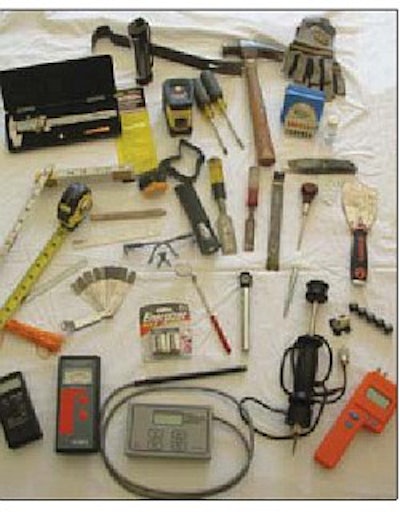
The National Wood Flooring Association Certified Professionals (NWFACP) currently offers four certifications: Installation, Sand & Finish, Sales Counselor and Wood Flooring Inspector. It's somewhat ironic that the goal of the first three certifications is to educate people well enough so the last one isn't necessary. But, in the wood flooring industry, inspections are a fact of life, and if you're in the business long enough, chances are one of your floors will end up being inspected.
Flooring inspectors, especially those not specifically trained for wood flooring, are a dime a dozen these days. If you need to hire an inspector, you'll greatly increase your chances of getting an accurate, professional inspection if you hire someone certified by the NWFA, NOFMA or the Institute of Inspection, Cleaning and Restoration Certification (IICRC). Those inspectors have taken tests to demonstrate their knowledge, and many have been through inspection-specific training.
Certification is no guarantee of a good inspection, but it's a start. Keep the following expectations in mind when you need an inspector, or when you're being inspected.
Ethical Guidelines
Some wood flooring inspectors are also contractors themselves. That is fine, as long as the two businesses never mix. For example, it is a conflict of interest for an inspector to perform an inspection and then also bid on the work to fix the job. Likewise, the inspector should never disparage anyone involved with the job, whether it's another inspector, the contractor or the supplier of the materials.
During the actual inspection, the inspector should gather information from the people involved, but should not share his or her theories or conclusions about why the floor went wrong with those present. It can be an intimidating situation when several parties in the dispute are present during the inspection, especially when tensions are running high. Inspectors should emphasize that they are on the job only to gather facts, not to assign blame on the spot. Conclusions should be included only in the inspection report. Once the report is done, it should be sent only to the party that commissioned the report.
Things to Keep in Mind
There are no standard procedures that should be followed on every inspection because the steps depend on the problem. For example, an inspection for peeling finish will be very different from an inspection for a buckled floor. In general, though, there are certain things to look for (and some to avoid). Some hallmarks of good inspectors are:
• They listen more than they talk. Inspectors should have little to say except for asking questions, and they must avoid thinking out loud (a certain amount of tact is required).
• They follow the basic ethics standards for inspectors.
• They verify the accuracy of the claim history.
• They take the time to discover what the flooring and subfloor really are, as opposed to taking someone's word for it (particularly the homeowner's).
• They are familiar with the specific geographical area and its construction methods, and how both can affect the job (especially where moisture is concerned).
• They try to interview every party involved.
Red flags during inspections include:
• The inspector seems biased toward the person paying for the report.
• The inspector seems to already have a preconceived idea of what the cause of the problem is before he or she has started the inspection.
• The inspection is extremely brief.
• The inspector criticizes any or all of the companies or people involved with the floor.
Good Reporting
A good inspection report should be clear and concise, without extraneous or irrelevant details. Other professionals will be examining what is written, and the report could be used in court. Reports should not be rushed; the timeframe for completing the report after the inspection should be agreed on before the inspector is hired.
Pressure to turn a report around in a rush will make most inspectors turn down the job. Good reports should include the following:
• The inspector's name, type of certification and certification number.
• The inspection date.
• A clear statement of the problem for which the inspection was commissioned.
• A physical description of the floor and job site.
• A comprehensive claims history of the floor so far, including a clear timeline of when everything occurred.
• The information gathered from interviewing the relevant parties. (For people who cannot be reached, the report should include their names, as well as when and how many times the inspector tried to contact them.)
• A description of all testing procedures and results, including specifics as to models and brands of testing instruments such as moisture meters.
• The inspector's observations, including specific citations for all relevant technical information supporting the findings (such as manufacturers' instructions, industry publications such as the NWFA Installation Guidelines, etc.). When publications are cited, the chapters, page numbers, etc., should be noted. Photocopies with the relevant pages of the publications should be included to avoid the risk of publications being quoted incorrectly. When there is a conflict, manufacturers' directions always take precedence over general industry guidelines.
Inspection reports should not include the following:
• The inspector's subjective opinions (not based on objective findings).
• Recommended corrective actions, unless contracted to do so. (Some state laws may require that inspectors recommend corrective action.) Recommending corrective actions can even open the inspector up to liability.
• "Accepted industry standards" that cannot be referenced in writing. Generalizations that have developed over the years about what is acceptable are baseless if they can't be supported by a written publication. I've read reports that make vague statements like "I'd rate this installation a four out of five." Four out of five what? Based on what?
• Any observations or statements not directly related to the problem for which the inspection was commissioned. Additional problems unrelated to the cause for the inspection should not be included in the report. For example, when the inspection is due to a finish problem, the report should not comment on the quality of the installation (racking problems, etc.).
• Standards that are unrelated to the floor being inspected, or standards that aren't even specific to the wood flooring industry. I have seen reports where the inspector quoted lumber grades, which have nothing to do with flooring. Even standards that are specific to wood flooring, such as NOFMA grades, are only applicable to the inspection if the flooring came from a NOFMA-certified mill. I once consulted on a case where the complaint was about the gaps being too big around the perimeter of the floor. The inspector who looked at the floor quoted standards saying that the floor required 4 inches of expansion. As it turned out, he had quoted directions for a basketball court—directions completely unrelated to the floor inspected.
• Assignment of blame where none should exist. An inspection may conclude that everything was done correctly.
• Statements unrelated to the floor at all. I once read an inspection report that stated, "Get rid of the dog." Of course, this is just ridiculous.
Legal Details
It is the inspector's legal and ethical obligation to report the truth in the inspection report. Oftentimes the party that hired the inspector is hoping the inspector will have something to say to win the case, but that isn't the inspector's job. The inspector's job is to relay factual information, even if it is adverse to the client. Also, if the inspector is unsure of something, he should be willing to say that, too.
When an inspection report is finalized and sent to the client, it becomes a legal document and may be used as evidence in court. If the report contains erroneous information, the inspector may suffer consequences. If the inspector is certified, he may lose his certification. The laws vary depending on the state, but he also may be sued for damages and/ or lawyer fees depending on what happened as a result of his report. To protect inspectors from this, inspectors should carry professional liability "errors and omissions" insurance coverage, which is not provided in a commercial general liability policy. Inspectors also should check the laws in the specific area where the inspection takes place—requirements for inspectors can vary among local and state laws.
Note that an inspection fee is for the inspection only. Things like court appearances and depositions are not included in the price of an inspection. All inspectors should have a list of services available for an additional cost printed on their letterhead so clients are clear on that policy.
As much as we don't like it, conflict and the resulting inspections are a part of today's wood flooring industry. I hope this information gives you a good idea of what to expect from a professional wood flooring inspection.
A Spirit of Cooperation
No matter which side of a dispute you're on—whether you hired the inspector or not—please cooperate fully with the inspector. People often try to avoid inspectors, but inspectors aren't out to get anybody. They're just trying to uncover the facts. Chances of an accurate inspection increase when everyone fully cooperates with the inspector. —D.C.