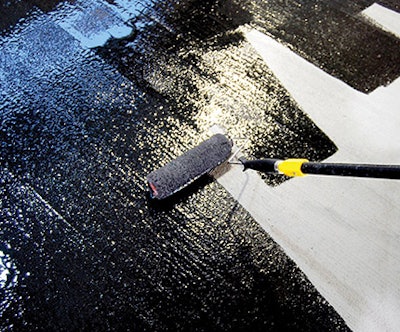
The successful installation of wood flooring over a slab is directly related to the proper preparation of the subfloor. Doing so leads to satisfied end users, and repeat business for the flooring industry. Conversely, when subfloor preparation is based on inaccurate assessments and ill-informed decisions, the results are bonding failures between the flooring and the subfloor, damaged flooring products, voided product warranties and expensive remediation. Determining the answers to six basic questions and responding appropriately can go a long way to ensure the successful preparation of a concrete subfloor.
1. Is the MC in the subfloor appropriate for the product being installed?
A critical step in prepping a concrete subfloor is determining its moisture content, because much of today's flooring is less forgiving with respect to moisture than products of the past, and many of today's adhesives have a greater sensitivity to moisture than their predecessors. As a result, today most manufacturers require more stringent pre-installation moisture testing than in the past, not only on the surface of the slab, but within it.
To determine moisture levels within the concrete subfloor, either the ASTM F2170 relative humidity (RH) moisture test or the ASTM F1869 calcium chloride moisture vapor emission rate test can be used. The RH test is generally preferred, but some manufacturers recommend one or both tests be used, and those recommendations should be followed. The most current revision of ASTM F1869 specifically excludes the use of calcium chloride tests on lightweight concrete, often referred to as gypcrete and gypsum.
The RH test requires in-situ testing probes be set at a depth of 40 percent of the thickness of the concrete subfloor. For a 6-inch slab, for example, the probes should be 2 1⁄2 inches deep. A minimum of three probes, one at the center of the concrete subfloor and the others on the perimeter, must be used for the first 1,000 square feet of flooring. An additional probe is required for each additional 1,000 square feet of subfloor surface.
A typical moisture test requires a minimum of 72 hours to achieve moisture equilibrium within the hole, with a reading after the first hour and again at the end of the testing period. Because tolerance to moisture differs from one flooring product to another, the readings, including date, time, RH percentage and room temperature, should be recorded and shared with the flooring manufacturer to ensure the moisture levels meet warranty standards for the specific flooring product.
2. Are there moisture barriers?
With new concrete subfloors, which are typically tested for moisture a few weeks prior to the flooring installation, most flooring manufacturers either require or recommend the installation of a moisture barrier under the slab. If the barrier is not compromised, moisture levels should consistently drop over a testing period. If moisture levels remain high, it is a strong signal that a moisture mitigation system approved for wood flooring may be necessary.
With existing concrete subfloors, a moisture mitigation system is often necessary. Without such a system, moisture levels can rise or fall as moisture evaporates from the slab and is then reintroduced, depending on changing climatic conditions.
When moisture emission levels exceed the maximum allowed by the wood flooring manufacturer, moisture-mitigation systems are necessary. This one-coat, epoxy resin rapid-set moisture control system can be ready to prime as soon as four hours after it is applied.
3. Are curing compounds or moisture mitigation systems an issue?
To accelerate the curing process in the fast-track construction environment prevalent today, many contractors apply curing compounds to the surface of the concrete subfloor. This practice, however, is not without issues, because curing compounds are not compatible with many adhesives. To avoid bonding issues, it is critical that curing compounds, as well as form release materials, paints, soil and other bond-breakers be mechanically removed from the surface of the concrete subfloor prior to flooring installation.
When high moisture levels are detected in the concrete subfloor, moisture mitigation systems are often employed to stop or slow moisture. Many flooring manufacturers recommend a patching compound be applied over the moisture mitigation system to meet flooring installation standards.
RELATED: Dealing With Existing Floor Coverings When Installing Wood Floors
4. Is asbestos present on the subfloor surface?
Experienced flooring contractors can quickly determine whether asbestos-containing flooring is present on the surface of a concrete subfloor. If asbestos is an issue, removing it is a necessity if it has become friable, meaning it can be easily crumbled or reduced to powder by hand pressure.
Asbestos removal should always be left to a certified or licensed asbestos abatement contractor. Not only do they know how to safely remove asbestos, they can also deal with the thorny problems of how and where to dispose of it. Asbestos is removed either with chemicals or mechanically. Each has its advantages and disadvantages. While faster and usually less expensive, the chemical removal process, if not properly done, can leave trace amounts of removal chemical, which can harm newly-installed flooring. Mechanical removal is usually more time consuming, but is often seen as the better choice because it physically removes the asbestos from the slab surface, most often by shot blasting.
5. Are old adhesives an issue?
Removal of old adhesives from a concrete subfloor is a necessity whenever flooring is replaced, primarily because old adhesives can be incompatible with newer products. For example, today's latex-based adhesives often do not bond with the older solvent-based adhesives.
Most major adhesive and flooring manufacturers recommend mechanical removal of old adhesive, eliminating the possibility of chemical residue remaining on the concrete subfloor. If a chemical removal process is used, it is important to check with the flooring manufacturer beforehand to ensure that the chemicals applied will not damage the newly installed wood flooring.
RELATED: Step by Step: How to Get a Concrete Slab Ready for Wood Floors
Slabs in poor condition must be remediated to the point where they are sufficiently flat for adhesives to bond to them before wood flooring is installed.
6. What is the condition of the subfloor?
Bad concrete subfloors can run the gamut from those that are curled and cracked to those that were jackhammered in order to run plumbing or electrical wiring. Whatever the reason, bad slabs must be remediated to the point where the surface is sufficient for the flooring adhesive to bond to it. Ceramic tile, resilient tile and sheet vinyl must be well-bonded to the subfloor and in good condition before wood flooring is installed over them.
All concrete subfloors should be structurally sound and flat to 3⁄16 inch in 10 feet before a wood floor is installed following manufacturer's guidelines. For every type of bad slab, there is a product to address it. These include both fast-setting and slower-setting compounds to address minor imperfections.
Creating a strong foundation
It has been said, "You can't build a great building on a weak foundation." That holds true, as well, for properly prepping a concrete subfloor before wood flooring installation. The time you invest doing correct prep serves as the "foundation" for a "great" wood flooring installation that will meet or exceed the expectations of both building owners and end users over the long term.