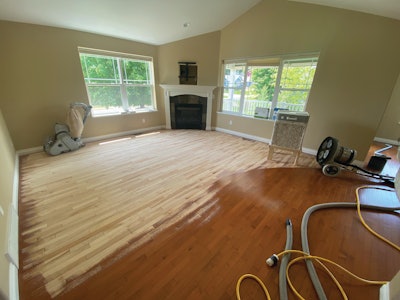
Some of us remember the first time we had to “try” sanding off a finish with aluminum oxide (AO) or ceramic finish. You put a new belt on your big machine, most likely a black one, and started your first pass. The sander seemed to float over the surface, leaving topical scratches and not removing anything. This was a WTF moment (What’s This Finish?)! That’s when it hit you: You were trying to remove AO with a belt made of AO. It became a short day, leaving time to ponder what to do over a beer.
Luckily for us, the abrasive industry was at work taking abrasives used in metalwork and bringing them over to the wood sanding world. The newer abrasives are made with ceramics, some as hard as industrial diamonds. Some products are a mixture of silicon carbide and ceramic; others are pure ceramics. There is a learning curve as to the shape of the grain and what grit to start with. Major machine manufacturers are now introducing diamond discs for use with their multi-disc equipment.
RELATED: Wood Floor Sanding 101, Part 1
So, how does this translate to your work in the field? Here are my top two tips:
1) The fastest method isn’t always the best. The newer diamond discs will quickly cut through a finish of any kind, right down to the wood. That is the upside—it is fast. The downside is that they can leave rather deep scratches. This may be a problem depending on whether you are sanding a floor with a thick wear layer (no problem), whether the floor has been sanded before, or whether it is an engineered floor with a thin veneer. Remember, our job is simple: We put scratches in the wood to get it flat or remove the finish. The rest of the job is removing the scratches we put in. So, even though the diamond discs are great in some cases, they can create grief in others.
2) Currently, the most common option is sanding with ceramic belts or rolls. The “trick” of the trade is to speed-sand with a higher grit, say 80, to break up the finish. The next pass is with a more aggressive grit to remove the finish. Try using the highest grit possible to efficiently remove the finish without leaving deep scratches. For example, if you break the bond by speed-sanding with 80, try 40 or 50 for the next cut. There is no reason to go straight to a 24 or 36.
One last note: Some of you are going to ask about using silicone carbide belts or rolls. They will cut the tougher coatings; the problem is they wear out quickly compared with ceramic grain in abrasives. Don’t be penny-wise and pound-foolish. Time is money, and trying to save a few dollars by buying cheaper abrasives will cost you in the long run.
RELATED: Recoating Wood Flooring 101
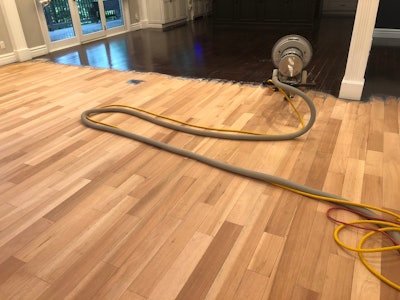