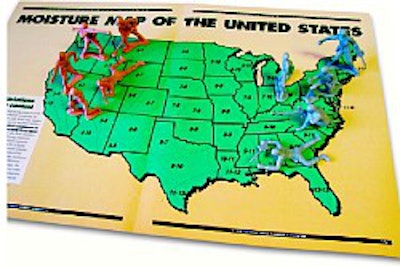
Ask any wood flooring contractor what causes the most problems with hardwood floors, and you can bet money he'll say "moisture." The problems are endless: too much humidity, not enough humidity, a wet subfloor, a nearby pool, a poorly graded yard, etc. That's why the best approach is to be aware of as many problems as possible and take steps to avoid each one before the job even begins.
Of course, that is easier said than done. Further complicating the situation is the fact that each region of the country may require a different approach. A contractor installing floors in Minnesota probably won't follow the same steps as one in Miami. To find out exactly how contractors in different regions attack the moisture situation on their job sites, Hardwood Floors spoke with three exemplary wood flooring contractors who have three drastically different moisture situations: one on the East Coast, one on the Gulf Coast, and one in the desert of New Mexico. Read on to find out how they win the war against moisture.
East Coast
Contractor: Charles Peterson, owner, Connecticut Premier Hardwood Floors
Location: Gales Ferry,Conn., with business including nearby Rhode Island and New York
Construction: Mainly homes over basements
Typical wood floors: Solid oak and maple strip, solidwide plank
Moisture conditions: Big swings in humidity, with moisture content of the wood flooring ranging as low as 4 or 5 percent in the winter and up to 12 percent in summer. "During the summertime, everybody opens their windows in their cottages and houses and lets all this wet air come in. During the wintertime, they shut them and turn on the heat—relative humidity can be around 24 percent," Peterson says, adding that sometimes in winter the moisture content of the wood is so low that the meter won't even register.
Plan of attack: Peterson's strategy is simple: as closely as possible, hit the midpoint between the extremes of the wood flooring's moisture content (MC) levels during the year.
In order to do that, he examines everything concerning moisture on the job site. An initial checklist includes items such as gutters, drainage, proximity to water and the type of HVAC system. From that, he develops a general idea of what the home's moisture levels will be throughout the year.
From there, he turns to the numbers:meticulous moisture readings throughout the home. Before the wood arrives, here cords the relative humidity of the basement and upper floors and moisture content of the joists. He also takes MC readings of the subfloor in various spots throughout the installation area and records the readings on the subfloor with a black marker. He keeps moisture reading logs in each job folder. The data contained in these logs are invaluable if moisture problems arise in the future.
The wood flooring for the job typically arrives direct from Peterson's distributors. Once it's on site, he takes the readings all over again, also recording MC indifferent pieces of flooring from the broken bundles. Red flags include large variations in readings between boards, or excessively high or low readings. If they show problems, he may rack out the floor and let it acclimate further. All of these are factors taken into account when he determines how long the wood will acclimate before installation.
Typically, the wood arrives with an 8percent MC—usually close to the target MC midpoint. During the summer, Peterson says a long acclimation period can be too much of a good thing. "At some job sites, it can be a little damp with the windows all open; the MC will shoot up to 12percent. Then, when they dry it out to 4or 5 percent in the winter, there aren't a lot of happy people," he says. "If you keep the MC around 8 or 9 percent, even if it gains a little moisture, you're not going to end up with problems; it won't expand to where it's going to explode or crush."
The same principle applies when determining acclimation during the winter. "I'm always trying to hit the midpoint of where this thing is going to be most of the year,"Peterson says. "If you're at 8 percent and it goes down to 5 percent, that's not too bad, and up to 12 percent it's still good—you're not going to end up with big gaps or boards buckling."
Plank flooring proves to be particularly challenging in such moisture conditions. With its greater capacity to expand and contract, it requires even more diligence. The first step is customer education. "Is how them what their moisture contents are throughout the house, and I always calculate what their gaps will be later on,"Peterson says. "I tell them, 'At the moisture content we're installing at, you can expect this gap. I notice you don't have any humidification in here. If you don't,the gaps may go down to this. You ought to install a humidifier in your home.'" During installation, he makes sure that the MC of the flooring is within 2 percent of the subfloor MC and follows manufacturers' directions precisely.
Token bad moisture story: "We were doing this mansion, and they had a severe time limit on it. It was wide plank white oak, and they wanted to stain it white. It was raining, and I had to take a ferry to this private island and stain3,000 square feet of white oak. It went around columns and center islands, and into bedrooms and bathrooms. They had an important client coming back who wanted the house for Thanksgiving. I said, 'Look, there's a 50 percent chance that the finish will fall off; this really should sit longer.' The guy said he had to have it. The stain was allowed to dry for five days. Moisture readings were taken prior to staining, sealing and the water base finish coats. The weather never cleared up for the duration of the job. The general contractor turned off the heating system every time I left. Around the outer walls and French doors the floors had some cold spots. It took a little bit of time, but the finish peeled around the sides. I had told him and told him,but it ended up costing me $3,500 (never collected), plus doing the job from scratch all over again."
