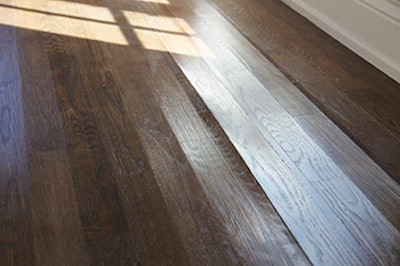
Everyone who works with wood floors knows that most complaints are caused by moisture problems. Keeping track of the moisture content (MC) through the various steps of kiln drying, milling, storage and installation is essential for successful floors. No one wants to get a call that the floor is lifting up the furniture. I have seen high-end floors worth many thousands of dollars fail and need to be replaced. Some of these situations could have been avoided if moisture readings had been taken in advance. Once something has gone wrong, measuring MC can be critical in diagnosing the problem in order to develop the proper corrective course of action. No matter which stage a job is at, knowing how to determine MC accurately is vital when dealing with wood floors.
Why We Measure MC
Wood shrinks and swells as the MC changes below the fiber saturation point (FSP), which is typically 27% to 30%. Knowledge of the MC of wood flooring allows us to predict how it will change in size as conditions change in the future. It is important to measure the MC of wood flooring before a wood floor installation begins, because flooring should be installed at a MC very close to what it will be during service-in typical living conditions-to avoid problems caused by shrinking or swelling.
RELATED: Avoid These Mistakes When Moisture Testing Wood Floors
Knowing your MC has many other practical uses on a wood flooring job site. At elevated moisture levels, around 17% to 19% MC, mold or decay can set in. Problems can also arise if flooring is too dry when installed and later swells when it acclimates to the local climatic conditions. (The amount of field expansion that is needed to avoid this problem can be calculated from the expected MC increase and the coefficient of swelling for the species.) Measuring the MC can also be a diagnostic tool to determine the cause of a floor failure due to water introduced from below the floor. Following the MC of a floor that has been flooded as it dries determines when repair steps should be undertaken and what should be done, and it can help avoid the problem of sanding a cupped floor prematurely (before it has fully dried), which can lead to crowning.
The Oven-Dry Method
In the most basic method of measuring MC in wood, a piece of wood's weight is first recorded. Then the water is removed by placing the piece of wood in an oven (at approximately 103 degrees Celsius, which is about 217 degrees Fahrenheit), and finally the piece is weighed once all the water has been removed. The difference between the initial and final weights divided by the final weight gives the initial MC.
One advantage of this method is that usually determination of MC is not dependent on knowing the species of wood. This process, although not difficult, usually takes 24 hours or longer and alters the wood, so oven testing is not used in most circumstances. Some dry kiln operations do still use this method. Note that if a species contains significant levels of volatiles other than water, the oven dry method does not give an accurate MC; such species include those with high resin content or oils, such as Eastern red cedar.
I have used a microwave oven to determine the MC of smaller pieces of flooring. This process is quicker than a standard oven-drying and is less accurate but can still be useful. Some years ago during my days as a contractor, we were asked to install wide dense flooring that had been purchased directly by the customer from an importer. It was sold as kiln-dried flooring. Although the flooring was given an attractive, descriptive name, the species was not known. Drying samples in a microwave oven indicated the MC was at least 16%. Needless to say, we declined the job.
Since oven-drying isn't practical in day-to-day life, meters were developed that measure the water in wood indirectly. Most meters measure an electrical property of the wood, which changes as the MC changes. The meters are then calibrated to read the equivalent MC. Inaccuracy in readings can be introduced if factors other than the MC change the property that the meter measures. The two common types of electric moisture meters measure the resistance or the dielectric properties of wood.
Pin meters correlate electrical resistance in wood to moisture content; this graph indicates that a small percentage increase in MC in wood results in a significant decrease in electrical resistance.
How Pin Meters Work
Pin meters measure the electrical resistance of the wood, which has been correlated to the MC. To use this type of meter, the user drives two or more metal pins into the wood. The meter then creates a voltage difference between the pins, which causes a small current to flow. The ratio of the voltage to current is the resistance.
As wood gets dryer, its resistance increases greatly (see the graph on this page). The extremely high resistivity of dry wood limits the lower end of the MC range of these meters to about 6%. On the high end of the moisture scale, readings above the FSP tend to be unreliable. Fortunately the high readings are not commonly encountered in flooring installations.
Most meters produced for the North American market should be used with the pins oriented along the grain (longitudinally). Follow the manufacturer's instructions for accurate results. Stay away from knots, cracks and decayed sections while taking readings. Pins should not be loose in the wood but firmly embedded when the readings are taken because a loose fit has a high contact resistance, which distorts the reading. Typically 5/16-inch pins driven to full depth are designed to measure ¾-inch-thick wood.
