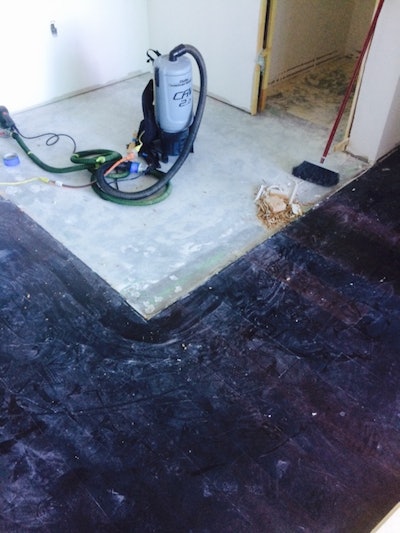
One of the general contractors I work with called me 10 months ago. He didn’t sound very happy. With a sigh he said, “Avi, we got that job in the city” (San Francisco). Why wasn’t he happy? Because the remodel was to take place on the 41st floor penthouse in one of the most luxurious towers in San Francisco. I shared his ambivalence. The consequences of a mistake on that job could cost anywhere from a lot of money to our entire businesses. Contractors working in that tower are required to fill out an application for the project, a drawing of the floor system and copies of their insurance, workers comp and license. The application then goes through a board approval to schedule the remodel. There is no parking. You can only make noise between 9 and 5. There is only one place to unload your tools and you have to reserve a time for that to happen weeks in advance. You also need to reserve a time for the service elevator. You sign in when you enter and sign out when you leave. They take your ID at the beginning of the day in exchange for the key to the unit and a sticker on your shirt that says “contractor.” The most important detail of all: There is no parking available within a mile, I’ve said that before. Let’s get to the floors:
There is only one place to unload your tools and you have to reserve a time for that to happen weeks in advance. You also need to reserve a time for the service elevator.
The floors in that unit were 5/8” x 5 13/16” (1.58 cm x 13.5125 cm) glued-down prefinished square-edge engineered wenge wood. I was called to bid on refinishing the floors and repairing multiple areas where walls were removed. I could not source the material in that width. I had to figure out a way to make it myself. The floors were glued down to a ¼” (.635 cm) cork for soundproofing, which was required in that building.
This is an area of the project that needed to be filled in/repaired before I could begin the sanding.
Then I would mill it myself. I’ve done it before when I had small repairs on solid floors. The hardwood lumber yard here has pallets of most woods, but only one or two pieces of wenge. I needed about 180 lineal feet of that material. Before we go into which material I needed to buy, let me walk you through the thought process of how to bid that job and, more importantly, how to repair that floor.
To bid this job I had to analyze what each factor meant:
• Wenge: It’s hard to source, machine, sand and tricky to finish. Very expensive. Limited sources. wenge is usually used as a decorative inlay, feature strip or part of a wood medallion feature, not an entire floor.
• Engineered: I only needed the veneer thickness of the wenge. The veneer was approximately 5/32” (3.9688 mm). How would I make the floor? I needed to lace into the existing floors. No manufacturer would set up to make me a few boxes of flooring.
• Glued down: How to remove the floors to make a nice repair? The floors were glued to cork, which was glued to concrete.
• Grain: Because this floor was engineered, the grain on the veneer was unique. It wasn’t sliced face nor sawn face. It seemed I had to mix flatsawn and riftsawn lumber. The color of the wood was dark. Some lumber yards had lighter looking wenge lumber that wouldn’t have worked for us (I found that out the hard way).
• 41st floor: Remember the article in HF about microclimates? Acclimation, acclimation and more acclimation.
• Parking (again): I had to get all my stuff together, load it when I had the time reserved and park the van far away. There was no “Oh, let me go back to the van to get the tape” kind of deal. If it is not up on the job site, you’re screwed.
Well, now that I got the job, I needed to figure out a schedule and execute the plan successfully. All about that in the next blog …