Advice: "Never take a chance on a floor failing. You are the only one who will be responsible for the consequences. Having a customer sign a waiver will not hold up in court. You are the professional and are expected by the court not to deviate from the correct technical procedure."
Gulf Coast
Contractor: Michael Browning, general manager, Browning Brothers Flooring Co. Inc.
Location: Mobile, Ala., and the surrounding Gulf Coast region
Construction: Mainly homes over slabs,some crawl spaces Typical wood floors: Solid oak strip, unfinished engineered strip
Moisture conditions: Wet. "We're right here on the Gulf of Mexico, so we're wet. Our humidity runs 90 to 100 percent pretty much the whole year. If it ever does get down to 60 or 70 percent, it's like paradise. We get lots of afternoon showers, and after that it's like a sauna,"Browning says.
Plan of attack: There isn't much unpredictability in planning for moisture content of the wood flooring. Even with the air conditioning on, the relative humidity stays on the high side. "The only time we have a shrinkage problem is when they really heat it up," Browning says.
A key element in preparing for the high moisture content is choosing the right product. Browning installs many solid strip floors, but the prevalence of slab construction often has spurred him to choose unfinished engineered flooring. Customers may balk when he tells them solid products aren't the best choice for their job site, he says, but when he explains that the unfinished engineered has the same appearance and wear layer as the solid product, they're pleased.
Before installing over a slab, Browning asks whether a membrane was installed under the slab. He uses a concrete moisture meter to test the slab before the wood floor goes down, although he says the slab usually is cured long before he gets to the site, and he rarely encounters slab problems anymore. "Everybody now is so cautious about checking before they jump in there to work—if there's a problem, they go back to the contractor, and he goes back to the slab man," Browning says. If there is a problem with the slab,he'll use a calcium chloride test to confirm it.
In the meantime, the wood flooring has been in storage at Browning's warehouse,where the lack of air conditioning mimics the same conditions found at most job sites—Browning says few builders turn on the air conditioning until the home is occupied. If the job site is air conditioned,the flooring acclimates on site. Browning takes moisture readings in various areas before installation and at the time of installation. The MC is checked again before the floor is sanded and a significant change in MC serves as a warning signal to keep waiting.
After installation, Browning leaves more time for acclimation—typically one week for unfinished engineered products and at least three weeks for solid products. Although he tells builders ahead of time, this still can come as a shock. "Lots of times the guys call and say, 'Put the wood in,' and we say that we'll need three weeks before we come back and sand it. Their mouths open, their jaws drop, and they say, 'You just blew my whole schedule,'" Browning says. Sometimes the contractor didn't bother to pay attention to the required time frame, or sometimes he just figured that when the time came, he could bully the wood flooring contractor into doing it faster. "What we do now is hold our ground," Browning says. "We tell them, 'Give me a release, and I'll do whatever you want me to do, but until I get that release, this is the way it's going to be.' We try to work with them as close as we can—if we can fudge a little, we will,but it's something we don't want to do,because we've eaten too many jobs."
The importance of waiting for the right length of acclimation is demonstrated by the number of phone calls Browning gets from unhappy clients—of other wood flooring contractors. Typically, the problem is that the contractor installed the solid floor and sanded it within a week or less, leaving a cupped mess.
Control joints are a common strategy to deal with the inevitable expansion. Browning recently did a floor for a gymnasium without air conditioning. The wood flooring was installed with a 1/8-inch control joint every 2 feet, and he waited 30 days before sanding and applying one coat of sealer. Every control joint had closed. Tobe cautious, he waited even longer to complete the finish coats. That situation is more typical than anything, he says. The key is "keeping track of where the moisture is on the job site and what the results are before you start sanding. It's so easy to sand too soon, and three weeks later it's cupping on you."
Token bad moisture story: "We did 8,000square feet of a patterned floor in a casino in Biloxi. There was lots of intricate work and patterns. Every two feet in the pattern and around the pattern we left a control joint. Before we completed the job,they were closed up. We went back and resawed them, putting them back in again. By the time the job was done, they closed up again. We sanded and finish edit, and then in a month's time it cupped. We had taken every precaution that we could, but the contractor decided to sand it and keep it on schedule. It was a combination of the air conditioning not being balanced, being next to a pool area and being on the Gulf Coast—those three things."
Advice: "Trying to make the general contractor happy, we've taken some risks, and it's just not worth it."
