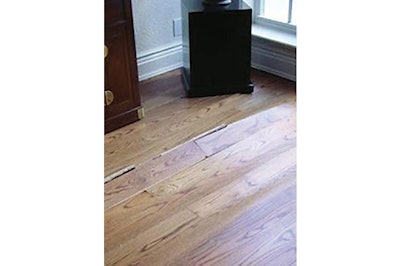
An old professor of mine once said, “95 percent of all problems that you will experience in wood in your career will be moisture-related in one way or another.” Thus far, he is correct. Regardless of your level of experience, there is one critical aspect that you must take into account in order to produce a claim-free wood flooring installation: control of the moisture content (MC).
This is the most critical aspect to properly manufacturing, installing or maintaining any wood-based product because wood is “hygroscopic.” Hygroscopic means “water loving,” and hygroscopic materials gain and lose moisture depending on the environment. When wood gains or loses moisture, it changes dimension. Dimensional change in solid and (to a lesser extent) engineered wood flooring can wreak havoc, and depending on the amount of dimensional change, defects such as buckling, gapping, checking, splitting, cupping and crowning can occur. It is important to understand a bit about the manufacturing process and how the ambient atmospheric conditions can affect wood flooring’s performance.
RELATED: Understand the Science of Water and Wood Floors
For example, most manufacturers produce solid and engineered wood flooring products going into the box with an MC of 6–9%. MC is defined as the weight of the water contained in the wood, expressed as a percentage of the weight of the dry wood. Wood products produced for interior applications in the U.S. and Canada are generally manufactured to hold the 5–9% MC range.
Generally speaking, those interior environments hold approximately that same atmospheric MC, also known as equilibrium moisture content (EMC), year-round. EMC is defined as the MC at which wood neither gains nor loses moisture when surrounded by air at a given relative humidity and temperature. In essence, when wood at a specific MC is placed into an environment that does not match its MC, the wood will gain or lose moisture until equilibrium with the environment is met. The result of this gain or loss in MC is dimensional change.
Most manufacturers require that wood flooring products be “acclimated” to the environment in which they are going to be installed. Improper acclimation typically results in gapping between boards (in drier conditions) and buckling or crushing (in wetter conditions). For example, if an installer fastens 3⁄4-inch-thick, 31⁄4-inch-wide Northern red oak (predominantly flatsawn) flooring with an average out-of-the-box MC of 6% in an interior atmosphere that has an 11% EMC without proper acclimation, he or she can expect approximately 4.4 inches of expansion in an installation 20 feet in width.
Nearly all of the dimensional change in wood flooring is across its width and through its thickness, with virtually no change along its length. Time exposure is a critical element that is rarely discussed when using this calculation. The calculated value of dimensional change does not take into account varying interior EMCs; therefore, the 4.4 inch total change in dimension is a worst-case scenario. Due to the short annual seasons in many temperate areas, only a percentage of the total calculated change is experienced with an installed hardwood floor.
No matter where you are or which product you’re installing, controlling moisture on every job site is critical to avoiding those 95 percent of wood floor problems.