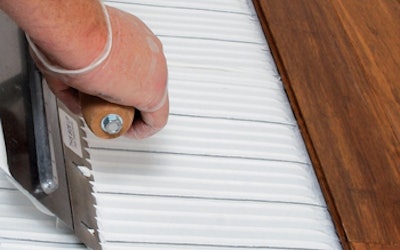
Cris Bierschank, LEED Green Associate, at MAPEI Corp., answers:
In order to achieve "low odor" wood adhesives without compromising installation performance, the adhesives industry had to re-think its formulations, substituting plant-based polymer materials for petroleum-based ingredients, eliminating the need for isocyanates, phthalate plasticizers or epoxy resins.
As an installer you might wonder how these reformulated wood adhesives stack up to "tried and true" solvent-based adhesives. Depending on the formulation, these newer hybrid polymer adhesives can actually perform equally well and in some cases better than solvent-based products. Some things to know about using them include:
- When formulated without water, they do not introduce additional moisture that can cause dimensional changes to wood.
- They are easy to spread with strong green-grab for fast installations.
- Typically no "flash time" is required, so the installer can start immediately, with working times of typically 45 to 60 minutes and adjustment time of typically two to three hours.
- Many offer both moisture (MVER, or Moisture Vapor Emission Rate) and sound (STC & IIC) reduction when the adhesive is used as a continuous, homogenous membrane.
- Most can be used with all types of solid hardwood and exotic planks or shorts, parquet, bamboo, acrylic-impregnated wood, cork, engineered wood flooring, laminate and tile or stone in mixed media installations.
- For combination adhesive/sound reduction/moisture reduction products, all your eggs are in one basket, so to speak-you have one shot to get a uniform layer on the concrete to mitigate moisture and sound. If there are any gaps in the product, the floor may still be sufficiently glued down, but the membrane is compromised and won't offer protection.
- Since you are creating a membrane, unlike using it as an adhesive, if you stop for the day, you need to extend the product flat-troweled as a membrane (no ridges), beyond the last board. This will ensure that the membrane is continuous, without dried glue ridges, and that there is no "break" in the membrane.
As always, consult both the wood flooring and adhesive manufacturer's most current technical data sheet and recommendations.
RELATED: Sticky Questions: Q&As on Essential Adhesive Know-How
Engineered Shrink/Swell?
I use dimensional change coefficients to calculate shrink and swell when working with solid wood floors. But what do I use for engineered flooring?
Howard Brickman at Norwell, Mass.-based Brickman Consulting, answers:
When working with engineered products, 0.5% to 0.3% is the commonly used shrink/swell factor. It is comparable to using 8% tangential and 4% radial for solids.
For example, a 10-inch-wide solid tangential board (plainsawn) would shrink a total of 0.8 inch from fiber saturation point (FSP is 28% moisture content) to oven dry (OD is 0% MC). A 10-inch-wide solid radial board (quartersawn) would shrink 0.4 inch, while a 10-inch-wide engineered piece would shrink 0.05 inch. Of course, the shrinkage during "normal" seasonal variation of RH and MC would be proportionally much less. In the Northeastern U.S. it is not unusual to have a seasonal MC change from a low of 5% in the winter to a high of 10% in the summer. Since changes in dimension and MC are linear or constant (this means that each 1% change in MC yields an equal amount of dimensional change), we can predict the amount of shrink or swell based on the size of the individual board, orientation of annual growth rings and species.
Let's look at Northern hard maple (Acer saccharum) as a solid wood and as an engineered wood. We go to the "Wood Handbook" Chapter 4, Table 4-3 "Shrinkage Values of Domestic Woods" to get the tangential shrinkage factor of 9.9% and radial factor of 4.9% for solid hard maple lumber. With solid wood, we use a longitudinal shrinkage factor of 0.01%. If we were to use hard maple veneers to make hard maple plywood, we would use a multi-directional shrinkage factor of 0.5%. We have three pieces of maple flooring all exactly ¾ inch thick by 5 inches wide by 50 inches long at the time of manufacture.
If we do the correct calculations, the plainsawn solid board would shrink 0.088 inch in width and 0.009 in length, the quartersawn solid board would shrink 0.044 inch in width and 0.009 in length, and the engineered board would shrink 0.0045 inch in width and 0.045 in length. For more detailed info and calculations, see the additional WFB online content below.
RELATED: Limit Your Liability: Avoid Moisture-Related Claims on Wood Floors
To continue our discussion about comparing shrink and swell of solid and engineered wood floors, let's take a detailed look at our three products:
We have three pieces of maple flooring all exactly ¾ inch thick by 5 inches wide by 50 inches long at the time of manufacture:
#1 is plainsawn (tangential) solid#2 is quartersawn (radial) solid#3 is engineered (plywood made from alternating layers of maple veneer)
Consulting our Wood Handbook (the PDF is available free here), we can come up with these numbers:
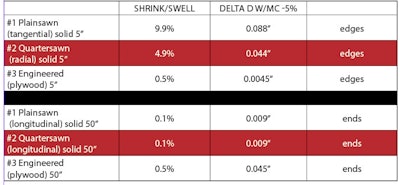
You can see that engineered flooring would show a minimal amount of displacement along the edges but would have shrinkage of over 1/32" at the ends. Conversely, solid flooring would have shrinkage of over 3/64" along the edges with minimal displacement at the ends. It might be helpful to know that the original "engineered" wood flooring was 9" x 9" square parquet made from three plies of ?" thick hardwood veneer. When engineered plank (then called "laminated") was first introduced more than 40 years ago, the lengths were limited to 42". Of course, the marketing department got so many complaints that the lengths were increased.
Let's have a go at the formula for computing dimensional change when wood changes MC:
?D = Dinitial x [(Sfactor/.28) x (MCfinal - MCinitial)]
This is based on the formula found in the "Wood Handbook" Chapter 13, pages 13-15, but I have modified it to make the source for the shrinkage factor more transparent. Normally shrinkage factors are published as the shrinkage from fiber saturation point (FSP) to oven dry (OD). For most species FSP = 28%, which is equivalent to the decimal number .28. By inserting .28, the formula now compensates for each 1% change in MC. Now we take this sleek new formula on a quick test drive using the solid plainsawn maple flooring ¾" x 5" x 50" numbers.
?D = Dinitial5" x [(Sfactor.099/.28) x (MCfinal.10 - MCinitial.05)] ?D = 5 x [(.099/.28) x (.10-.05)] ?D = 5 x [(.35357) x (.05)] ?D = 5 x [.017679] ?D = 0.088"
How about another quick spin around the block? Another application would be to see how a sheet of plywood subfloor changes dimension when it changes MC. The scenario is 4'(48") x 8'(96") SYP plywood that comes to the job at a MC of 6%, then acclimates to a job site MC of 12%. How much does the plywood change dimension? Plywood is engineered with a shrinkage factor of .5%, or 0.005.
?D = Dinitial96" x [(Sfactor 0.005/0.28) x (MCfinal 0.12 - MCinitial 0.06)] ?D = 96 x [(.005/.28) x (.12-.06)] ?D = 96 x [(.018) x (.06)] ?D = 96 x [.00108] ?D = 0.104", which is a little less ?" (.125")
Understanding this fundamental relationship between MC and ?D is critical to being able to analyze things that happen to wooden buildings and wooden components in concrete and steel buildings. The failure to master fundamentals directs you toward the path to failure.