Southwest Desert
Contractor: Tom Anderson, general manager, Kimbrough-Carpenter
Location: Albuquerque, N.M.,and surrounding area
Construction: Mainly homes over slabs Typical wood floors: Solid red oak 21/4- and31/4-inch strip
Moisture conditions: Dry, with some seasonal variation. The monsoon season of rains during August and September, as well as evaporative cooling systems used during the summer, create some variety in humidity. "The times of the year that we have problems are much the same as in other areas of the country, but people don't think of them happening in New Mexico," Anderson says.
Plan of attack: Just as Peterson acclimates floors aiming for a midpoint in the predicted moisture content, the same is necessary in the usually arid New Mexico environment. During the winter and spring, the relative humidity easily can be in the 20s. During the monsoon season,humidity can jump up around the 70 percent range. The use of swamp coolers, a cooling system that essentially blows cold, moist air into the house, can have the same effect on relative humidity. The systems typically are turned on in April or May and run until the end of September.
The first step, Anderson says, is educating consumers on what to expect for seasonal changes in the wood floors. If they know that the floor will expand and contract throughout the year, they won't be shocked when gaps appear. There's noway to avoid the movement, Anderson says. "When are you going to acclimate—when there's the swamp cooler running and the monsoons? Or in the springtime when it's really dry?" he says. His strategy is to aim for the middle ground and make sure the customer's aware of what will happen.
Kimbrough-Carpenter's 3,000-square foot showroom goes a long way toward helping in the education process. There, customers see different species and types of products installed in a real floor. "We'll point out cracks and tell them, 'This is what wood does,'" Anderson says. It also gives clients a chance to see how different species react, seeing for themselves that gaps show up more in a maple floor than in a darker species, for example.
Like many wood flooring contractors,Anderson also tries to advise his customers to use some sort of humidification system in their home, although he says it's still uncommon. "Most people don't do it,because they don't realize how important it is for the wood. If it was more of a standard, everybody in the wood flooring business would be happier. Short of that, what we need to do is acclimate the product as best as possible," Anderson says.
When sourcing material, it's crucial to get wood flooring from a reputable source, he emphasizes, avoiding wood a tan unacceptable moisture content, for example. "We usually get moisture readings on material when we get it and when it goes in at the job site. We also like to use hygrometers to find out where the home is running," Anderson says.
Usually, wood arrives to the warehouse at a MC of 7 to 9 percent. The warehouse,with its swamp cooler system and forced air heat, replicates very closely the conditions at most job sites, he says. That's important, as it can be difficult to acclimate the wood on many remodel job sites, he says. The company does try to ensure that all HVAC systems are up and running before the wood arrives. Although that may not always be possible, it's essential when dealing with radiant heat systems, which are popular in the region. "We'll dictate to a builder that the radiant heat is on for 10 to 14 days because of how much movement you get out of a radiant floor," Anderson says. Once conditions are right for installation, a floating subfloor of two layers of CDX plywood is used with a moisture retarder of 15-pound felt. After installation, Anderson tries to wait another week before the floors are sanded and finished. "I'd like to see it pretty stable,"Anderson says. "If it goes in at 6 percent and now it's at 8 percent, I'd be real concerned about that."
With careful attention paid to moisture throughout the project and the customer educated on what to expect, there usually aren't too many problem calls regarding cupping or shrinking. "During the winter, people call and say, 'I've got cracks.' I say,'Yes, you do. Look at your hands, they're probably cracking too.' I point out their kitchen cabinets or interior solid doors. I always like referring to something else." For support, Anderson turns to NWFA publications, especially the moisture content charts. Whether it's pacifying clients over the phone or going out to the job site to take a look, quickly taking care of the customer leads to fewer problems.
Token bad moisture story: "We were putting in 3-inch solid red oak plank in a house that had radiant heat. The builder said, 'I don't have time to turn the heat on—install the wood floors and I'll take the liability for it.' We installed the floor, and a year later during the dry season, it shrunk so much you could actually seethe tongues through the gaps in the flooring. We didn't have to replace the floor,but we did have to go in and do some cosmetic work—at our own cost."
Advice: "The best thing we can do is educate the consumer, because you can't acclimate the floor perfectly."
A key resource
When planning for moisture, a vital source is the NWFA’s Technical Manual A100: Water and Wood. In it, you can find information on understanding moisture content, computing wood’s potential expansion, using moisture meters and more.
NWFA members should have a copy as part of their membership packet. To purchase additional copies, contact the NWFA at 800/422-4556 (U.S.), 800/848-8824 (Canada), 636/391-5161 (local and international), [email protected], or www.nwfa.org.
No acclimation=litigation?
Contractors routinely are pressured to install wood flooring under bad moisture conditions. Asking abuilder to sign a waiver of responsibility can be enough of a threat to convince him to do the job right instead. If he does sign a waiver and you proceed with the job, you won’t necessarily be protected in court. Consult with your lawyer as to exactly what your liability is. Ultimately, it is up to each individual contractor to decide how much risk he or she is willing to shoulder.