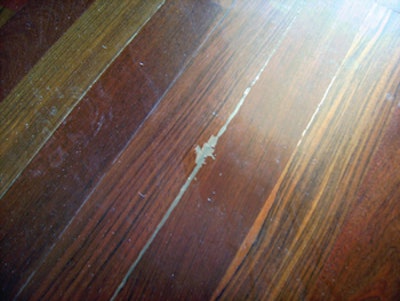
The wood flooring business doesn't have much in the way of conspiracy theories, but one finish problem is approaching that status. Rumors and buzz about it—and its causes-spread rapidly by word of mouth and even faster in the blogosphere. It's discussed so much, with so much wrath, that it has even earned a name that sounds like a disease: white line syndrome, or WLS for short.
The name is casually used any time white lines show up between boards in a wood floor. The reason it has earned its own moniker is that it seems to be so much more prevalent in recent years, particularly about the last five years. Some contractors who have never had issues with white lines before report suddenly having to redo floors, even though they're doing everything the exact same way-with the same products they always have used.
This has all led to suspicions directed at the finish manufacturers: They're changing product, using cheaper ingredients, messing up the finishes to comply with VOC laws, etc., etc. Contractors feel they are being thrown under the proverbial bus. But what really causes WLS? Is it truly a mysterious, misunderstood phenomenon lurking on your next job?
Types of WLS
The first question is: What, exactly, is WLS?
Not all finish experts agree on the terminology. Some use "WLS" to describe any time any sort of white lines show up between boards. Others make a distinction between what they consider to be "real" WLS—finish stretching between boards—and white lines that result from peeling finish. They do agree on this: Whatever you call it, the vast majority of calls they receive from customers saying they have WLS are actually about finish peeling at board edges.
Peeling Problems
Peeling described as WLS manifests itself along board edges, usually with oil-modified urethane (OMU) finishes. As the finish begins to lose adhesion and peel, it turns white in an irregular pattern that roughly follows the board edges (but isn't an exact straight line) and often overlaps the top of the board slightly.
Why does peeling show up in this pattern? One answer has to do with abrasion, or lack thereof. OMU typically doesn't stick well to itself—it needs a good mechanical scratch, or abrasion, in order to bond well with the next finish coat. If the floor isn't abraded well enough between coats—as often happens when you're afraid of creating swirl marks or cutting through the finish to bare wood—the finish won't bond well, especially along lower-lying areas of the floor. (As one finish manufacturer put it, "It's stuck, but it's not stuck well enough!")
Once the finish has cured and people are walking on it, and the floor goes through seasonal movement (particularly in areas with a great variation in humidity), the places in the finish stressed the most are those where the finish has bridged between the boards. The foot traffic and seasonal movement stress the finish to the point where it releases from the finish below (which wasn't bonded well enough to start with), and white areas of peeling finish begin to appear. If you use a microscope to look at the finish underneath the peeling coat, you'll see that there isn't enough of a scratch pattern to create good adhesion of the next coat of finish.
This problem is much more common in situations when there is more than just a day of dry time between coats of OMU. For example, say you applied everything but the final coat of OMU on a floor in a kitchen, and then the cabinet guys installed the cabinets and the painter was doing touch-ups. It was a couple weeks before you applied the final coat, and now the poly had a chance to cure much harder than it would have over just a day or two. You'll need to abrade extremely carefully—until the finish is completely dulled down—to ensure good adhesion of the next coat.
Many contractors go far beyond a worn screen to abrade between coats of OMU. One technique is to screen the floor, then come back with a pad and strip system to make sure you hit the lower areas in the floor. Most importantly, after you think you are done abrading between coats, clean the floor and take a careful look to see if there is any visible shine difference remaining (see the sidebar "Lying Low" below). If you see any areas that are shinier than others—board edges are a common problem spot—you may need to complete abrasion by hand until all the finish is dulled down.
Peeling from Solvents
Another problem that can result in white lines between boards occurs with stain or solvent-based sealers: When they haven't dried well enough before the finish coats, or too much stain or sealer has seeped between boards, solvents trying to evaporate through the topcoats can cause the floor to take on a WLS appearance. On recoats, the problem can be made worse by wax and/or maintenance products between boards that react with the new finish.
