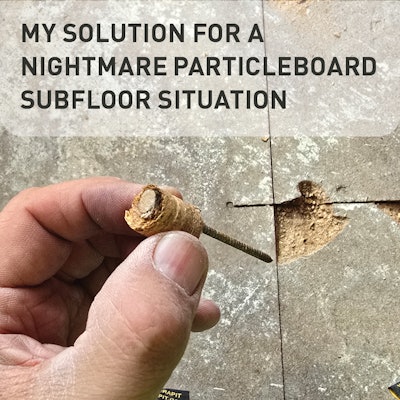
I was hired to do a 475 square-foot simple install on the second floor of a home nearby. There was existing carpet that badly needed a re-stretch, and it felt lumpy underfoot. I figured the padding was crumpled and/or disintegrating or something, and since the client said “no” to that mess, the excitement was high for a new wood floor. Removing the carpet, padding, tack strips and the 18 zillion padding staples was the agenda for our first day, and we set to it like bright-eyed, bushy-tailed squirrels. I was thinking that with the base molding they wanted, I was into this for about four days or so, depending on how long it would take the paint on the molding to dry.
I set the team on this carpet demo and quickly went to the distributor and picked up the flooring materials. I was gone about 1 1/2 hours or so, and when I returned the padding was rolled up on the curb as I directed. I walked inside to get a look at what was accomplished in my absence, and as my roving eye of Sauron set itself on the subfloor, I beheld a terrible sight. The subfloor wasn’t what I expected, and I had a problem on my hands to deal with. There was only particleboard in every room. I had thought the carpet was lumpy … but it was the particle board! It was sagging between the joists (duh). It was ¾ inch thick, and it was tongue-and-grooved on the long sides. As we all know, particleboard is not to be used as a subfloor for any floor, and especially directly laid over joists, as it was here.
I had to confront my client with the discovery, but before I did, I wanted to build a case. I called one of you Master-type pros just to make sure I was in spec (I was). Then I called the wood flooring manufacturer, and they said (as you already know) particleboard is not acceptable. Not only that, but I couldn’t even leave it in place to stay compliant with industry standards or the manufacturer’s guidelines.
Then I asked the manufacturer’s technical advisor if they would respond to an email wherein I would ask if this particleboard is okay. I got the email back within minutes and forwarded it to my client. After reading it, the client informed me they still wanted their new wood flooring, and they wanted a solution from me—and quickly, if possible. I swept up and left for the day, took the discarded carpet to the city dump and went back to my office to sort this out.
About an hour after that, I emailed the client with the remedy, and after a few hours more, they texted to go ahead with my solution, which was replacing the subfloor to comply with industry standards. I like CDX plywood better than OSB (my subjective choice), and I created an additional work order to take with me in the morning.
After signing that, we set about replacing the panels one at a time, starting with the client’s soon-to-be office.
My action plan called for de-nailing and de-screwing the panels first, then removing them in whole pieces. As you know, particleboard falls apart pretty easily, and I did not want to take a bunch of shards to the dump when I could take a relatively few panels instead. All I needed was 17 sheets in, so 17 sheets had to come out.
I just hired a “new guy” from New York, and I set him to de-screwing and de-nailing, and the screws came out easily, just as you may think. The nails, on the other hand, were ring-shanked, and the heads of the nails were not as strong as the shank. The result was the heads just folded under the stress like miniature umbrellas in a hurricane. This de-nailing thing just wasn’t going to work. The ring-shanked nails were much, much stronger than the particleboard, too. What a bummer! All I want to do is finish this simple, little install, and it’s growing to be way more difficult than it needs to be.
I’m okay with the work, but recalled a similar application and devised a practical solution. I bought ¾-inch hole saws and grabbed a scrap piece of ¾-inch plywood and drilled a hole in it with the hole saw.
Then I placed the plywood with the hole in it over a nail and using the plywood as a “guide” or “bushing” of sorts, drilled a hole around the ring-shanked nail only as deep as the thickness of the particle board.
The result? The sheet lifted right up after all the nails were drilled, and all that was left were the round nubs of particle board left in the joists with ring-shanked nails through them:
The “new guy” was amazed, and he said that’s not the way they do it in New York. I asked how they do it in New York, and he said they just beat the floor with hammers and take out all the little pieces. He liked my little trick a lot better. I told him, “We don’t do it New York style here,” and he laughed.
So, this not only works for particle board, but with any subfloor you need to tear out. I’d rather take out larger pieces than oodles of tiny, pointy pieces you can’t put in a trash bag.
As the new plywood panels went down, the subfloor immediately became flat and strong like it is supposed to be.
This is one of the tasks that seems daunting from a distance, but when you are in it - is pleasurable and actually enjoyable because you are winning in quick, spacious strides to the finish line: the paycheck.