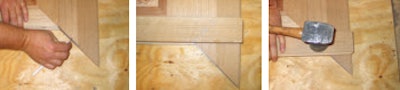
Hooked on Orbital
I just put stain on a floor I sanded and about every 20 feet it looks like there are hook marks. Is there something wrong with the random orbital sanding machine I used?
Jeff Marcum, who works in sales at Indiana, Pa.-based Cherryhill Manufacturing Corp., answers:
Because random orbital sanders can sand in any direction over any pattern, a lot of people think the machines are exempt from the natural laws of sanding. With a regular big machine, everyone knows to move in a standard pattern with an overlap. With an orbital sander, though, I’ve seen guys start sanding correctly and then get distracted by a medallion, for example. They do a 90-degree turn to start sanding it. When they’re done with the medallion, they move over to some other part of the floor. So these guys are moving all over the field, and it’s difficult for them to see where they’ve already sanded.
Most likely, at some point during the sanding sequence, they’re leaving parts of the floor unsanded. As they move up grits in the sanding sequence, if they miss a spot that was sanded before, they aren’t going to take out the scratches from the previous grit, and those spots can result in those hook marks. Many times, these scratches don’t show up until the stain goes on.
So, treat random orbital sanders as you would any other big machine. Sand the length of the floor, moving over 3 to 4 inches at a time across the floor, and you should avoid this problem in the future.
Formaldehyde Fears
I have customers asking about formaldehyde in wood flooring, but I don’t know what to tell them. What should I know?
Jack Racine, director of technical services for Medley, Fla.-based flooring manufacturer BR-111, answers:
Most engineered flooring has “urea-formaldehyde” in the bonding agents used during the laminating process.
Products with no added urea-formaldehyde (some formaldehyde occurs naturally in wood products) are required for the clean air credit in the U.S. Green Building Council’s LEED green building program; I imagine manufacturers will be offering more products that qualify. Meanwhile, the California Air Resources Board (CARB) is setting a new standard for formaldehyde emissions that it says will be the strictest in the world. The limit for “veneer core hardwood plywood” (including engineered wood flooring) will be 0.08 ppm (parts per million)as of January 2009 and 0.05 ppm as of January 2010. Manufacturers must have their products tested according to specified ASTM standards.
The test results I’ve seen have levels at or less than 0.02 ppm. You should be able to obtain these results from the manufacturer if testing was done. The 0.02 ppm result is really good; although formaldehyde is present, the emissions are almost undetectable and of little concern, if any.
Steamy Sanding?
Somebody told me I should take moisture content and relative humidity readings before and during the sanding process, but I thought I only had to worry about humidity once I’m applying finish. Who’s right?
Greg Mihaich, product engineer at Sanborn, N.Y.-based Norton Abrasives, answers:
You need to be aware of humidity and moisture content (MC) throughout the entire flooring process—prior to installation all the way through the final finish coat. Most contractors know to check humidity and MC before installation starts to see if the flooring is properly acclimated. However, they do not continue to monitor the job site after that. Problems can arise during and after the sanding and finishing process, especially if the floor was left unfinished for weeks or months so other trades could complete their work. In that time, your floor installed at the proper MC could have seen big changes in humidity. If a floor picks up extra moisture and swells after installation, causing some cupping, and the floor is then sanded and finished, it will likely crown after it dries out.
Most contractors know that extra moisture can affect the dry times and performance of finishes, but they don’t know that sandpaper is also affected by moisture. The majority of products available in the wood flooring industry use either a paper or cloth backing, and these materials are hygroscopic, just like wood (abrasives with a polyester backing are not). Sanding belts are most affected by this. A belt may expand or contract due to excessive moisture or lack thereof, but it won’t expand or contract along the splice, where the belt is joined. This can cause buckling in the belt, which in turn can cause vibrations in the sander, leading to chatter marks in the finished floor. To be safe, sandpaper should be stored in the boxes it came in and away from excessive moisture.
Trick of the Trade: The Right Angle
By Jim Schumacher
Getting the right miter is one of the most time-consuming parts of doing a custom install, even if it's just a picture-frame around a dining room or fireplace. This quick trick can make it less frustrating when you have a tricky angle: Scrape a pencil back and forth on top of the cut board, align the board to be cut on top and hit it with (the rubber side of) a mallet. The lead will transfer the exact miter onto the board to be cut.