Proficiency in obtaining good readings comes with practice, and experience also increases your ability to interpret readings in a useful way. When I have a new meter, I like to take a whole series of readings, including several measurements along the same board. These results are then compared with the same measurements taken with a meter that has been used in the past.
All wood species do not have the same resistance characteristics, and the resistance changes slightly with temperature. Douglas fir at 70 degrees Fahrenheit is a common calibration for North American meters, so a correction needs to be applied for other species and temperatures. Tables are available for manual corrections, and some digital meters allow you to set the species and temperature for automatic corrections.
Do Your Readings Make Sense?
As with most things, think about your results to see if they make good sense. I have seen low measurements reported when a meter was inadvertently set for a temperature scale of Celsius rather than Fahrenheit. The 4-5% error resulted in a floor failure because the flooring was too wet and later shrank. Luckily it was only an overlooked stair landing, so the replacement cost was small, but the same error could have happened to an entire house.
RELATED: Understand the Science of Water and Wood Floors
An external standard calibrator should be used to verify that a meter is working correctly even if it has an internal check. Standards are usually available from the meter manufacturer. Touch the pins to the contact points of the standard, and the meter should give the value indicated.
No one should be surprised that condensation needs to be avoided on moisture meters and probes. When non-insulated pins are used, the meter reading will reflect the wettest layer of the wood penetrated by the pins. This result is due to the strong decrease in resistance with increasing MC mentioned earlier. With non-insulated pins, a piece of wood that has a thin wet layer on the outside will give a high moisture reading. The same piece of wood measured with insulated pins would show a wet shell and dryer core. In some species, the sap wood and heart wood can measure a different MC in the same board.
Insulated pins and a hammer electrode can be used to measure MC at different depths through a board. This series of measurements can determine if a moisture gradient exists in wood. Longer pins can also be driven through the flooring into a wooden subfloor to check for a gradient there. Detecting a moisture gradient is useful because it can help identify the source of excess moisture causing a floor problem.
A pin meter is inserted in flooring ready to take a reading; note that a reference standard to check accuracy of the meter readings is shown on the right.
Pinless Meter Tips
The second type of meters, pinless meters, measure an electrical capacitance property or the dielectric constant of the wood. They have the advantages of being easy to use (especially for quick surveys), not damaging the finish, and having very low sensitivity to temperature.
Some things to note when using them are that these meters can be designed to measure to a specified depth, and that the readings will be affected by material that is behind thinner boards. To make sure you have accurate results when using meters with a large contact surface, you must have a flat wood surface. The readings of pinless meters are affected by the density of the material they measure. Tables are available for species corrections, and some digital meters allow you to enter the species for automatic correction. Natural density variations from board to board or even along a single board will cause different readings. If the load of wood varies in density from the species average used to develop the tables, the moisture readings will be off.
Here's a hammer electrode with insulated pins inserted a short distance into the wood. (Photo by David Gonzalez)
High resin or other extractive content can give skewed moisture readings (again, caused by density variation). Care should be exercised, as with any other measurement of a natural material, and a small number of readings cannot be relied on.
External calibration blocks are available for some pinless meters to verify that they are working correctly. For critical measurements, check the calibration both just before and just after the readings are taken.
No Matter Which You Use
I recommend to typically take 20 or more readings when testing wood flooring prior to installation, and do not forget to check the subfloor MC in several locations. As a natural material, wood varies some from piece to piece, and a larger number of readings will give a more accurate representation of how the floor will perform once it is installed.
This pinless meter is shown with a calibration block that verifies the meter is working correctly on the right. The preferred direction with this moisture meter model is across the grain.
If readings before installation vary significantly, this may be an indication of improper drying or storage conditions, which could lead to an unsatisfactory floor. Keep in mind that some preservatives or glue in manufactured subfloor materials (plywood or OSB) can affect meter readings. Also, boards lose and gain moisture more quickly at the ends, so measurements should be taken at least a few inches in from the board ends.
Different meters will sometimes disagree when measuring the same spot on a piece of wood. My experience is that a quality meter manufactured by a company that provides good support is well worthwhile. As a general rule, readings are not accurate to better than one percent despite the fact that some meters read to a tenth of a percent. I have a personal preference for analog meters for diagnostic work, but usually use digital meters for surveying large quantities of wood.
Knowing the MC of the flooring, jobsite and the subfloor is essential to ensure good results on a wood flooring job. In existing homes, it's also a good idea to check woodwork and structural members, because that gives a good indication of the MC a new floor will reach. If there is a spread in the readings, the results should be analyzed with some thought. Having accurate moisture meter readings can be the difference between a successful floor and a failure, so this is a tool you should never be without.
Read more about how moisture affects wood in Andrew St. James' article, "Understand the Science of Water and Wood Floors."