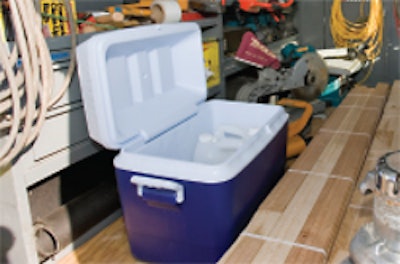
Sticky Situation
Some people have told me that when I do a plank job, I need to nail and glue the boards. Is that true?
Frank Kroupa, technical advisor for the NWFA, answers:
According to the NWFA's "Installation Guidelines," nailing and gluing plank flooring is not required, but the wider the flooring is, the more highly it is suggested.
There are things you can do without gluing the floor to help hold the plank flooring down. First, try to maintain your nailing schedule. If you're installing strip flooring and nailing every 8 to 12 inches, for flooring twice that wide, for example, you have to get your nailing pattern down to every 4 to 6 inches. With rustic material, you might be able to add enough surface nails in the defects for supplementary hold-down. Or, you might be able to drill and plug the floor.
If you decide to glue the floor as well as nail it, full-bed mastic is the most costly and the biggest hassle. There are other methods you can use. You could use a serpentine pattern, using tube mastic on the floor or underneath the boards. You could apply the mastic in a strip pattern, using the narrow side of the trowel, so the mastic is in rows about a foot apart. Or, you could use the strip mastic in addition to using mastic underneath the areas where the butt joints come together. No matter which method you use to glue, remember that adhesive sticks twice: Once where you want it and someplace else on you. It takes twice as long to do it right, so charge extra not only for your materials but also for the extra time.
Whatever method you use, keep in mind that gluing will not prevent gapping between boards and will not prevent cupping. It can stop some movement, mainly the up-and-down movement that's normally at the butt joints. Emphasize to the customer that wide plank will move. And, finally, the better material you have, the less likely it is you'll need some of these extreme measures.
The Name Game
I am getting requests from designers to install exotic woods, but with so many different names, how can I be sure the wood I'm ordering is really the wood they want?
Dan Harrington, director of product development at San Rafael, Calif.based EcoTimber, answers:
This is becoming more of an issue in our industry. For example, ipé (Brazilian walnut), is a name used for several species. In ipé's case, the different species have slightly different colors, so if you can identify and specify the individual species, you may be protecting yourself from suppliers that mix them together and provide more color variation than you expected.
We sometimes see American and European importers who are misinformed about the common name of a particular species and roll it out incorrectly in the marketplace. Many companies put catchy "pet" names on their products thinking they are unique, when in reality that name is already being used by others for a different species. For example, "Bolivian rosewood" generally refers to moradillo (morado), but a couple of importers have attached that name to massaranduba. Or, chechen, generally referred to as Caribbean rosewood or poisonwood, is now being sold by at least one importer as Caribbean cherry, even though Caribbean cherry is a name usually associated with machiche (black cabbage bark).
Wood names are generally not trademarked and carry different names in every country (and sometimes multiple names in one country), so ultimately, it's up to the purchasers of the wood to find out exactly what they are buying. If there is no scientific name available (some suppliers protect these from their competitors), be sure you have thorough information from the supplier (and/or others who have used the supplier's product) with regard to hardness, dimensional stability, photosensitivity, etc., of the exact product you are buying. In the end, if you buy a floor that doesn't perform to expectations, you won't be able to go back to the manufacturer because you thought it was a different species. Ultimately, it's up to the purchasers of the wood to find out exactly what they are buying.
In the Dark
I need to get my stain to look darker, and someone told me to just apply it twice. Will that work?
Russell Bates, product manager at Baltimore-based finish manufacturer Lenmar Inc., answers:
As industry trends move toward darker and more opaque colors, we are seeing more service calls on finish behaving badly over stain, which is usually related to a problem with the stain application. Typical wood flooring stains are "wiping stains," which offer many benefits, but one of their major drawbacks is that it can be difficult to obtain darker colors.
All wiping stains leave behind pigment particles of colorant on the surface of the wood. There is only so much pigment that can be loaded into a wiping stain base. To make the stain look darker, some finishers try to add extra pigment to a wiping stain. Or they may try applying the wiping stain, then not fully wiping it off. Or, they may apply the stain once, then reapply a second time, or even a third.
When a wiping stain is applied and fully wiped off, the level of pigment remaining on the surface is quite low, so there is enough wood fiber available to allow the sealer to obtain good adhesion. When a stain is applied and not wiped cleanly, or when a stain is applied over itself more than once, the pigment particles begin to build up on the surface of the wood, leaving the sealer less wood fiber for adhesion. After a certain point, the finish may degrade faster, and it may chip and flake off. Product failure in the field for dark stain colors is almost always due to too much pigment left on the surface of the floor.
So, what's the solution for darker colors on wood? Water-popping can cause a floor to be more open and accept more pigment. (For more on water-popping a floor and staining, see the "Stain Savvy" article in the December 2005/January 2006 issue of Hardwood Floors.) Most suppliers also recommend adding dyes to their stains. This is a trickier application, though, because the product will tend to leave lap marks, will not stay open as long and can be more difficult to repair.
Trick of the Trade: Avoiding Extremes

Just like humans and wood floors, finish has a comfort zone. When it's applied, it should be in the same temperature range as the floor, which should be at normal living conditions. That's why it's a good idea to keep your finish in a cooler in your truck or van. The cooler helps protect the finish from temperature extremes, which can cause problems—finish that's too hot can be hard to apply, flash off too quickly and/or leave applicator marks, while finish that is too cold can be difficult to apply, will not level out properly and can have problems curing.