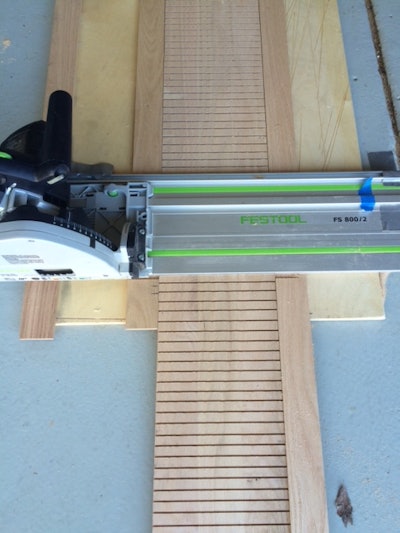
It was not a fancy house. It was a beat up, dated and old one. I walked in to meet with the owner. She wanted a new 5/16-inch (7.9375mm) floor in her kitchen and some repairs in the existing floor. She said her husband wanted a double-curve nosing and riser on the one step down to their living room. I looked the job over and I was thinking this was a small job. It would take me the same amount of hours to install the new floor as it would to make that one piece of nosing. Don’t get me wrong, I could do it with no problem. The sad thing is that I looked at that nosing as an annoying detail. It was almost like my brain was saying, “Do we really need to get out all of our specialty tools just for this?” Guess what, we had to.
Making a curved piece of wood and, in this case, a nosing requires that all woodworking fundamentals be embedded in your blood cells. What do I mean by that? If you have no understanding of wood anatomy (wood cells, types and direction of grain, heartwood vs. sapwood…) and working with wood, you’re going to mess this up. So what do we need? Let me rephrase this: What tools did I use? (And you all know by now that I love tools…)
- Festool track saw
- Bosch heavy-duty plunge router (soft start … oh yes!)
- Template material
- All hand tools
- More tools
First, we need to make the riser. The owner is a retired contractor, so he framed that curve for me. You are probably thinking, “That curve was per Avi’s standards for sure”—NOT! So the curve was not at a right angle with the concrete slab, nor was it flowing in a smooth arc fashion. To compensate for the irregularities in the riser, I took a 5/16-inch solid red oak riser and scored the back side every ½ inch (1.27 cm). That not only gave me a more pliable riser but would guarantee a very continuous curve or bend regardless of the frame.
I would usually use my table saw sled for repetitive cuts, but this riser was 13 feet long. Unsafe and stupid is what I would call it if I had tried to use my table saw. Instead I made a quick jig:
I laid the riser on scrap plywood. I attached two wood pieces on each side to keep that riser in place. I positioned my track saw at a right angle and at the right depth, then marked my spacing on the wood and cut away. I would make one cut, then push the riser the ½-inch distance (which was marked on the jig) and make another cut. And repeat like a million times. It took about 15 minutes:
Next I needed to cut the riser to length. I used a piece of string to measure, and then I cut my riser longer. I went back and forth trimming each side until my cuts on both sides fit perfectly. Then I scribed the bottom of the riser to the concrete. (We are not discussing what scribing is right now.) The last step is to cut the top of the riser flush with the subfloor, apply some glue to compensate for the voids in the frame and attach the riser to the frame. Do not use a finish nail gun! Use a brad nailer or pin nailer:
I calculated that I would make the nosing out of three pieces. That meant three templates and three pieces of lumber (plus one extra, you’ll see later why). Now that the riser was secured and the glue dry I had a beautiful flowing double curve to work with. I cut and fit three pieces of HDF over the riser. I butted the HDF against the flooring for a reason. Easy positioning, easy does it. I marked the bottom of the HDF with a small jig I made which was 1¼ inch (3.175 cm) deep. That gave me the depth of the nose overhanging the riser.
Ask me if I remember the first curved nosing I made and how I forgot to compensate for the nose. It never happened! You know why? Because I always mark what I call an “idiot” line first. Let me explain: I marked the bottom of the HDF to follow the riser. Then I flipped the HDF over and roughly marked another line about 1¾ inch (4.445 cm) away. It is a raggedy, bad-looking line but it is there. I trimmed the template at the idiot line with my jig saw to make the actual marking for the nosing easier (less material overhanging while marking the template). By the way, the jig I made for marking the depth of the nosing was simply made from a piece of HDF holding a #2 pencil. That’s it. Now I had a smooth pencil line representing the edge of the nosing. I needed to create a smooth front curve on all three templates. The secret is working to a line, using a combination of tools and techniques. We’ll discuss this next time.