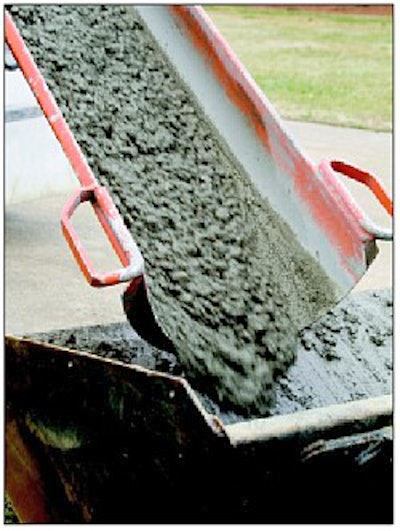
And when something goes wrong with their wood floor over a slab, they often don't know why it happened or what they could have done to prevent it. Maybe the floor cupped because the slab wasn't properly cured. Or, the wood flooring may be coming up in places where the adhesive didn't stick to the concrete. Whatever the case, the best time to familiarize yourself with the basics of concrete—and how to make it work with your wood floors—is before you have a problem.
Basic Recipe
Basic generic concrete is a mixture of fine aggregate (sand), coarse aggregate (crushed rock or natural gravel), water and various cementitious materials. There are also many lightweight concretes and gypsum concretes, which, if left as-is, are not suitable for installation of hardwood flooring, except for floating floors.
Concrete's ability to gain strength is due to the hydraulic properties of cementitious materials such as cement, slag, fly ash and micro silica, all of which react with water or free lime, Ca(OH)2 . This reaction is called hydration, and it's the critical reaction that enables concrete to harden. Essentially, cement is full of minerals that have had the water removed during the manufacturing process. As water is applied, these chemicals rehydrate and are able to form chemical bonds and recrystallize.
Just Add Water
The amount of water added to concrete is critical for strength development. If concrete were made only with the water needed for hydration it would be difficult to work with, and achieving the required consistency would be impossible. Therefore, extra water known as "comfort water" is added to achieve a desirable consistency and workability. However, the addition of too much water decreases the final compressive strength of concrete, so there must be a delicate balance between concrete's workability and the amount of water added.
The ratio between water and cementitious materials is called the water/cement (w/c) ratio. The higher the w/c ratio, the lower the strength. Generally, a 40 percent w/c ratio is considered optimum. The w/c ratio drives the economics and performance for both the concrete and flooring subs on a job site: Some concrete subs use as much water as they can get away with, as it reduces the amount of the pricier cement in the mix, but that creates greater application problems for the wood flooring sub. Too much water can wash away sand and create vacuoles (holes) in the slab, increasing the porosity of the concrete. This increases the transmission of water throughout the slab. The more porous the slab, the greater the likelihood of having a moisture problem.
In order to gain a balance between water, workability and compressive strength, chemical admixtures can be used to maximize water within the mix. Admixtures used for this purpose are generally known as "water reducers" or "plasticizers." Water reducers help manufacturers make workable concrete without the addition of extra comfort water. These products effectively disperse cement particles in water and improve plastic consistency of the mixture without strength reduction. Concrete with a water-reducing admixture will likely have a higher strength than the same concrete without it.
Gaining Strength
The strength of concrete is known as compressive strength, or its ability to withstand forces. Weak concrete may dust and crumble, causing a failure of an adhesive to bond. Compressive strength is affected by many factors, but the most important is curing. For concrete to be properly cured, water or high humidity is essential. If a sufficient amount of water is provided when concrete is hydrating, the hydration process can "grow" stronger. The majority of concrete hydration takes place within the first seven days, so this period is crucial for the quality of concrete. Better curing not only helps compressive strength but also increases overall concrete durability. The concrete slab isn't fully cured and ready for wood flooring for at least 30 days and sometimes longer. Attempting to install wood flooring over a slab that hasn't fully cured can lead to cupping, buckling and other installation failures.
Absorbing Moisture
Water plays a critical role in the formation of concrete, but it's the water that remains in the concrete slab that concerns wood flooring contractors. Remember that water can come from all directions. It can come from below the slab or through the walls. It can come from spills on top or the dreaded leaky pipe. Because concrete is porous, water can come from anywhere.
Underneath the slab, prior to the pour, various forms and thicknesses of different types of fabric are usually used as vapor barriers. Despite that, installers often run into wet slabs and need to use a topical treatment on the slab. The two most popular systems are penetrating epoxy primers and topical polyurethanes. It is important to note that all moisture barriers are really moisture "mitigators" or moisture "retarders." They reduce the moisture to levels that the wood and adhesive can tolerate. They do not eliminate moisture from the slab. Also keep in mind that water will seek the path of least resistance. So, if you put a moisture-control system over the slab in the living room, don't be surprised if the moisture starts to show up in the adjacent kitchen.
Because of its porosity, in many ways, concrete actually behaves like wood. It shrinks as it loses moisture and expands as it gains moisture. Just as with hardwood flooring, when a slab is not in equilibrium, it will warp. The concrete industry calls it "curling." It's normal to expect some curling on every project. However, severe curling should be taken as an indicator that there are likely severe moisture issues within the slab and extensive moisture testing would be wise to prevent failures to your wood flooring installation such as cupping, delamination or bond failure.
Moisture Testing
Oftentimes, there isn't visual evidence of moisture problems. That's why thorough moisture testing is a key part to a successful wood flooring installation over slab.
I could write an entire doctoral dissertation on the methods for detecting moisture in concrete, but for the purposes of this article I'll mention some of the most popular and important testing methods. If you're currently using the plastic-sheet method or the phenothalien test, I would suggest you use a more detailed testing method. Here are some of the major concrete moisture testing methods in use today.
