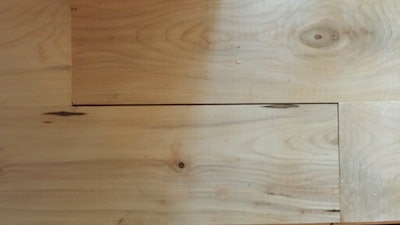
Yep, this is a play on words, but with some luck I can get all of us playing in the right direction. How many times do we walk in to a job site and see four or five business cards sitting on the table? Theyâre all doing the same thingâfree estimates, with the same goal: get this job!
The hardest part of an estimate is getting past the low-cost, weak-skilled, under-educated and, well, not to be ugly, but ⌠bad floor people. Just this week I was asked to go look at two floors, one had troubles with cupping and the other was not milled right.
The cupping floor was all due to the poor up-front job site inspection. The bad milling was just that, and the flooring was replaced at no charge ⌠but that was just the start of that can of worms. Let me go into detail for each job.
Cupping Floors:
This was 10-inch-wide red oak installed last winter. It looked great until seasonal heat and high humidity came to the sunny South. The homeowner removed some of the flooring so that it would not push out the wallsâyes, it was that bad. The manufacturer stated that it must be glued and nailed down, so they did that with a glue gun and Liquid Nails. About every foot they ran a line of glue and nailed the fire out it.
This was not the reason for the failed floor, though, it was the moisture coming from the crawl space.
This was not the reason for the failed floor, though, it was the moisture coming from the crawl space.This was not the reason for the failed floor, though, it was the moisture coming from the crawl space. As I walked around this 100-plus-year-old home, we could see cracks in the foundation large enough to put two fingers into. The gutters dropped the water right to the foundation, and the yard was pitched back the house. We did what we had to do and opened the crawl space door to find no earth cover. There was water and mud, plus daylight through the rock foundation (not brick, only God knows how old this rock foundation is). They took rocks from the farm and made the crawl space walls. That is okay, but over the years they need to be tended to, including filling in the voids and cracks, keeping the rain water off the wall to prevent the breakdown of the mortar, and, yes, installing ground cover, as well as lapping it up the wall to prevent moisture from getting into the space. The homeowner paid big money for this floor, they wanted an old look with wide plank to keep the look that the home once had. Yes, they went with the lowest bid and got what they paid for. Not one contractor went under the house, walked the outside of the home or talked about rain water management.
For them, it will take $4,500-$5,500 to correct the crawl spaceâfunds they do not have because they spent it all on the remodel last year. The painful part is telling them the manufacturer (not us, thank God) wonât stand behind poor workmanship. They have no claim with them, and the flooring installer, well, he doesnât seem to be doing floors anymore. They have tried phone calls and emails, with no response.
Bad Milled Flooring:
1. Did your installer check for moisture in the subfloor?
2. How long has the flooring been in the home?
3. Why is the HVAC unit shut down?
4. Did they leave a expansion around the walls?
5. Were the folks installing the floor the lowest bid?
Letâs go through them one at a time.
1. Nope, they did not test for moisture, they said one week and it is good. (Right now the wood is 8-9% and the subfloor is 13% on top and 21% at the bottom.)
2. One week, and it was good to go per the flooring installer. (That was, one week all stacked up along one wall to make install faster because they didnât have to move it again!)
3. HVAC is off because it will make the home cooler, they can open windows during the day. We are getting cooler here now, so the high heat and RH are better, it is best to let the wood get used to that than the heat or air.
4. They left ½ inch around the walls so the base would cover the gap. (The problem is it is now tight to the walls in some spots and a Âźâto 1/8â gap is all they have now in other areas. They was no center layout; they went off one wall they felt was straight.)
5. Yes, they were the lowest bid by more than $0.50 than the next guy. The highest bid to install was $2.50, and the lowest bid was $1.50. The $1.50 got the bid. So the bids were all over the place.
Now letâs get into the job site. We looked in the crawl and there was no earth cover, there are no gutters, windows are open, it has incorrect layout with ½-inch expansion andâthe killer to me and, yes, this is a debateâSTAPLES. Is this job going to fail? You bet it is!
Now, I may not know what I am talking about, but I can read.
I looked at the flooring, and at every point that the staple went in, it split the tongue. They did maybe 20 rows before they called to say it has gaps, so thank God they stopped the install. I went through the NWFA Guidelines regarding all of this with homeowner before I left that job site; we pulled information off different websites to show that my information is not coming from me but the folks that wrote the rules for flooring. Here is the kicker: The homeowner went over the information with the installer the next day, and the installer said, âHe has no idea what he is talking about.â Now, I may not know what I am talking about, but I can read, and not one manufacturer will tell us to install flooring without earth cover. The term ânormal living conditionsâ will pop up somewhere in the instructions. That homeowner has let the installer go, I hate it for them because we all need the funds to pay bills, but I am happy for the homeowner. They are going back to the start and getting new flooring at no charge, and they are getting bids to fix the crawl space, get the HVAC going and making sure the flooring will be installed correctly based on the written word from the NWFA and the flooring mill.
Take the time to do a real estimate, look at the job site. I still hear Mickey Moore telling me, âBoy, get the house ready for wood, then the get the wood ready for that house.â Words of wisdom and words for a lifetime of great jobs.
So, long blog cut short: Crawl in the crawl before you walk in and install. Crawl before you walk, and walk before you run. That makes our task of getting the job done right (instead of just getting it done) so much easier.