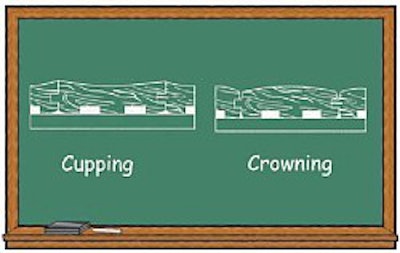
You hear it said so often that it's become a cliché — "water and wood don't mix"— but in reality, water and wood are inextricably linked, from the time a tree begins to grow and continuing throughout the wood's years of service as flooring. Flooring professionals and customers alike would do well to understand the relationship between water and wood, and the normal way wood behaves as moisture is added or subtracted. If you want to ensure a successful and lasting installation, here are 10 things you should know about the relationship between moisture and wood flooring:
1. Wood tends to contract as water is subtracted from its cell structure and expand as water is added. That's true when a tree is harvested and cut into lumber, and it's still true decades after the wood has been installed as flooring. This basic premise underlies everything else you need to know about water and wood.
2. Excessive moisture within a structure will tend to be absorbed by wood flooring, causing the wood to expand. In the most severe cases, the flooring can actually buckle and pull away from the subfloor.
Excess moisture might come from a concrete slab foundation that's not sufficiently cured, a crawl space that's not properly ventilated, or from a variety of other sources.
3. The structure should be at "normal living conditions" before wood flooring is brought to the site for acclimation (see No. 6) and installation. "Normal living conditions" means that the environment within the structure is at approximately the temperature and relative humidity that will be experienced during occupancy — during the life of the floor.
That means the structure should be fully enclosed, with doors and windows in place, and interior climate controls should be operating for at least 48 hours to stabilize the moisture conditions of the interior. Wood flooring also should not be delivered to the job site until plastering and painting are completed and dried. Moisture evaporates from damp walls into the air within the house, and some of it will be absorbed by the flooring.
4. Wood flooring that is installed too wet for a home's normal living conditions will eventually give up the excess moisture contained in the wood's cell walls and will shrink, leaving unacceptably wide cracks between boards.
5. Wood flooring that is installed too dry for a home's normal living conditions will eventually absorb moisture and will expand, creating cupping and — in extreme cases — buckling.
6. To avoid the problems created in Nos. 4 and 5, solid wood flooring should be acclimated at the job site until it reaches a moisture content that is consistent with normal living conditions within the structure. Engineered wood flooring usually does not require full acclimation before installation. Acclimation can take several days or even weeks, depending on how much difference there is between the moisture content of the flooring when it is delivered and the appropriate moisture content for installation.
The ideal moisture content for wood flooring installation can vary from an extreme of 4 to 18 percent, depending on the wood species, the geographic location of the end product and time of year. Most oak flooring, for example, is milled at 6 to 9percent, but wood at 9 percent moisture content may need to acclimate several days at the job site if the equilibrium moisture content of the site is 4 percent or 14percent. Experience and moisture readings from previous, similar job sites are your best guides to determining the proper equilibrium moisture content for a site. Also,the National Wood Flooring Association's Technical Reference Manual contains a map that lists regional variations in average moisture content.
7. Solid wood flooring should not be installed below grade. However, engineered flooring may be successfully installed above, on or below grade. Because it displays far less expansion and contraction with moisture changes, engineered flooring can be successfully installed in areas with wide humidity variations.
Below grade is defined as any part of the slab having four inches or more of earth above it. Additionally, walk-out basements are considered a below-grade application, even if a portion of the basement is above ground.
8. Wood flooring should not be installed over any subfloor or concrete slab that is not sufficiently dry. In the case of a wood subfloor (plywood or OSB, for example),the moisture content of solid strip flooring should be within 4 percentage points of the subfloor. That means that if your target moisture content for the wood flooring is 8percent, the wood subfloor should register no more than 12 percent moisture content.
Concrete slabs can present even more of a moisture challenge. Regardless of age or grade level, concrete will emit or conduct some degree of moisture, usually in the form of a vapor. Water in concrete is necessary to continue the process of curing well past the first few critical weeks. Therefore, all slabs should be tested for moisture before the floor's installation. Checking the moisture content of a slab can start 30 days after the slab is poured. However, in most cases it will take 60 days or more before the slab is dry enough for wood flooring installation to proceed. NWFA guidelines specify that emission of moisture vapor from a concrete slab should not exceed 3 pounds per1,000 square feet per 24 hours.
9. Testing for moisture should be a standard part of any pre-installation process. That includes testing the subfloor and slab, testing the interior environment of the structure, and testing the wood flooring itself. For testing wood floors and subfloors, hand-held moisture meters are the most important tools. Some moisture meters are also capable of testing concrete, but there are several other approved tests as well. Among the most common are the calcium chloride test, the polyfilm test, the humidity meter test and the phenolphthalein test.
10. Moisture retarders or moisture barriers will inhibit the effects of subsurface moisture on wood flooring. Moisture retarders are required in crawlspaces, beneath a concrete slab,between wood floors and concrete slabs,and are also recommended between wood floors and subfloors.
In crawl spaces, a ground cover of 6or 8-mil polyethylene sheets (preferably black) should be placed over the entire area of the crawl space soil, lapped at least 6 inches and held in place by bricks or other weights. In cases where concrete is poured to create a floor in the crawl space, the 6- or 8-mil polyethylene cover is still required.
Beneath a concrete slab, a heavy plastic, uninterrupted film should be laid between the base of gravel or crushed stone and the slab. Since placing this moisture barrier is normally beyond the control of the flooring contractor, the builder or home owner should be advised of this requirement before the slab is poured.
Between the slab and the wood floor or subfloor, there should be another moisture barrier or retarder. Common choices include low-end PVC vinyl adhered to the slab with a multipurpose adhesive; 6-mil polyethylene film applied over a skim coat of asphalt mastic; 15-pound roofing felt in asphalt mastic; and rubberized elastomeric membrane.
Solid strip or plank flooring requires a felt paper moisture retarder between the floor and subfloor. If a wood subfloor is laid over an existing slab, the moisture retarder can be cemented to smooth,clean-swept concrete.
Take the lead
Wood flooring contractors are rarely responsible for creating adverse moisture conditions at the job site, and sometimes moisture-related problems are beyond the flooring contractor's ability to resolve them. However, flooring contractors are responsible for knowing the appropriate moisture conditions, identifying potential moisture problems whenever possible and advising customers accordingly. It's also a flooring contractor's responsibility to not install wood flooring until the moisture conditions are appropriate.