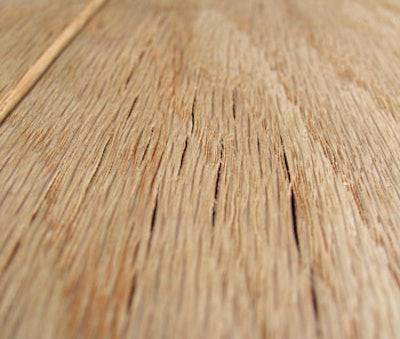
The Importance of Definitions
In order to properly identify checking in wood flooring, its definitions must first be understood. The following definitions were taken from the USDA Forest Products Laboratory's General Technical Report FPL-AH-188, Dry Kiln Operators Manual, Chapter 8-Drying Defects:
• Surface Checks are failures that usually occur in the wood rays on the flat-sawn faces of boards. They occur because drying stresses exceed the tensile strength of the wood perpendicular to the grain, and they are caused by tension stresses that develop in the outer part, or shell, of boards as they dry. Surface checks can also occur close to a knot, by gum pockets and mineral streaks, and in bacterially infected wood, as such wood is weaker than "normal wood."
• End Checks, like surface checks, usually occur in the wood rays but on end-grain surfaces. They also occur during the early stages of drying. End checks occur because moisture moves much faster in the longitudinal direction (along the board's length) than in either transverse direction. Therefore, the ends of boards dry faster and shrink (or try to shrink) sooner than the rest of the lumber; the end result is that stresses develop at the ends.
Hypotheses Through the Years
Various causes have been (and continue to be) offered about why checks develop in wood flooring after installation. The following examples of commonly touted hypotheses for checking in post-installation environments provide useful insight on where we as an industry have traditionally focused:
The wood checked because …
• it was installed in an uncontrolled environment outside of the 35%-55% industry-accepted relative humidity (RH) range
• it was installed within acceptable moisture content (MC) range but dried excessively during the winter months (during seasonal periods of low RH)
• it gained moisture during the summer and swelled excessively, causing checks
• it wasn't acclimated properly before installation (either too wet, or too dry).
Yet, as mentioned in the definitions above, the fact is that face-checking and end-checking develop as the result of drying the lumber too fast.
Looking at the Science
Numerous scientific research documents draw similar conclusions as to why and when checks develop in wood. The following excerpt taken from the USDA Forest Products Laboratory's General Technical Report FPL-GTR-118 Drying Hardwood Lumber, Chapter 9-Operating a Dry Kiln, says:
"It is virtually impossible for lumber to check at lower MC levels (under 40% MC); the only exception is if the lumber is subjected to unusually extreme drying conditions. At lower MC levels, the shrinkage of the core exerts compression on the shell, so sufficiently large tension forces to create checking cannot develop. Surface checks may open at lower MC levels. However, the checks are not being created at low MC-they are already there and are merely re-opening."
Therefore, end-use environments are not responsible for checks existing in hardwood used as flooring materials. Although variations in RH and temperature do influence MC and expansion and shrinkage of wood flooring and the size of the check opening, they are not extreme enough to cause the formation of checks in a piece of wood that is otherwise free of drying defects. Once wood dries below the MC saturation point of 28%-29%, it never again reaches a MC exceeding this value; in other words, the 40% MC mentioned in the previous excerpt is unattainable.
Images of Drying Checks
Checking can manifest itself in various ways in different pieces of wood flooring. Below are some examples of problems that are all referred to as "checks" or "checking."

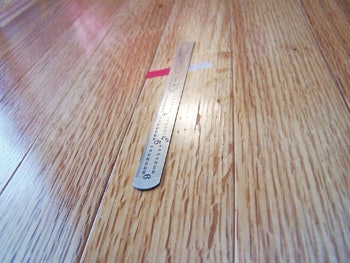
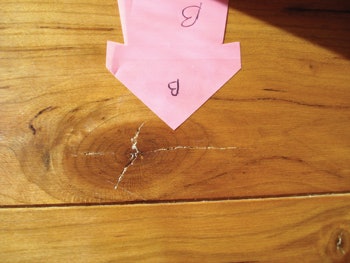

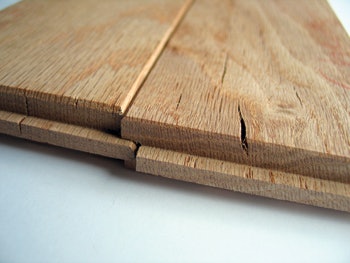
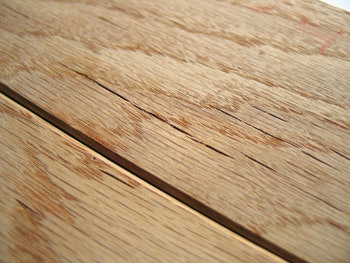
Checks in the Installed Floor
Wood science has long identified checking as a drying defect; but it is also important to understand the mechanics behind its visible (and invisible) presence within the installed floor system.
