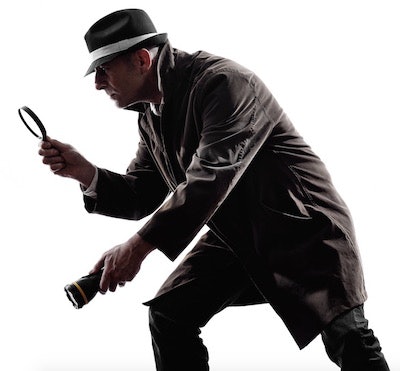
“OWNER/INSTALLER RESPONSIBILITIES: the customer/installer is responsible for final inspection of quality, and for moisture testing the subfloor and wood flooring.”
So who is the legally responsible party for the inspection at the time of installation? It’s simple, the installer!
This is nothing new to the industry. The installer always was the last one to inspect the product prior/during installation. What’s changed is how we currently look at the installer’s roles. Back when I started as an apprentice in 1971, we did a lot of prefinished Haddon Hall parquet. My boss, Jents Wilslev, would set me up with two 300-watt lights and a table made out of sawhorses and plywood. That was my station to go through every box of flooring to find bad corners, missing finish, etc. Then any culled material was marked with a grease pencil and placed back into separate boxes to be used for trimming along the walls.
So, what’s changed? It’s simple: the need for speed. Many installers are under the gun for production for the builders and don’t take the time for pre-inspection during installation. Then when those characteristics show up after completion, they will be held responsible by the homeowner or inspector. The question has been, “Is that fair?”
The truth of it is: “Yes!”
Almost every manufacturer has a statement like this within their guidelines:
“Our floors are manufactured in accordance with accepted industry standards that may allow possible defects caused by (manufacturing or nature) not to exceed 5%. Before installation, if more than 5% of the purchased material is unusable, contact your distributor/seller immediately.”
The reason for the 5% is not to put out a crappy product, but rather cover things such as damaged corners, missing finish, wrong color, etc.—things QC may have missed during the manufacturing process. Most manufacturers try to keep this under 1% or less, not 5%.
If you’re an installer, adapting a few simple rules will help avoid these installation concerns:
Once the homeowner turns on 2,000 watts of recessed lighting in the kitchen, you are now under the microscope.
• Carry good lighting on the truck. Lighting during install is so important. Once the homeowner turns on 2,000 watts of recessed lighting in the kitchen, you are now under the microscope.
• Rack out as much material as possible so you can inspect the flooring against your portable lighting. It’s best to view from different angles, because some issues can only be seen from one direction. Mark and use those for starters or trimmed ends.
• Do a final inspection upon completion before leaving the job site.
• Self-insure yourself by up-charging your install by 2%. That way, when a board or two slips through your inspection, just go back and repair at no cost to them.
If you follow a few simple rules, you can keep the homeowner happy, the inspector of your back and a strong referral base of clients.