WLS from Stretched Finish
Far less common than white lines from peeling is what some manufacturers refer to as "real" WLS. This happens when the finish stretches over a gap that develops when wood flooring boards contract. Just like a black garbage bag stretched too far, stretched areas of finish over the gaps turn white. The white areas are perfectly even, straight lines directly over the gaps.
Because the white lines are a direct result of the finish's tendency to stretch instead of fracture over a gap, the finish's flexibility can be a good predictor of potential for WLS. In general, this appears to be more common with waterborne finishes, which are the most flexible, but it also can happen with recently applied OMU. It is uncommon with other finish types and unheard of with finishes such as oil and wax. Because the composition of waterborne finishes varies widely, some may have a greater tendency to develop WLS than others.
Preventing Stretching
Manufacturers stress that acclimating your wood floor, and then ensuring the customer uses good climate control year-round, are the most important steps you can take to minimize WLS from stretched finish. If the floor doesn't move, the finish won't stretch and create the lines.
But what does acclimation really mean? The floor should be at a moisture level close to the midpoint of the moisture content (MC) it will have year-round. If you're installing a walnut strip floor in Ohio in August, the MC of the floor and the subfloor may be within 4 points of each other, but they are probably at their year-round peak, and that floor is likely to shrink substantially come wintertime, especially if the customer doesn't maintain reasonable humidity levels in the home.
Also, a floor with loose end matches and/or fasteners too far from end joints can cause movement in the floor that stretches the finish.
Additionally, not all finish experts agree, but some believe that using a thicker-than-recommended spread rate may increase the likelihood of WLS.
As always, customer education can go a long way toward minimizing this problem. If you think WLS might be a problem, let the customer know that there is a potential for white lines to appear between boards—at least one contractor actually writes it into his contract. Make sure the customer knows about proper maintenance procedures. Wet-mopping the floor, for example, will wreak havoc on MC levels.
If calls about WLS from stretched finish do occur, sometimes waiting for the floor to go through a full cycle of seasons can lead to an acceptable appearance. Another option is to use a razor knife to cut down the finish at the seams, then buff and recoat.
Why Is It Happening Now?
This all doesn't answer the question of why it seems like suddenly everybody is talking about WLS. The blogosphere commonly cites VOC changes and finish manufacturers changing their products to use different resins. But the resins being used in VOC-compliant wood flooring finish have been used for years, and while finish manufacturers do often change their products, they say WLS also happens on products that basically haven't changed in decades. VOC-compliant OMU products are thicker than previous versions, with more solids, so it's possible that longer dry times with those products are making WLS more likely. The reasoning goes that instead of the finish drying and breaking right away, it's flexible for a longer amount of time while it's still curing, creating a chance for WLS to occur.
One important factor everyone can agree on is a change in consumers' preferences. Trends in recent years toward exotic floors, dark floors and plank floors all make WLS more visible. A white line between boards may not even be noticeable on a maple floor, but it will be front and center on a walnut, padauk or dark-stained floor. Plank flooring expands and contracts more than strip, stretching the finish more, and many exotic species are also known for their volatile expansion and contraction on the job site.
Today's more urgent job sites also may play into WLS. In the olden days, wood floors were installed and sat on a job site for a while before they were sanded and finished. Today, jobs tend to be more rushed than ever, and the wood may still be settling in—in particular, shrinking—while the finish is still flexible and drying.
Finally, customers' expectations are ever-increasing. As they become more demanding, fewer imperfections are seen as normal, making life more difficult for everyone.
WLS may never totally lose its mystique—and every single case of WLS may not always have an easy explanation—but hopefully by taking the right steps, you can reduce your potential for catching this dreaded disease.
|
Lying LowWhen abrading between coats of oil-modified polyurethane, make sure all areas of the floor, especially low areas at board edges, have been abraded well enough. Below, sheen differences at some of the board edges show where the abrasive didn't hit low spots enough. If not abraded further, these areas could be prone to peeling that looks like white line syndrome. |
Avoiding WLSThere's no guarantee, but keep these tips in mind:
|
Sources and reviewers for this article included: Johannes Boonstra, Synteko Floor Finishes; Paul Campbell, Glitsa American; Steve Crawford, Dura Seal; David Folkman, Basic Coatings; Bill Jauernig, PoloPlaz; Todd Schutte, Bona US; and Janet Sullivan, Lenmar.
Join the conversation about White Line Syndrome in the WFB Forum.