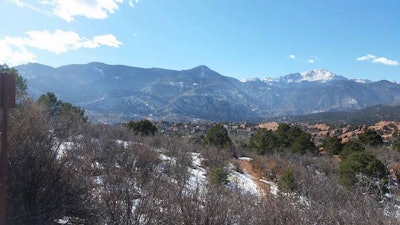
We aren't in Springville, Tenn., anymore.
My first comment? It’s a whole new world. But, like with most new steps in life, we learn how to adjust and adapt. The first few jobs we went on were simple straight-lay floors with a dark stain and a simple layout. At first look, they were nothing to brag or blog about, but then it hit me: They were wide hickory flooring stained brown.
I took the moisture meter out and hit the wood, subfloor and studs in the walls that were still exposed. The meter did not act right—it was too dry. I was shooting in the dark, a feeling very odd to someone used to my 12-14% MC world. The next step was RH and temp in the home. The temp was set at 68 degrees, and the RH was 16%—wow, that is dry! Our EMC with those numbers is 3.8%.
Let’s check and see if this 4-inch-wide hickory is still 4 inches wide. The short answer was, “Nope.”
The next step was the tape—let’s check and see if this 4-inch-wide hickory is still 4 inches wide. The short answer was, “Nope.” On the tape, it was very hard to see, but the micrometer showed it under size by 1/16 inch, or 0.0625. Now that is not a bunch, however, come spring that can be a huge problem. Just like in the South, we face the battle of change. Denver has four true seasons: spring, summer fall and winter. Where we did our work in Tennessee we would see three: cool, warm, and hot and humid. The winter months are not that long or that cold. Yes, we see below freezing, but not for weeks on end, nor do we see snow measured in the feet. So, doing the math in spring; if each board is 1/16 or 0.0625 small then in the spring that same board can grow back to a full 4 inches. In four boards, that is ¼ inch, and in 8 boards that is ½ inch … keep going. By the time we get across the room, they could have the same problem in Denver that we have in Springville, Tenn. The wood is still wood, and the action of the flooring is still the same. What changes? Not much, but the education is more important about the extreme dry air, four true seasons, job-site install conditions and the living conditions of the home after install.
We did go look at two homes that had both gaps that were more than 1/16 and what looked like cupping. The first response of the homeowner was, “My floor is dry-cupping.” I do not believe it was dry cupping. Here is my take on the “cupping” look. The flooring was installed last spring/early summer. It grew and, yes, it was very tight, with not much filler used. The flooring got a compression set from being so tight, and when it was fall and winter, the moisture was slowly released but the set didn’t lay back down. As it went into full-blown winter, the flooring lost the full 1/16 inch (or more, depending on the wood MC at install) and the floors now have the look of raised edges like a cupped floor. In my mind, a solid floor will not “dry-cup” like an engineered product can. The only way to fix that floor is to wait until spring, re-sand it and make sure the homeowner understands that 16% RH will not work with the flooring. They will need to add moisture to the home for the winter months and let the HVAC remove the moisture in the spring and summer.
Most of the homes, if not all, we visited were on a basement. To me, that is great because we can control the living space below. In the South we do not see many basements, and controlling the crawl space is the hurdle. Dew point is a factor for us when we install over a crawl space, and what a huge factor it is. We have to make sure that the crawl space is right. “Right” does not mean 6-mil plastic on the ground and you are good to go. What that means is the homeowner needs to understand that the vents need to be closed in the spring and summer and, if needed, open in the winter. I like having a controlled crawl space—making a basement, if you will. I like the information on Craig Dewitt’s website rlcengineering.com with regards to sealed crawl spaces and cross vents for a home.
We all have the same battle, and that is giving the same information over and over with each estimate we do.
So what did the miles of walking in another man’s shoes do for me? Well it has made me understand that each of us faces a hurdle. We all have the same battle, and that is giving the same information over and over with each estimate we do. The key is getting the facts on your market (far beyond what the other guys does or does not do). Start measuring and keeping the numbers from job to job and season to season in your market. Understand the change of all four seasons and how they will work or not work in the home. Make sure you inform the customers each and every time what they need to know on how flooring works. Give them the woodfloorbusiness.com website and ask them to do the research. The site has some of the best articles written by the best the wood flooring market has to offer. Use the NWFA training books and Guidelines, get them in print and give that information to the homeowner.
Here is the tap dance: Just because you let it sit on the job for a week and just because the manufacture says to get it plus or minus 2% on plank does not mean it’s ready to install. Be smarter than the wood, and know the hurdles you can face in your market. Most of all, keep this golden rule right on top: Get the house ready for wood and the wood ready for that house.