The initial defect(s):
• Checks usually occur early in the process of drying lumber, usually above 40% MC, before being cut into flooring.
• Checks develop because the lumber surfaces get too dry too quickly (in comparison to the board's core), and then excessive stresses develop as a result of RH that is too low.
Will checks remain open?
• Most checks, particularly those in hardwoods, close (but do not heal) in the later stages of drying. This occurs when the stresses reverse and the shell changes from tension to compression.
• For this reason, checks that close may be missed during quality control inspections during manufacturing.
Will closed checks reopen?
• Checks that are present but invisible will quite likely open to some extent during use because of normal fluctuations in RH that alternately shrink and swell the surfaces.
• Typical floor system stresses on individual and groups of boards can also prompt closed checks to open.
Site-related influence:
• With regard to hardwood flooring, there is little in the form of scientific evidence that supports checks being created by post-manufacturing interior environments. On-site, flooring will not be subjected to moisture content drops sufficient to create checking. In addition, the flooring's surface will be nearly twice as strong when dry (compared to wet lumber's strength), so forces required to check the wood would have to be twice as high.
Other factors:
• Variations in flexibility and brittleness in finishes impact the visibility of checks that open due to typical system stresses. Flexible finish coatings are more likely to expand and bridge the gaps, whereas more brittle finishes (especially if thin) fracture and make voids more obvious in both direct and reflective lighting conditions.
What's Next?
Education provides the opportunity for change. A general understanding of how and when checking develops in solid hardwood flooring is crucial if efforts to reduce the number of end-use claims are to be realized. Can checking defects be eliminated entirely during drying? No process is without flaw. The ability to dry and bring to market wood that is substantially free of checking does exist, but is the entire wood flooring industry likely to manufacture to such standards? From a practical perspective, no, probably not. However, individually, some drying operations within the industry do very well.
Supply and demand, the increase in foreign manufacture, the functional limits of the equipment used in manufacture, and fluctuating economic trends each limit the degree of quality control that can be expected prior to shipment of hardwood flooring. Our industry has determined that price and availability will be the primary criteria used in defining a products value. We have passively educated the consumer to a similar level of understanding. It is only when claims result and the potential of lost profitability is imminent that we are reminded of the importance of consistency, quality, and due diligence in defining product appearance and performance expectations to the consumer. When claims transpire, all too frequently consumers (and their living environment) are burdened with the blame, even though the checks were not caused by the consumer or by improper control of their environment
Preventative Measures
Grading standards are seldom utilized at any level in the marketing and sale of wood flooring, even though oftentimes the potential for checking is specifically qualified and quantified in these standards. Their placement on samples and within product literature would present an educational opportunity for sales staff at all levels. In addition, it would actively or passively provide the consumer with a means to acquire this valuable knowledge.
Consumers that have obtained product-specific information are less likely to voice complaints about the potential for previously disclosed and occasional defects in the finished floor. After all, wood is an imperfect and natural product. Color, grain, character, and performance variability combine to create and define each wood floor's unique and distinctive look.
In Summary
Consideration should be given to the fact that drying defects occur, and that eliminating their existence cannot be expected nor guaranteed. In most good-quality and excellent-quality flooring mills, a very small percentage of boards will continue to be manufactured with a small level of drying defects (both visible and invisible) and will be installed. Manufacturers' grading standards provide invaluable product-specific information that defines which characters and defects will be allowed, as well as their frequency. It is important that we make this information common knowledge for everyone's sake.
When checks in the solid wood floor are beyond the manufactured stated limits, claims should be handled swiftly and with clear understanding on the part of all parties that the consumer was not the source for the issue.
Special thanks to Gene Wengert, emeritus professor of wood processing, University of Wisconsin-Madison, and president, The Wood Doctor's Rx LLC, for his review of this article.
Important Points about Checks in Solid Flooring
• Checks are drying defects that occur during the lumber's drying process.
• Checks do not originate in post-installation interior environments.
• In many instances, installers cannot and will not see closed checks before the boards are installed.
• Closed checks, which are not visible prior to or immediately following installation, can lie in wait within the installed floor, completely invisible to the eye, and may become evident over time as the floor system is subjected to reasonable and expected stresses, especially when the humidity is dropping and causing the wood to shrink.
• Checks may be allowable (in some forms) as defined in manufacturers' grading standards specific to their products.
• Proactive sales and consumer education can significantly reduce the potential for post-installation claims relating to checking.
• If more emphasis is put on the quality of wood flooring rather than just price and availability, materials will be created to accommodate that.