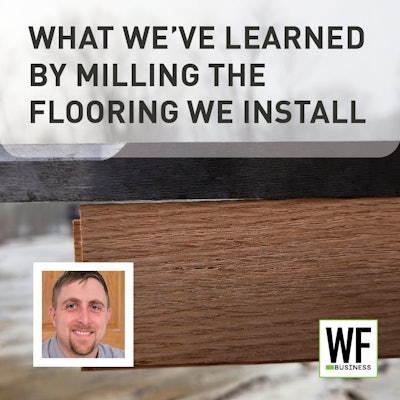
My brother and I are pretty unusual in the wood flooring industry because we are wood flooring contractors who also mill our own flooring. This also means we are spoiled: Because we mill our flooring, we are careful about the drying, milling and defecting. And because of that, when we are installing a floor, we don’t have to look twice at a piece before nailing it down. Here are some factors I think more wood flooring installers should pay attention to.
Waste factor: A couple weeks ago my brother and I were installing a wood floor the customer had bought from a big name in the industry, and even though it was supposed to be a high grade of flooring, it was garbage: It was full of shake, and the pieces were short, with hardly any over 40 inches long. We had to toss around 15% of the wood. When you’re having to spend so much time defecting the flooring on the job site, your installations take a lot longer. And finding shake after your final sanding or during staining/finishing is a big problem (especially for us water-based users). Shake can be difficult to spot, but a good mill should be able to defect almost all of it.
Snipe: If I didn’t mill wood flooring myself, I probably wouldn’t know the word “snipe” or understand it. You can get “side snipe” or “top snipe,” and it tends to happen when you have low-quality blanks that haven’t been dried properly or have stress in them, along with improper cutter head alignment with the molder fences. It happens more with narrower widths, because the blanks for narrower flooring tend to have a little more bow in them—the blank isn’t as stable because it doesn’t have the width. So it goes into the molder a little curved and bounces off a fence (I’m saying “bounces” but it’s really like 5/1000 of an inch) and when it comes out, the ends of the boards are very slightly more narrow than the rest of the board—side snipe. When it curves up into the cutter head, you can get face snipe. Even when you’re experienced at looking for it, it can be easier to feel than see. On the job, what it usually means is having to trowel-fill the floor to fill the gaps or do more sanding to get it flat.
Sanding steps: If you’re using really well-milled flooring and you’re making sure your subfloors are flat, you can shorten your sanding process. Some pros think we’re crazy when I say this, but our company only recently bought a 220-volt big machine. Because of our commitment to quality milling, tight tolerances, and minimal overwood, we’re able to start our sanding process with the Power Drive on our unfinished floors.
We’re charging a premium for our wood flooring services, so we better be living up to it, and it all starts with the product we’re using. I think if more wood flooring pros worked with good material on a regular basis, they would realize that the extra money they spend on the flooring is actually saving them in the long run on time, filler (we don’t use any) and aggravation.