Calcium Chloride (ASTM F 1869): The calcium-chloride vapor-emission test has been used for decades to measure the volume of water vapor emitting from a concrete slab surface over time. The test measures the amount of moisture emitted from a 1,000-square-foot sample of slab surface in 24 hours. It involves weighing and then encapsulating calcium chloride in a sealed environment. After 60 to 72 hours, the calcium chloride is removed and weighed a second time. The result is expressed as "pounds," which is the equivalent weight of water (emitted as vapor) over 1,000 square feet in 24 hours. This has long been the standard for moisture testing within the floor covering community. Unfortunately, this test is highly susceptible to corruption from outside elements. Ambient air humidity and temperature can significantly affect results. The test only tells you the moisture content in the upper 3/4 inch of the slab. Like the electrical impedance methods, it is an indicator of what is happening on the surface of the slab, not deeper within the slab.
Non-Destructive Moisture Measurement (Electrical Impedance): With this test, a specifically calibrated non-destructive electronic moisture meter is pressed down into the surface to determine the moisture content in the upper 1/2 to 1 inch of the floor slab. Moisture content readings are instantly displayed.
The meter measures the electrical impedance by creating a low-frequency alternating electric field that penetrates the material being tested. The instrument detects this current, determines its amplitude and derives the moisture content value. This test gives you a reading of surface moisture. On an 8-inch slab, it only reads to a maximum of the first inch. It does give an excellent indication of how wet the surface of the slab is, but does not eliminate the possibility of problems developing later.
Relative Humidity Measurement: Currently, there are two methods used for measuring relative humidity (RH) in the floor slab. These are:
The Insitu Method (ASTM F2170): This involves inserting sealable hole liners into holes drilled in the floor slab. This liner should be designed to create a test area at 40 percent of the depth of the slab. This sealed test area should be allowed sufficient time to reach equilibrium with the surrounding area within the slab (ASTM F2170-02 currently specifies 72 hours) before taking RH measurements with a humidity probe inserted into the test areas. This is an excellent test.
The RH Hood Method (ASTM F2420): This method uses a preformed insulated hood sealed to the floor slab with butyl sealant, creating a sealed chamber directly above the surface of the slab. The sealed chamber should be allowed at least 72 hours to equilibrate before taking RH measurements within this chamber with a humidity probe inserted into the test areas between the floor slab and the hood.
Consult the flooring manufacturer to determine the acceptable testing methods and moisture ranges of the slab for the specific hardwood flooring you're installing.
Before the Floor
Moisture isn't the only problem you may encounter with a concrete slab. Inspection of the surface can reveal a lot about the suitability of the concrete and lead you to some remedial steps to avoid problems. Here's a checklist of things to look for (some apply to existing slabs, new slabs or both):
- Is the slab relatively new or older? Most new concrete provides good bonding, whereas an older slab may need treatment with a primer before wood is installed.
- What is the compressive strength of the concrete? Is it lightweight concrete or gypsum? Weak concrete may dust and crumble, causing a failure of the adhesive to bond. A simple nail-scratch test is usually sufficient to indicate a weak slab. In some cases, a substrate consolidating primer can be used to prepare lightweight concrete for hardwood flooring.
- Is the slab flat? The best time to consider what steps you should take to flatten the floor is before you begin installation. Check the flatness and have a plan to deal with low or high spots in the slab. Usually grinding or self-levelers will take care of the problem. "Flat" means that the subfloor is within the most recent industry standards: for glue-down floors, it's 3/16 inch in 10 feet or 1/8 inch in 6 feet.
- Is there any chipping, delaminating, cracking, loose material or other surface defects? You need a sound surface to bond the floor securely to the concrete. Cracks and holes must be filled for maximum bond and lifecycle of the slab. Large cracks should have reinforcing bars applied.
- Is the slab clean? Drywall compound, paint and old adhesive must be completely removed.
- Are there any concrete sealers that might interfere with the bond of the adhesive? If so, the slab needs to be abraded before wood flooring can be glued down.
- Is there rebar or wire mesh in the slab? Check for surface cracks and stains that indicate corrosion has begun. This process will continue and eventually break up the concrete if not addressed properly. You may need to patch or repair the slab. If extensive repairs are required, a concrete professional may be necessary.
While this checklist helps us understand what's going on in a slab, sometimes failures are not our fault. A very high w/c ratio can lead to vacuoles in the concrete, which increase moisture migration. Short of drilling cores, there is no way to know this.
Sometimes, however, problems are our fault and could've been avoided. For example, lack of preparation of concrete heavy with excess water will lead to failure. So will gluing down a wood floor over a lightweight slab. Concrete may not be the most exciting topic, but gaining a better understanding of slabs and their potential pitfalls can help eliminate callbacks and leave you with happier customers.
Resources
• The ACI (American Concrete Institute) has excellent in-depth articles exploring the topic of concrete. It also has published a Guide for Making a Condition Survey of Concrete in Service that is a valuable reference for identifying most of the harmful conditions you will encounter in a concrete slab. The pictures included can help you determine the condition of the slab and identify areas for concern. For more information, visit www.concrete.org.
• The NWFA has several technical publications, including Installation Guidelines and Technical Manual A100: Water and Wood, dealing with installing hardwood flooring over slabs. For more information, visit www.nwfa.org or e-mail [email protected].
• The Portland Cement Association's book, Concrete Floors and Moisture by Howard Kanare, explains how to control moisture in concrete floors. For more information, visit cement.org.