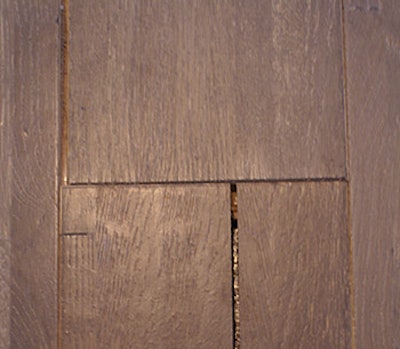
The Problem
The Procedure
The floor was purchased from a flooring chain by a builder, who hired a flooring contractor to install the product in a new home using the floating installation method. The product was 5/8-inch-thick white oak and was somewhat unusual in that it was a floating floor but had no plies; the boards were made up of solid pieces glued together at the sides. About 900 square feet was floated using the product's click system over a fir plywood subfloor in the kitchen, living room, dining room and home office. The builder said he had tested the subfloor for moisture, although no readings were recorded. Installation took place during summer, and problems did not appear until the heating season started.
The Cause
When I arrived, I could see the floor was starting to let loose from its click system. The problems were around the perimeter, near the kitchen island, under the fridge and over a heat duct. It was most noticable parallel to a heat duct and a heat register. My moisture readings of the wood averaged 7%, which would seem typical, and the RH was 39% that day. It was raining outside, which probaby elevated the interior RH on that particular day. The humidifier located on the furnace was set to 30%.
RELATED: Take Steps to Avoid Noise Complaints with Floating Floors
After documenting measurements and moisture readings, I waited until the supplier could forward the manufacturer's installation and warranty guidelines to me (these had not been mentioned in the first inspector's report). As inspectors, we always look at the manufacturer's guidelines before those of the National Wood Flooring Association since manufacturer guidelines supersede all others. Because the product was discontinued, it took almost two weeks to get the information emailed to me.
Like other products, this product would lose its warranty if guidelines were not followed. When I finally got the product guidelines, they were surprising: The minimum RH was 45% and the maximum was 60%. (The NWFA suggests 30% to 50% for a wood floor to perform best.) This product was installed in the Midwest, which is known for tremendous swings in RH. The high end of the RH in summer can be as high as Florida's, and during the winter the RH can get as low as it does in Utah. If this product required a RH range between 45% and 60% in order to perform, it was doomed to fail in this area. Since the builder had bought the product, he was responsible for the failure.
How to Fix the Floor
In the Future
This floor should never have been installed in this home, and it appears that it has subsequently been discontinued. Don't assume that manufacturers use the same guidelines as the NWFA. Many manufacturers have their own research and development and write installation guidelines based on their own research. Always, always check the manufacturer's guidelines and use the NWFA's "Installation Guidelines" as your backup.