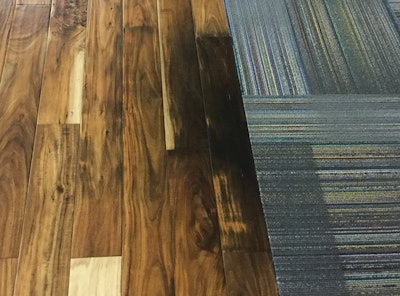
The Problem
A large church in Texas had engineered wood flooring installed in its roughly 2,000-square-foot entryway. Portions of the wood flooring began turning black just one year after the installation.
What Happened
The same area had demonstrated a similar issue with carpet in the past. A commercial contractor had informed the church that wood flooring would offer a solution if a concrete moisture control adhesive were utilized, so the carpet was replaced with wood flooring. A year later, the wood flooring started to discolor in seemingly random areas, in some places turning black.
The Inspection
Several areas of the installed wood flooring were very dark or black. Tests showed the site to be at 75 degrees Fahrenheit and 37% RH, and an invasive pin moisture meter showed that the discolored areas had MC readings upwards of 30%, while the non-affected areas had a normal range of 7-10% MC. In the discolored portions, the plank undersides had a much higher MC than their surfaces, indicating a moisture source existed below the floor.
The wood flooring installer informed the inspector that a premium combination sound and moisture control urethane adhesive was used. He opened two areas of the flooring installation, both directly over hollow sounding areas (these are ideal for inspection because they can show the exact notch and size of the trowel used). With those removed, the source of the problem revealed itself: an improper application of the adhesive. A square-notch trowel was used, despite the adhesive manufacturer specifying a V-notch trowel. More than half of the concrete was not covered with adhesive.
RELATED: Sticky Questions: Q&As on Essential Adhesive Know-How
How to Fix the Floor
In this scenario, the entire floor must be removed, the concrete subfloor must be thoroughly cleaned, and wood flooring should be reinstalled per specifications with a moisture mitigating adhesive. An alternative is the application of a two-part epoxy mitigating product on top of the concrete prior to spreading the adhesive.
In the Future
It is critical to conduct moisture testing on concrete substrates, particularly when replacing a floor with concrete moisture vapor damage. It is highly recommended to find out if there was a plastic vapor retarder installed under the concrete, history of damaged pipes, drainage running from the building, or sprinkler systems close to the foundation. This investigative work prior to installation can help prevent lost time, expensive repairs and a damaged reputation.