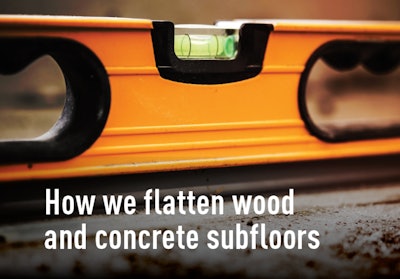
Floor flattening to industry guidelines is really important. We've all had clients who want to save a buck and ask us to cut corners on floor flattening for the sake of their budget, but that just doesn't work out well. Besides a floor failure, here in California we can have our license up for disciplinary action or, even worse, revocation if we leave an out-of-spec floor behind.
Remedying out-of-spec subfloors is our responsibility, and if the client pushes back on fixing the issue, the best decision is to walk away and live another day with our reputations and our licenses in perfect health. For those of us who work out of stores, the same is true if the store advises you to install the floor and move on with the subfloor out of spec. Even if you believe that legally the store would be on the hook, they could come after the installer on a civil basis, as well.
For my part, I never went to "floor flattening school." I simply had to learn by following the advice of those whose skills far exceeded mine. I'm no expert even now, but I have accumulated a fair share of experience chasing out-of-spec subfloors until they surrendered. As with all of us, I've learned some tricks from others, and even learned new tricks of my own on the job as I wrestled with complicated applications. I have never walked out on a tough subfloor job, but I have walked out on clients who refused to have the floor flattened because of the cost. It's that important.
How do we get to flatness?
I find that breaking down the requirements into different lengths and relatable measurements can be helpful.
If we stay within these tight parameters we are good, but how do we get there?
I can tell you what we do. For grinding a hump, we use an edger on wood subfloors and a 7-inch right-angle grinder with a diamond wheel I like (pictured below) on concrete subfloors. For filling a depression on wood subfloors, I've seen wood shims, roof shingles and drywall shims for simple depressions. For demon-possessed depressions on concrete, we use cementitious products. For challenging wood subfloors, we can use cementitious products in combination with wire lath or fiberglass fabric to add integrity—per the manufacturer's direction, of course.
I used water to keep the dust down when grinding this subfloor—even though I had a vacuum. The spatula was for picking up the slurry created, which I put in the blue container. Of course I had the level there, or else I would have had no way of knowing if I made any progress.
RELATED: How to Prove Subfloor Prep Is Necessary—and Get Paid for It
The following pages have examples from some of my jobs with subfloor prep.