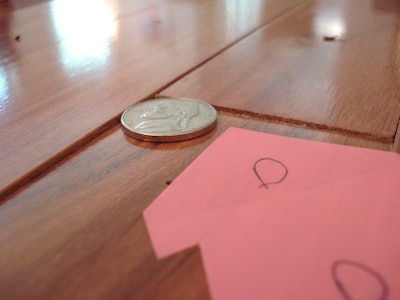
What should you do if you find overwood like this as you start installation?
The decision the lead installer makes is vital. If he proceeds with the installation, he knows the consumer is going to be unhappy and call the retailer. If he stops the installation, he may have to lay off his crew for the day and send them home, making them very unhappy. If this situation happens every other week, he will no longer have a crew. If he goes with the first option, proceeding with the installation, he’ll have to deal with the consequences later and potentially a wood floor inspection.
When the inspection occurs, the inspector will use the manufacturer’s installation instructions. Typically, at the very beginning of those instructions, they will state that the installer/owner must inspect the flooring. This gives the manufacturer an out for the overwood, because in many cases the installation guidelines will state “installation warrants acceptance.” This means that if our lead installer proceeds with the installation without contacting the retailer or the technical support at the manufacturer, he takes full responsibility.
A second dilemma for the installer is that the crew already opened more than half of the flooring cartons. At this point the retailer cannot return the open cartons to the manufacturer for credit or exchange.
The first thing we must learn from this is to slow things down at the beginning. Once the subfloor prep is completed and underlayment paper covers the subfloor, lay out the first 25 to 50 square feet for inspection. During this process, the installation crew can still stage the material but not open the cartons immediately. It is the installer’s responsibility is to stop the installation for defective material and contact the retailer, allowing the retailer to make the decision whether to proceed with the install or pull off the job. The best advice I can give is to make sure all correspondence be done in writing. With today’s phone technology, pictures are geotagged and can be attached to the emails for future reference if needed by the flooring inspector.