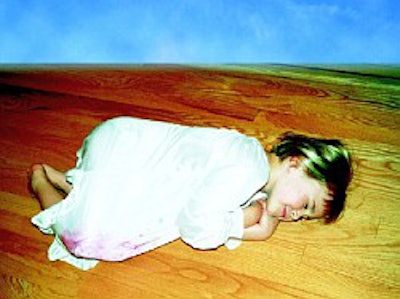
Developers of high-rise condominiumand luxury apartment complexes are under the gun from residents and potential residents to do a better job of controlling sound transmission between living quarters. Some even have faced lawsuits over the issue, so you canbe sure those developers are placing similar requirements on builders and subcontractors to provide materials that reduce sound transmission. No one is under more pressure to do so than woodflooring contractors.
Steve Becht, president of The Becht Corp. in Tewksbury, Mass., says demand for sound-control underlayment beneath wood flooring was minimal as recently as five years ago. Today, it's a standard part of his company's business. At the prestigious Trinity Place condo development project near Boston's Copley Square, Becht installed 70,000 square feet of glue-down engineered wood flooring,all of it over cork underlayment glued to concrete.
"In the Boston area, there's a real push to get more residential units in the city," Becht says. "Now that their kids have grown, a lot of affluent Baby Boomers want to move back into the city, so we're seeing an increase in building these luxury complexes."
In densely built cities like Boston, of course, there's no direction for these buildings to go but up. Wood flooring, for all its practical and fashionable advantages, is notorious for its tendency to transmit impact sound to levels below it, so everyone concerned is looking for products that effectively mitigate sound transmission.
Becht agrees that developers are becoming even more demanding about the effectiveness of sound control installations, but that flooring contractors have to rely on their suppliers to provide the documentation needed to demonstrate sound-dampening ability.
"We certainly don't have the means or the expertise to test for acoustics," Becht says. Manufacturers serious about supplying the sound-control market know they have no choice if they expect to meet the market's demand for proof of effectiveness.
"There's a lot of liability involved for everyone," says Joe Lazzaro of Bostik Findley, which sells a cork and adhesive system designed and tested for sound control. "A lot of these developers are running scared because of the lawsuits that have been filed by condo associations."
To provide flooring contractors and condo developers with the products and documentation they need, manufacturers have been moving toward testing that more accurately reflects real-world performance. Problems in the past sometimes have resulted from installations that didn't match the sound-control performance predicted in product documentation.
To achieve more accurate results, manufacturers are approaching the issue from at least two angles: Testing whole systems (rather than individual products), and doing on-site tests instead of laboratory tests.
Being Systematic
The core concept behind system testing is relatively simple: If you test a 1/4-inchor 6-mm cork product, for example, all you know for sure is how much sound the cork alone will block. You won't know how the cork will perform with an adhesive, with one adhesive versus another, or under a given wood flooring product.
Manufacturers who sell sound-control products with a system approach say they can warranty the system to perform as documented, as long as the entire system is installed as specified. Without that, they say, there's no end to the finger-pointing that begins when problems occur.
The most common systems start withan underlayment of cork, fiber matting, foam or a composite membrane. The underlayment is sometimes combined with a specified adhesive or lightweight gypsum concrete. Some systems are compatible with either nail-down, glue-down or floating floors, though the system specifications are different for each installation style.
In all cases, a perimeter isolation barrier is required to prevent sound transmission from the floor to the walls. The barrier, made from the same material as the underlayment, is installed around the perimeter of the room between the flooring and the walls.
"The perimeter barrier is probably the place where people make the most mistakes in terms of not paying attention to the details," says Ann Wicander, president of WE Cork in Exeter, N.H. "If impact sound is transmitted from the floor to the walls, you lose a lot of the effectiveness of the system."
In the Real World
Although field-test data is more difficult and expensive to obtain than lab data, manufacturers are being asked for such data more frequently. The growing demand stems from the belief that testing sound-control products in an actual structure will provide more accurate performance predictions than testing in a laboratory, regardless of how hard labs try to make their testing structures realistic.
Whether that's true or not, some developers will not accept lab-only data. A few—especially those most leery of litigation—have even taken the real-world testing concept a step further, demanding that testing be done on the site of the proposed installation. In that scenario, a sample installation must be completed in one area of the complex, then subjected to acoustic testing before final installation can begin.
"We just had to do that on a large installation in Miami," Wicander says. "Some developers are just adamantabout field testing, so they don't get sued again."
Setting Standards
The American Society for Testing and Materials recently approved new testing standards for sound transmission—standards that some believe will level the playing field and make comparisons between products more accurate. The new testing specification, called the Delta IIC, uses a standardized concrete slab, a tapping machine and a microphone linked to a computer. Lab technicians perform a baseline test with the slab alone, then a second test with the sound-control floor system in place. The difference in test results provides an IIC (Impact Insulation Class) rating for the system.
If everyone uses the same specifications in their testing, comparisons between products are easy, "but you can skew the results by making the structure unlike anything you'll find in the real world," Wicander says.
More, Not Less
Expect to see more demand for sound control underlayments as the demand keeps pace with construction growth in high-end multi-family dwellings. "Sound control is practically mandatory in all multi-family dwellings in California now," says Chris Coates, president of Coates & Associates in Novato, Calif.
Most building codes call for an IIC rating of 50 or better, although some developers are beginning to ask for more. "Many of these new developments have CC&Rs [codes, covenants and restrictions] that dictate higher IIC values than standard building codes contain," says Coates.
"Sometimes it's overkill," says Lazzaro. Wicander agrees. "In some cases, we've seen developers asking for a IIC inthe 60s," says Wicander. "Sometimes you can achieve that in a concrete structure with suspended ceilings, but you can't expect to be in the 60s with a wood-frame structure. The structure itself limits that."
Demand for sound-control products—once limited primarily to NewYork City, Miami and Southern California—is likely to spread wherever high-income people live in high-rise buildings. "We still see sales strongest in California, New York and Florida,"says Wicander, "but it's spread to areas like Denver, Chicago, Seattle and Portland as well. Actually, it's happening anywhere where there's a lot of condo development, because the push really comes from the condo associations and condo developers. That's one of the strong selling points developers are looking for in their condos—sound control."
What’s That Sound?
Building codes typically specify two types of sound-control ratings: IIC (Impact Insulation Class) and STC (Sound Transmission Class). A rating of 50 for each generally is a standard requirement. The IIC relates to sound transmitted as a result of impact on a surface—footsteps on a floor, for example. The STC relates to airborne sounds, such as voices and music. Sound-control underlayments often carry an STC rating, as well as an IIC rating. However, says Ann Wicander of WE Cork, flooring products really have a substantial effect only on impact sounds. “The underlayment really will not affect STC much,” Wicander says. “It really confuses people. The STC or airborne sound is really affected almost solely by the structure itself.”