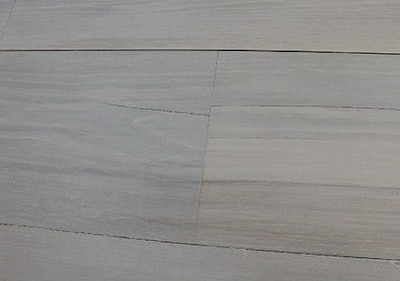
The Problem
I was called because of concerns about gaps between boards, surface splits in the veneer and inconsistency in the stain.
What Happened
The unfinished engineered white oak plank measured from 81⁄2–10 inches wide. It was delivered to the job site during construction of the luxury home in Southern California. Installation began shortly thereafter while the home was still under construction, with millwork, window, HVAC, painting and other work still being done on the home. The homeowner said he expressed concerns about gaps during installation but was told by the flooring contractor not to worry. After the glue-down installation, the flooring was stained white, and the customer had concerns about the consistency of the color.
The Inspection
The inspection took place more than a year later, and the home was still under construction. The flooring was throughout the upstairs. There were numerous side gaps throughout the floor that measured from 1⁄64–1⁄16 inch, and there was filler in the gaps. It appeared that movement had pulled apart the filler so it was on one side of the plank, exposing the gaps. The master bedroom had a wall of floor-to-ceiling windows with no coverings facing south, and there were gaps in almost every row of flooring there. This area also had cracks/splits in the face of some of the planks, and filler could be seen in the splits. Using an IR thermometer, the floor surface was found to be 90 degrees Fahrenheit. The MC of the flooring ranged from 7.2–7.8%, and the RH was 33.3%. Some planks measured on size while others were narrower.
The flooring showed a great variation in color of the stain and did not match the sample provided to the client, which had a consistent color.
RELATED: How to Prevent Wood Floor Gaps in Winter
There were many missteps in this case, including installing in the midst of construction before windows, doors and operating HVAC were in place; ignoring the customers' concerns about gaps during installation; not noticing the drastic differences in color during staining and attempting to fill the gaps with filler.
How to Fix the Floor
Raising the RH may alleviate some of the gaps between boards but won't repair the veneer splits, so this floor must be replaced.
In the Future
When a customer expresses concerns during installation, it's best to stop and find solutions immediately; the time and cost involved will only grow exponentially as the job progresses. Adhering to industry standards (such as installing after HVAC is operational) will help reduce liability. Even in a temperate climate like Southern California, engineered flooring is not bulletproof.